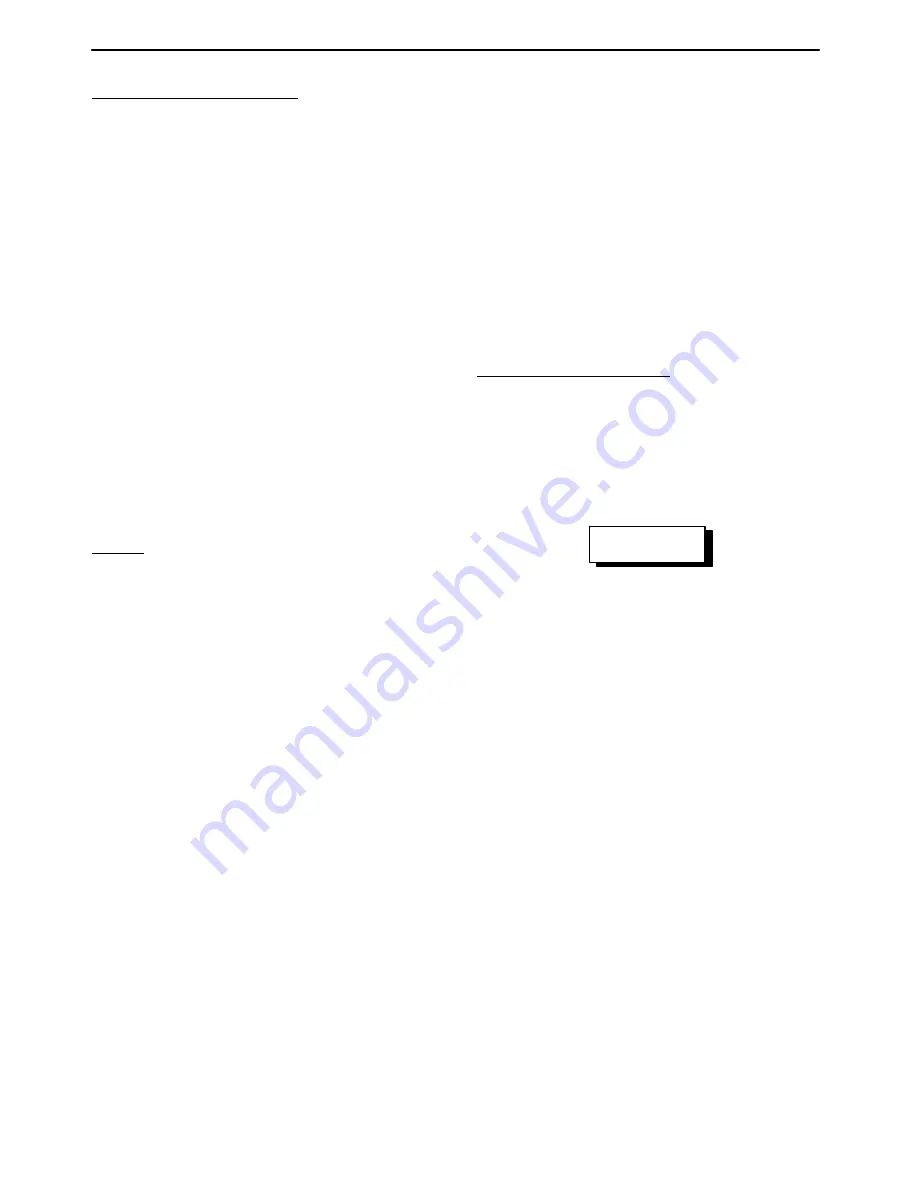
38
( )
Book: 22305593 (8/03)
COMPRESSOR OIL COOLER
The compressor lubricating and cooling oil is cooled
by means of the fin and tube--type oil cooler, located
below the radiator. The lubricating and cooling oil,
flowing internally through the core section, is cooled by
the air stream from the cooling fan flowing past the
core section. When grease, oil and dirt accumulate on
the exterior surfaces of the oil cooler, its efficiency is
impaired.
Each month it is recommended that the oil cooler be
cleaned by directing compressed air which contains a
nonflammable, non--caustic safety solvent through the
core of the oil cooler. This should remove the
accumulation of grease, oil and dirt from the exterior
surfaces of the oil cooler core so that the entire cooling
area can transmit the heat of the lubricating and
cooling oil to the air stream.
In the event foreign deposits, such as sludge and lac-
quer, accumulate in the oil cooler to the extent that its
cooling efficiency is impaired, a resulting high dis-
charge air temperature is likely to occur, causing shut
down of the unit. To correct this situation it will be nec-
essary to clean it using a cleaning compound in accor-
dance with the manufacturer’s recommendations.
HOSES
Each month it is recommended that all of the intake
lines to and from the air cleaners, the engine cooling
system hoses and all of the flexible hoses used for alr,
oil, and fuel be inspected.
To ensure freedom from air leaks, all rubber hose
joints and the screw--type hose clamps must be
absolutely tight.
Regular inspection of these
connections for wear or deterioration is necessary.
Premature wear of both the engine and compressor is
ASSURED whenever dust--laden air is permitted to
enter the engine’s combustion chamber or the
compressor intake.
The flexible hoses used in the fuel, oil and air lines on
these units are primarily used for their ability to accom-
modate relative movement between components. It is
important they be periodically inspected for wear and
deterioration. It is also important the operator does
not use the hoses as convenient hand hold or steps.
Such use can cause early cover wear and hose failure.
Piping systems operating at less than 150 psi (1050
kPa) may use a special nylon tubing. The associated
fittings are also of a special “push--in” design. If so,
features are as follows:
Pulling on the tubing will cause the inner sleeve to with-
draw and compress, thus tightening the connection.
The tubing can be withdrawn only while holding the
sleeve against the fitting. The tubing can be removed
and replaced numerous times without losing its seal-
ing ability.
To install the nylon tubing, make a mark (with tape or
grease pencil) approximately 7/8 inch from the end of
the tubing. Insert the tubing into the sleeve and “push--
in” past the first resistance to the bottom. The mark
should be approximately 1/16 inch from the sleeve, for
the 3/8 inch O.D. tubing; 1/8 inch for the 0.25 inch O.D.
tubing. This will ensure that the tubing is fully engaged
in the sealing mechanism.
COMPRESSOR OIL FILTER
The oil filter must be replaced every 500 hours of
operation or six (6) months, whichever comes first.
To service the oil filters it will first be necessary to shut
the unit down. Wipe off any external dirt and oil from
the exterior of the filter to minimize any contamination
from entering the lubrication system. Proceed as
follows:
WARNING
High pressure air can cause severe injury or death
from hot oil and flying parts. Always relieve pres-
sure before removing caps, plugs, covers or other
parts from pressurized air system.
1.
Open the service air valve(s) to ensure that
system is relieved of all pressure. Close the
valve(s).
2.
Turn the spin--on filter element counterclockwise
to remove it from the filter housing. Inspect the
filter.
NOTICE
If there is any indication of formation of varnishes,
shellacs or lacquers on the oil filter element, it is a
warning the compressor lubricating oil has improper
characteristics and should be immediately changed.
3. Inspect the oil filter head to be sure the gasket was
removed with the oil filter element. Clean the gasket
seal area on the oil filter head.
NOTICE
Installing a new oil filter element when the old gasket
remains on the filter head, will cause an oil leak and
can cause property damage.
Summary of Contents for P185WIR
Page 69: ...SECTION 11 PARTS LIST...
Page 70: ......
Page 71: ......
Page 72: ......
Page 73: ......
Page 74: ......
Page 75: ......
Page 76: ......
Page 77: ......
Page 78: ......
Page 79: ......
Page 80: ......
Page 81: ......
Page 82: ......
Page 83: ......
Page 84: ......
Page 85: ......
Page 86: ......
Page 87: ......
Page 88: ......
Page 89: ......
Page 90: ......
Page 91: ......
Page 92: ......
Page 93: ......
Page 94: ......
Page 95: ......
Page 96: ......
Page 97: ......
Page 98: ......
Page 99: ......
Page 100: ......
Page 101: ......
Page 102: ......
Page 103: ......
Page 104: ......
Page 105: ......
Page 106: ......
Page 107: ......
Page 108: ......
Page 109: ......
Page 110: ......
Page 111: ......
Page 112: ......
Page 113: ......
Page 114: ......
Page 115: ......
Page 116: ......
Page 117: ......
Page 118: ......
Page 119: ......