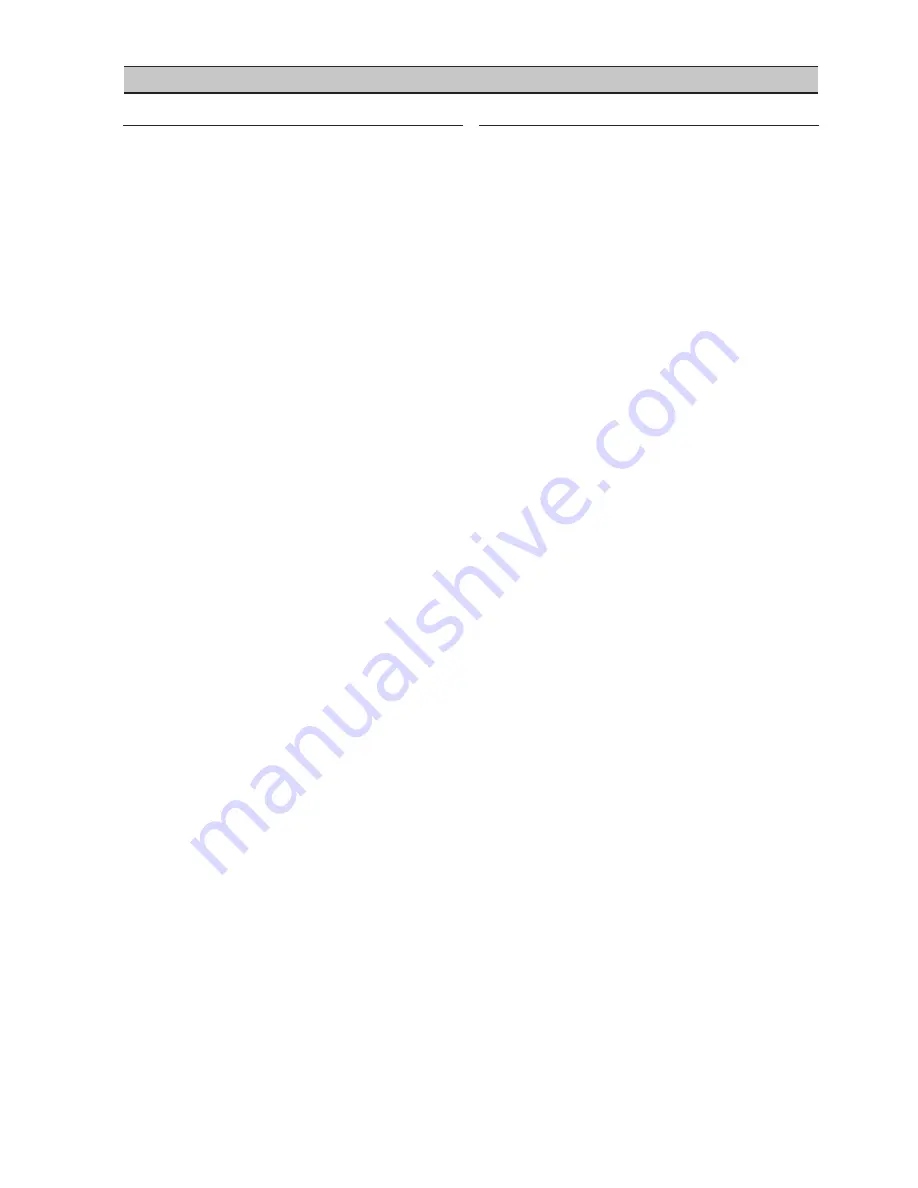
7
SECTION 6 - bEfORE yOU START
CHECK LIST
Prior to attempting installation and commissioning of the
x8I or x12I please review the following check list:
Quick Set Up Manual is available and has been
reviewed.
Application Guide is available and the correct diagrams
have been identified.
If the specific diagrams are not in the Application Guide
the specific compressor control wiring schematic will
be required to define the correct interconnection.
Operator’s Manual is available and has been reviewed.
Compressors to be connected can accept remote load /
unload commands.
Compressors to be connected have automatic Start /
Stop capability.
Correct compressor controller EPROM is installed or
available to allow Remote Control and Auto Start/Stop
(SE Controller) See Reference Table Below.
The correct wire is available to connect the x8I or x12I
with the Compressor / ir-PCB interface.
The correct wire is available to connect the x8I or x12I
with the Compressor / ir-485 and/or irv-485 Gateway.
The correct wire is available to connect the x8I or x12I
with the Optional Integration boxes.
The correct wire is available to connect the x8I or x12I
with the pressure sensor/transducer.
The x8I or x12I can be located within 330ft (100m) of
each compressor using the ir-PCB.
The ExP must be located within 33ft (100m) of x8I or
x12I.
The ExP can be located within 330ft (100m) of each
compressor using the ir-PCB.
The x8I or x12I can be located within 4000ft (1219m)
of each compressor using the ir-485 and/or irv-485
Gateway or Optional Integration boxes. (The exception
to this is connecting the Optional ExP box to the x8I or
x12I. The maximum distance is 33ft (10m) in length).
The Pressure sensor/transducer can be located
appropriately within 330ft (100m) for the x8I or x12I
Controller.
•
•
•
•
•
•
•
•
•
•
•
•
•
•
•
•
CHECK LIST GUIDANCE
Electrical Drawing For Each Compressor: It is important
to have the Electrical drawing for each compressor
so that the correct interconnect drawing can be
referenced from the Interconnect and Application
Guide.
Types of Compressors To Be Sequenced: Refer to the
Interconnect and Application Guide for specific details
on the types of compressors that can be sequenced
and their individual requirements such as Auto Restart,
Intellisys Software, etc.
ir-PCB and ir-485 and/or irv-485 Gateway Mounting:
The ir-PCB and the Gateway module is designed to
be installed within the compressor starter enclosure.
The mounting location of the ir-PCB should be away
from any high voltage connections, contactors, or
transformers.
ir-PCB, ir-485 and/or irv-485 Gateway and Compressor
Interconnections: Refer to the Interconnect and
Application Guide for specific drawings for various
compressors and the x8I or x12I. If there is not a
specific drawing available for the compressor being
sequenced at the site, please contact Technical Support
Services for assistance.
ir-PCB, ir-485 and/or irv-485 Gateway and Compressor
Interconnection Wire: The x8I or x12I Installation
kit contains 330ft (100m) of 18 gauge stranded wire
(Orange) to use for the connections between the ir-PCB
and the compressor. In most cases, this is sufficient for
most installations. If additional wire is required, any
18 gauge stranded wire can be used in lieu of the wire
provided in the kit.
x8I or x12I Installation kit also contains an interconnect
cable for the connection between the ir-485 Gateway
and the Intellisys Controller.
x8I or x12I, ExP, Ex and ir-PCB Interconnect Wire: The
cable used between the x8I or x12I and the compressor
ir-PCB interconnection is designed to use 7-conductor
shielded cable or individual wires run through earthed/
grounded metal conduit/tubing. (18 gauge wire).
The cable used between the x8I or x12I, ExP, ir-485
and/or irv-485 Gateway or any Optional Integration
Boxes is Belden 9841 (or equivalent). It should be run
in grounded conduit and should not be greater than
4000 feet (1219 meters) in length (The exception to this
is connecting the Optional ExP box to the x8I or x12I.
The maximum distance is 33ft (10m) in length).
•
•
•
•
•
•
•
Summary of Contents for X12I
Page 32: ...32 VX Box Connection VX Box Power Supply Connection...
Page 33: ......