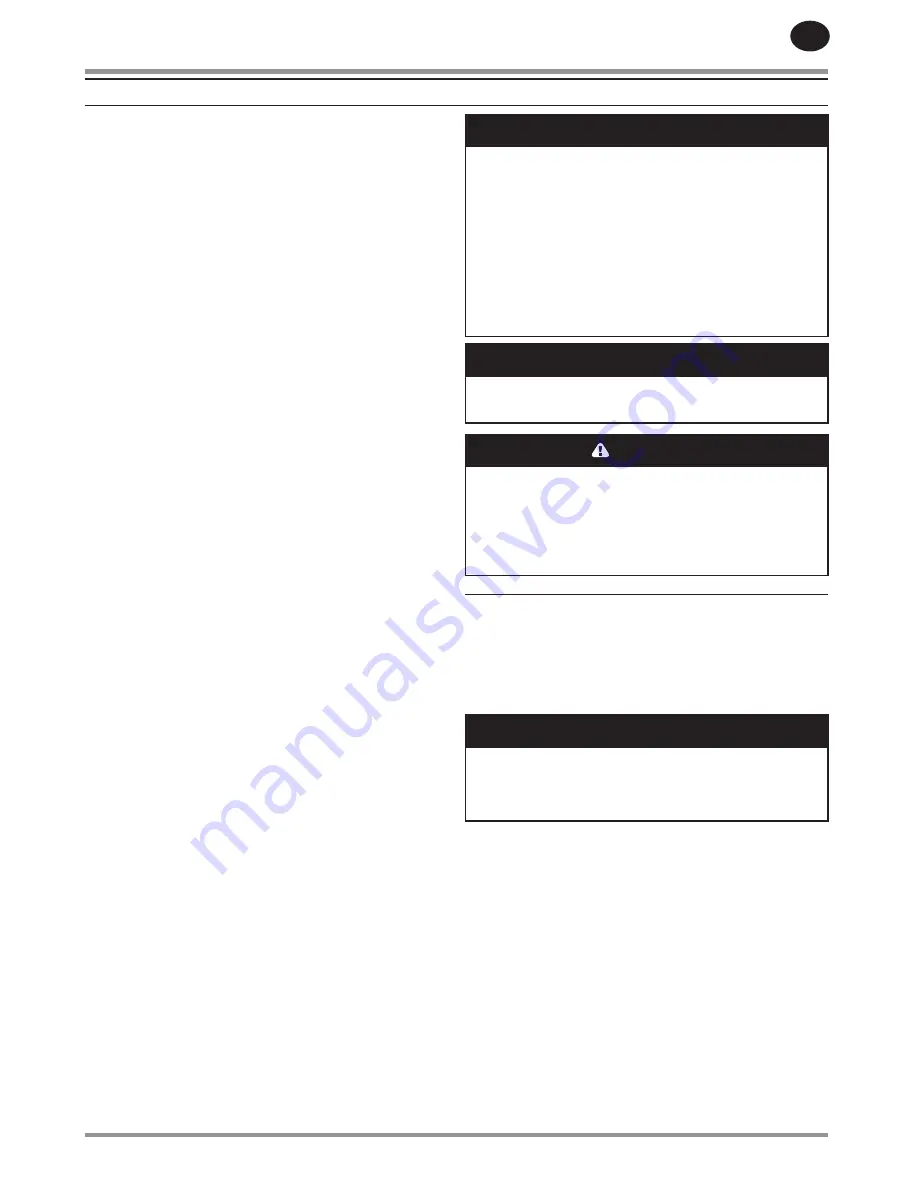
80446339 Rev E
EN-9
EN
The compressor is an electric motor driven, contact cooled screw compressor,
complete with all necessary components piped, wired and baseplate
mounted. It is a totally self contained air compressor package.
The standard compressor is designed to operate in an ambient range of 2 °C
to 46 °C (35 °F to 115 °F). The standard maximum temperature of 46 °C
(115 °F) is applicable up to an elevation of 1000 m (3280 ft) above sea level.
Above this altitude, significant reductions in ambient temperature are
required if a standard motor is to be used.
The compressor is managed by the onboard electronic controller. The
controller and drive system operate together to vary the speed of the
compressor to deliver compressed air at the target pressure.
For fixed speed (FS) models, the capacity is automatically controlled via
‘ON-OFF LINE’. The compressor will operate to maintain a set discharge line
pressure and is provided with an auto restart system for use in plants where
air demand varies widely.
Panel instrumentation is provided to indicate the compressor operating
conditions and general status.
The air/coolant mixture discharges from the compressor into the separation
system. This system removes all but a few ppm of the coolant from the
discharge air. The coolant is returned to the cooling system and the air passes
to the after-cooler and out of the compressor through the moisture separator.
Air is pulled into the compressor by the cooling blower and through the
coolant cooler and after-cooler.
By cooling the discharge air, much of the water vapor naturally contained in
the air is condensed and is drained from the built-in moisture separator and
drain.
The coolant system consists of a sump, cooler, thermostatic valve and a
filter. When the compressor is operating, coolant is forced by air pressure
from the separator tank to the thermostatic element. The position of the
element (a direct result of coolant temperature) will determine whether the
coolant circulates through the cooler, bypasses the cooler, or mixes the two
paths together to maintain an optimum compressor discharge temperature.
This temperature is controlled to preclude the possibility of water vapor
condensing. By injecting coolant at a sufficiently high temperature, the
discharge air coolant mixture temperature will be kept above the dew point.
For variable speed drive models, the system is enhanced by a control logic
that varies the cooling blower speed dependent on the intake and discharge
temperatures and hence controls the injection temperature even closer while
saving blower motor energy.
The compressor is provided with a temperature sensor which will shut the
compressor down in case of excessive temperature. This setting is typically
109 °C (228 °F).
Effective coolant filtration is provided by the use of a screw on, heavy duty
coolant filter.
NOTICE
Standard air compressors are factory filled with compressor coolant.
It is recommended to perform a coolant analysis every 2000 hours or
3 months to monitor condition and determine when to change the
coolant. If an analysis is not performed, the recommended coolant
change interval is 8000 hours or two years, whichever comes first.
For compressors supplied with optional food grade coolant, it is
recommended to perform a coolant analysis every 500 hours or every
month to monitor condition and determine when to change the
coolant. If an analysis is not performed, the recommended coolant
change intervals is 2000 hours or six months, when utilizing the food
grade filter supplied with the compressor. For compressors running
food grade coolant without the food grade filter, the change interval
should be 1000 hours or three months, whichever comes first.
NOTICE
Fixed speed compressors should not be connected to variable speed
drives. Please contact your local Ingersoll Rand representative before
inverter duty conversion.
CAUTION
For fixed speed models, the compressor may not reach its normal
operating temperature during periods of low demand. Sustained
operation at low demand can result in the buildup of condensate in
the coolant. If this situation occurs, the lubricating characteristics
of the coolant can be impaired, which may lead to damage of the
compressor.
The compressor should be allowed ample loading time.
INTEGRATED DRYER OPERATION
In the default mode, the dryer is non-cycling. The stop button must be
pressed to shut-off the dryer.
In the energy efficient mode, the dryer may run up to 6 minutes before
it shuts off automatically during the Start/Stop mode of the compressor
package. Note the dryer could be off for an extended period if the
compressor needs to come back on right away.
NOTICE
If ISO Class 4 dew point standards are critical to your application,
run the compressor in unload mode (fixed speed) or idle mode
(variable speed) for one minute at startup to allow the dryer to reach
the required dew point before the compressor begins providing
compressed air.
GENERAL INFORMATION
RELEASED 01/Nov/2018 12:06:37 GMT