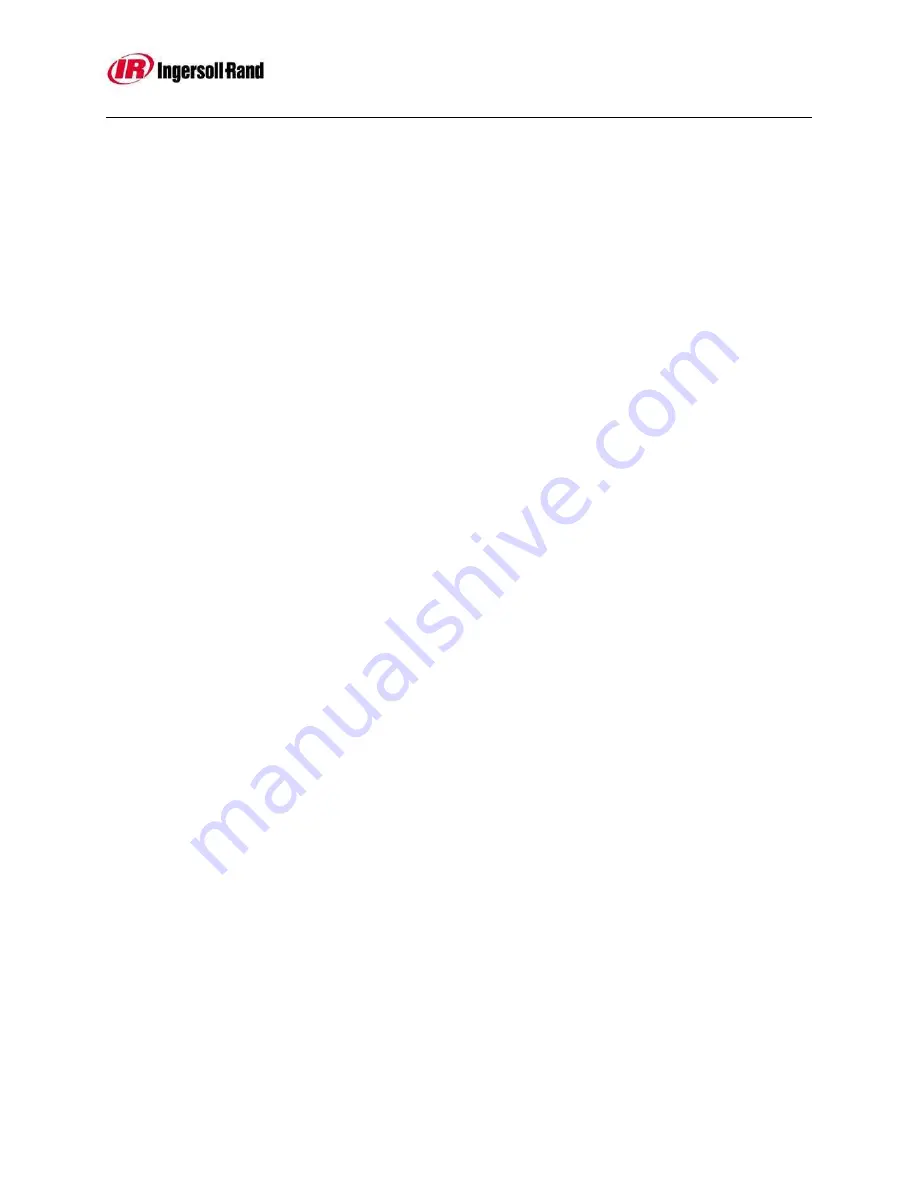
USER MANUAL
MODEL NO.: TZ730–1710
Rev. 08 – 14 September 2005
9
3. EQUIPMENT OPERATION
3.1 GENERAL OPERATING PRINCIPLES
This
I
I
n
n
g
g
e
e
r
r
s
s
o
o
l
l
l
l
-
-
R
R
a
a
n
n
d
d
®
®
dryer has two parallel adsorption chambers filled with desiccant.
While the medium is being dried flowing bottom-up in one chamber, regeneration of the
desiccant takes place from the top down in the other chamber. The changeover from
one chamber to the other is controlled by an Energy Management System (EMS) that
monitors desiccant performance by measuring the outlet air dew point. It can operate
continuously and is fully automatic.
The standard (STD) dryer has a cycle time of 10 minutes. Dryers with the Low Dew
Point (LDP) option have a 4-minute cycle time. In each case, half the cycle time is
dedicated to air drying work and the other half to desiccant regeneration, with one
chamber working to dry the air while the other regenerates. The cycle time affects air
flow and air quality. The longer cycle time allows greater saturation of the desiccant,
thereby decreasing its drying capacity over the period of the cycle. The faster cycling
provided with the LDP option ensures that the desiccant is regenerated more frequently,
thereby enhancing its drying performance. The dryer is configured at the factory. The
principles of operation are the same for both the STD and the LDP dryer.
Wet air enters the working desiccant chamber (it can be either the left or right) at the
inlet switching valve (bottom) and is dried as it flows upward through the desiccant bed.
Dry air exits the dryer through the outlet check valve.
At the outlet of the working chamber, a portion of the dry air (i.e., purge air) is diverted
to the regenerating chamber. That purge air, at near atmospheric pressure, will remove
previously adsorbed moisture as it flows downward through the desiccant bed and exits
through the purge exhaust muffler.
The purge air is controlled by a purge adjusting valve and purge orifices located in the
purge line.
Purge pressure is indicated on the purge pressure gauge.
Refer to
Appendix C for instructions on adjusting the purge rate.
Near the end of each half cycle, the chamber being regenerated will be repressurized.
For this to occur, the exhaust valve of the chamber being regenerated closes while
purge air continues to flow.
Repressurizing the regenerated chamber to operating
pressure before placing it into service minimizes fluidization of the desiccant and helps
prevent desiccant abrasion which causes desiccant dust to prematurely block filter
elements.
Chamber switchover takes place when both towers are fully pressurized.
This
minimizes desiccant movement which, in turn, minimizes creation of dust.
When switchover is complete, the regenerated tower will be placed into service and the
exhausted tower will begin a depressurization/regeneration cycle.
Summary of Contents for TZ1050
Page 2: ...ii...
Page 4: ...USER MANUAL MODEL NO TZ730 1710 Rev 08 14 September 2005 iv...
Page 6: ...USER MANUAL MODEL NO TZ730 1710 Rev 08 14 September 2005 vi...
Page 12: ...USER MANUAL MODEL NO TZ730 1710 Rev 08 14 September 2005 6...
Page 22: ...USER MANUAL MODEL NO TZ730 1710 Rev 08 14 September 2005 16...
Page 27: ...USER MANUAL MODEL NO TZ730 1710 Rev 08 14 September 2005 21 7 DRAWINGS...
Page 28: ...USER MANUAL MODEL NO TZ730 1710 Rev 08 14 September 2005 22...
Page 43: ......