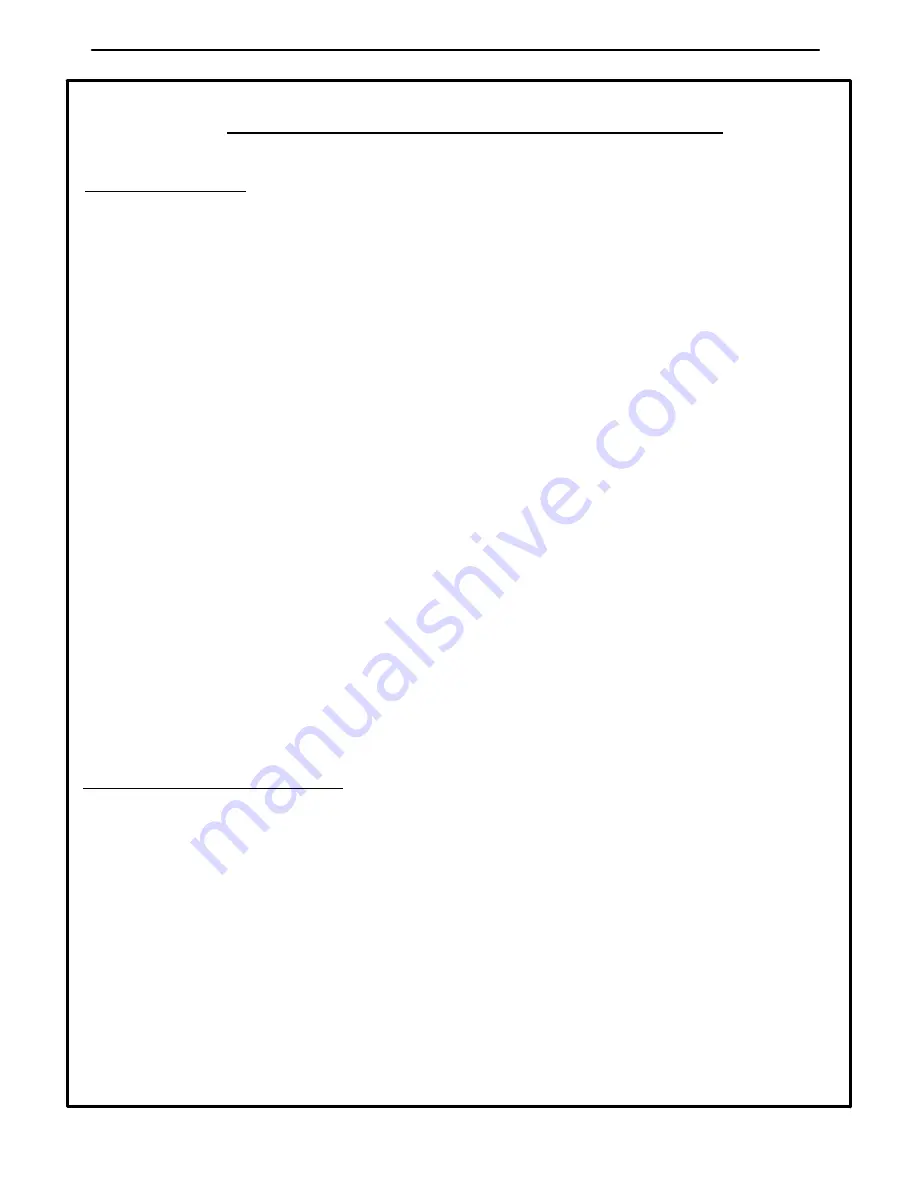
35
( )
Book 22442552 (7/03)
Section 8 -- Trouble Shooting
Trouble shooting for a portable air compressor
is an organized study of a particular problem or
series of problems and a planned method of
procedure for investigation and correction.
The trouble shooting chart that follows
includes some of the problems that an
operator may encounter during the operation
of a portable compressor.
The chart does not attempt to list all of the
troubles that may occur, nor does it attempt to
give all of the answers for correction of the
problems. The chart does give those problems
that are most apt to occur. To use the trouble
shooting chart:
A.
Find the “complaint” depicted as a bold
heading.
B.
Follow down that column to find the po-
tential cause or causes. The causes are
listed in order to suggest an order to fol-
low in trouble shooting.
INTRODUCTION
ACTION PLAN
A. Think Before Acting
Study the problem thoroughly and ask yourself
these questions:
(1) What were the warning signals that preceded
the trouble?
(2) Has a similar trouble occurred before?
(3) What previous maintenance work has been
done?
(4) If the compressor will still operate, is it safe to
continue operating it to make further checks?
B. Do The Simplest Things First
Most troubles are simple and easily corrected. For
example, most complaints are “low capacity” which may
be caused by too low an engine speed or “compressor
over-- heats” which may be caused by low oil level.
Always check the easiest and most obvious things first;
following this simple rule will save time and trouble.
D. Find And Correct Basic Cause
After a mechanical failure has been corrected, be sure to
locate and correct the cause of the trouble so the same
failure will not be repeated. A complaint of “premature
breakdown” may be corrected by repairing any improper
wiring connections, but something caused the defective
wiring. The cause may be excessive vibration.
C. Double Check Before Disassembly
The source of most compressor troubles can be traced
not to one component alone, but to the relationship of one
component with another. Too often, a compressor can be
partially disassembled in search of the cause of a certain
trouble and all evidence is destroyed during disassembly.
Check again to be sure an easy solution to the problem
has not been overlooked.
Note
: For trouble shooting electrical problems, refer to
the Wiring Diagram Schematic.
Summary of Contents for P110WIR
Page 39: ......
Page 40: ......
Page 41: ......
Page 42: ......
Page 43: ......
Page 44: ......
Page 45: ......
Page 46: ......
Page 47: ......
Page 48: ......
Page 49: ......
Page 50: ......
Page 51: ......
Page 52: ......
Page 53: ......
Page 54: ......
Page 55: ......
Page 56: ......
Page 57: ......
Page 58: ......
Page 59: ......
Page 60: ......
Page 61: ......
Page 62: ......