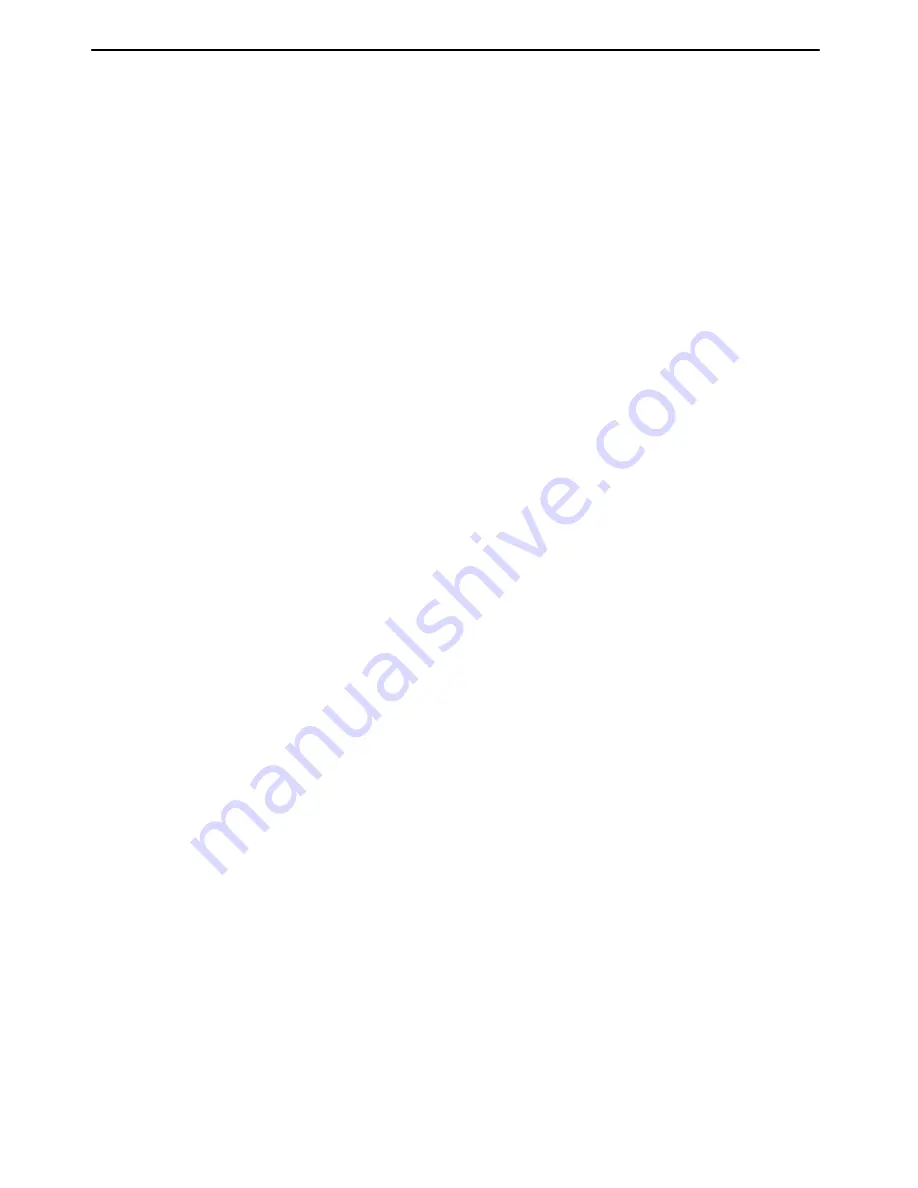
24
( )
Book: 22305593 (8/03)
MAINTENANCE RECOMMENDATION:
Some Ingersoll--Rand Company non--road engines
are certified by the United States Environmental
Protection Agency and California Air Resource Board
to comply with smoke and gaseous emission stan-
dards prescribed by Federal laws at the time of
manufacture.
The engine is certified if it has a special certification
label. An INGERSOLL--RAND Dealer can also inform
you if the engine is certified.
Efficiency of emission control and engine perfor-
mance depends on adherence to proper operation
and maintenance recommendations and use of rec-
ommended fuels and lubrication oils. It is recom-
mended that major adjustments and repair be made
by your authorized INGERSOLL--RAND Dealer.
Various chemical fuel additives, which claim to reduce
visible smoke, are available commercially. Although
additives have been used by individuals to solve
some isolated smoke problems in the field, they are
not recommended for general use.
Federal smoke regulations require that engines be
certified without smoke depressants.
The corrective steps taken immediately on discovery
of worn parts, which may affect emission levels, will
help assure proper operation of emission control sys-
tems. The use of genuine INGERSOLL--RAND parts
is recommended. Suppliers of non--INGERSOLL--
RAND parts must assure the owner that the use of
such parts will not adversely affect emission levels.
Regular maintenance intervals, along with special
emphasis on the following items, are necessary to
keep exhaust emissions within acceptable limits for
the useful life of the engine. Refer to the Maintenance
Section of this manual. If the engine is operating un-
der severe conditions, adjust the maintenance sched-
ule accordingly. See your authorized INGERSOLL--
RAND Dealer to help analyze your specific applica-
tion, operating environment and maintenance sched-
ule adjustments.
The following is an explanation of maintenance for
emission--related components.
See the Maintenance Schedule for the specific inter-
val for the following items.
FUEL INJECTION PUMPS OR NOZZLES – Fuel in-
jection pumps or nozzles are subject to tip wear as a
result to fuel contamination. This damage can cause
an increase in fuel consumption, the engine to emit
black smoke, misfire or run rough. Inspect, test and
replace if necessary. Fuel injection pumps can be
tested by an authorized INGERSOLL--RAND Dealer.
TURBOCHARGER – Check for any unusual sound or
vibration in the turbocharger. Inspect inlet and ex-
haust piping and connections. Check bearing condi-
tion and perform maintenance as described in the
Maintenance Schedule.
Slow engine response and low power may indicate a
need for adjustment or repair. Your INGERSOLL--
RAND Dealer is equipped with the necessary tools,
personnel, and procedures to perform this service.
Owner is encouraged to keep adequate maintenance
records, but the absence of such, in and of itself, will
not invalidate the warranty.
The machine or equipment owner may perform rou-
tine maintenance, repairs and other non--warranty
work or have it done at any repair facility. Such non--
warranty work need not e performed at a designated
warranty station in order for the warranty to remain in
force.
CUSTOMER ASSISTANCE – EMISSION CONTROL
SYSTEM WARRANTY:
Ingersoll--Rand Company aims to ensure that the
Emission Control Systems Warranty is properly
administered. In the event that you do not receive the
warranty service to which you believe you are entitled
under the Emission Control Systems Warranty, call or
write:
Ingersoll--Rand Company
P.O. Box 868
Mocksville, NC 27028
Tel.: 336--751--3561
Authorized Dealers are recommended for major
maintenance and repair work as they are staffed with
trained personnel, proper tools and are aware of the
latest maintenance methods and procedures. Own-
ers and others who desire to perform their own work
should purchase a Service Manual and obtain current
service information from their INGERSOLL--RAND
Dealer.
Summary of Contents for P185WIR
Page 69: ...SECTION 11 PARTS LIST...
Page 70: ......
Page 71: ......
Page 72: ......
Page 73: ......
Page 74: ......
Page 75: ......
Page 76: ......
Page 77: ......
Page 78: ......
Page 79: ......
Page 80: ......
Page 81: ......
Page 82: ......
Page 83: ......
Page 84: ......
Page 85: ......
Page 86: ......
Page 87: ......
Page 88: ......
Page 89: ......
Page 90: ......
Page 91: ......
Page 92: ......
Page 93: ......
Page 94: ......
Page 95: ......
Page 96: ......
Page 97: ......
Page 98: ......
Page 99: ......
Page 100: ......
Page 101: ......
Page 102: ......
Page 103: ......
Page 104: ......
Page 105: ......
Page 106: ......
Page 107: ......
Page 108: ......
Page 109: ......
Page 110: ......
Page 111: ......
Page 112: ......
Page 113: ......
Page 114: ......
Page 115: ......
Page 116: ......
Page 117: ......
Page 118: ......
Page 119: ......