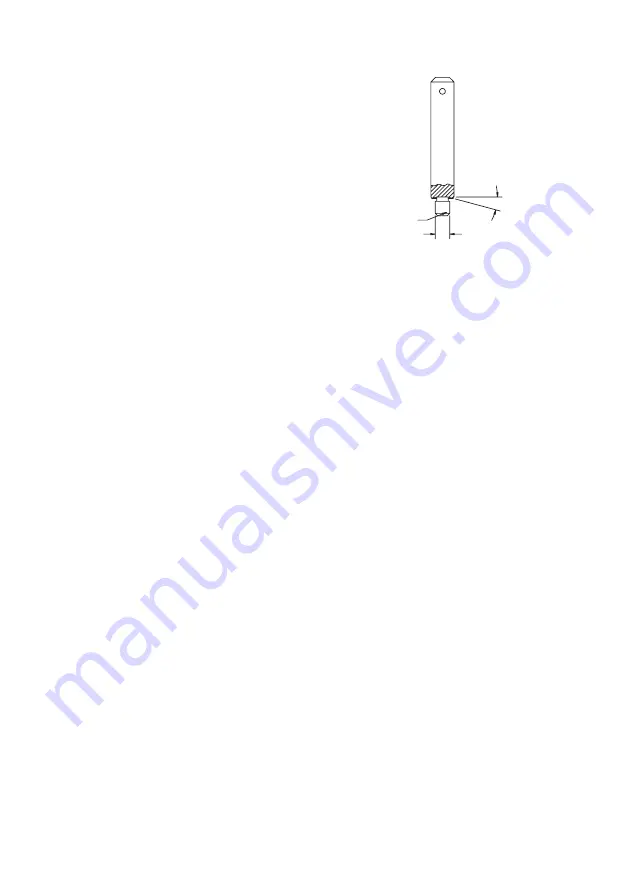
03528635_ed7
11
3. Grasp the Gear Box Frame (19) and carefully separate the
assembled Frame and Gear Box Cover Assembly (38) from the
Gear Box (18) and set it aside. If the First Stage Intermediate
Gear (21) remains with the Gear Box Frame, make certain it does
not drop onto any hard surfaces or other gearing.
4. Remove the Gear Box Gasket (20).
5. Lift the First Stage Intermediate Gear out of the Gear Box. Pull
the First Stage Intermediate Gear Rear Bearing (22) and First
Stage Intermediate Gear Front Bearing (23) off the hubs of the
Intermediate Gear. If the Bearings are frozen on the hubs, use a
bearing puller to remove them.
6. Carefully separate the Gear Box Cover Assembly from the Gear
Box Frame and remove the Gear Case Gasket. Be careful not
to allow the Motor Shaft Thrust Bearing Race (32) or the Motor
Shaft Thrust Bearing (33) to slide off the Motor Shaft and become
damaged.
7. Remove the Third Stage Intermediate Gear (31) and the two Third
Stage Intermediate Gear Bearings (30) from either the Gear Box
Frame or the Gear Box Cover Assembly. Pull the two Bearings
from the shafts of the Gear. If the Bearings are frozen on the
shafts, use a bearing puller to remove them.
8. Pull the Intermediate Gear Pinion Rear Bearing (24) off the rear
hub of the Intermediate Gear Pinion (27).
9. Using a gear puller, pull the Second Stage Intermediate Gear (25)
from the rear hub of the Intermediate Gear Pinion. Remove the
two Shaft Keys (26).
10. Push the Intermediate Gear Pinion out the motor shaft end of the
Gear Box Frame.
11. Pull the Intermediate Gear Pinion Front Bearing (29) off the Pinion
and if the Intermediate Gear Pinion Roller Bearing (28) must be
replaced, pull it from the Pinion.
12. If the Motor Shaft Thrust Bearing and Bearing Race have not been
removed, remove them from the Shaft.
13. Push the assembled Motor Shaft out of the Gear Box Cover
Assembly.
14. Pull the Motor Shaft Front Bearing (35) off the front hub of the
Motor Shaft.
15. Using a hooked tool, pull the Motor Shaft Seal (39) out of the
Gear Box Cover.
Assembly
General Instructions
1. Always press on the inner ring of a ball-type bearing when
installing the bearing on a shaft.
2. Always press on the outer ring of a ball-type bearing when
pressing the bearing into a bearing recess.
3. Whenever grasping a tool or part in a vise, always use leather-
covered or copper-covered vise jaws. Take extra care not to
damage threads or distort housings.
4. Except for bearings, clean every part and wipe every part with a
thin film of oil before installation.
5. Check every bearing for roughness. If an open bearing must be
cleaned, wash it thoroughly clean suitable solution and dry with
a clean cloth. Sealed or shielded bearings should not be cleaned.
Work grease into every bearing before installation.
6. Apply a film of O-ring lubricant to every O-ring before installation.
7. Unless otherwise noted, always press on the stamped end of a
needle bearing when installing a needle bearing into a recess.
Use a bearing inserting tool similar to the one shown
in Dwg. TPD786.
Needle Bearing Inserting Tool
Shoulder to
regulate depth
15°
Pilot to fit i.d. of bearing.
Length of pilot to be
approximately 1/8” less
than length of bearing.
(Dwg. TPD786)
Assembly of Series 92NB and 92RB Gearing
1. Using a bearing inserting tool, press the Intermediate Gear Pinion
Roller Bearing (28) into the Intermediate Gear Pinion (27).
2. Using a piece of tubing that contacts the outer ring of the
Intermediate Gear Pinion Bearing (29), press the Bearing
into the large bearing recess in the spindle side of the
Gear Box Frame (19).
3. Insert the shaft of the Intermediate Gear Pinion through the
Bearing and Frame, and rest the assembly on the table of an
arbor press with the pinion shaft upward and the gear end face of
the pinion supported.
4. Insert the two Second Stage Intermediate Gear Keys (26) into the
slots in the shaft and press the Second Stage Intermediate
Gear (25) onto the pinion shaft capturing the Gear Box Frame
within the assembly.
5. Using a piece of tubing that contacts the inner ring of the Third
Stage Intermediate Gear Bearing (30), press a Bearing onto each
shaft of the Third Stage Intermediate Gear (31).
6. Place the assembled Gear Box Frame on a workbench with the
roller bearing end of the Pinion upward.
7. Position the Bearing nearest the large spline on the shaft of Third
Stage Intermediate Gear above the bearing recess in the Gear Box
Frame. Engage the large spline of the Gear with the spline of the
Pinion while pushing the Bearing into the recess.
8. Using a piece of tubing that contacts the inner ring of the Motor
Shaft Front Bearing (35), press the Bearing onto the output end of
the Motor Shaft (36).
9. Install the Motor Shaft Thrust Bearing (33) followed by the
Motor Shaft Thrust Bearing Race (32) onto the opposite end of
the Motor Shaft and insert the assembled Shaft, Bearing Race
leading, into the Pinion Roller Bearing.
10. Place one of the Gear Box Gaskets (20) onto the Gear Box Frame
making certain the Gasket fits over the alignment pin in the
Frame and fits well around the large, raised alignment hub.
11. Using a dowel, push the Motor Shaft Seal (39), small opening
leading, into the recess in the Gear Box Cover Assembly (38).
12. Position the Cover over the Box Frame and install the Seal on
the Motor Shaft by bringing the Cover down against the Gasket.
Make certain the alignment pin and hub on the Frame enter the
hole and recess in the Cover.
13. Turn the assembly over so that the output end of the Motor Shaft
is downward.
14. Using a piece of tubing that contacts the inner ring of the First
Stage Intermediate Gear Front Bearing (23), press the Bearing
onto the shaft adjacent to the small spline of the First Stage
Intermediate Gear (21).
15. Using a piece of tubing that contacts the inner ring of the First
Stage Intermediate Gear Rear Bearing (22), press the Bearing
onto the shaft adjacent to the large spline of the First Stage
Intermediate Gear (21).
Summary of Contents for MULTI-VANE 92N Series
Page 7: ...03528635_ed7 ZH TPB491 4 3 2 1 2 TPB491...
Page 13: ...Notes...
Page 14: ...Notes...
Page 15: ...Notes...