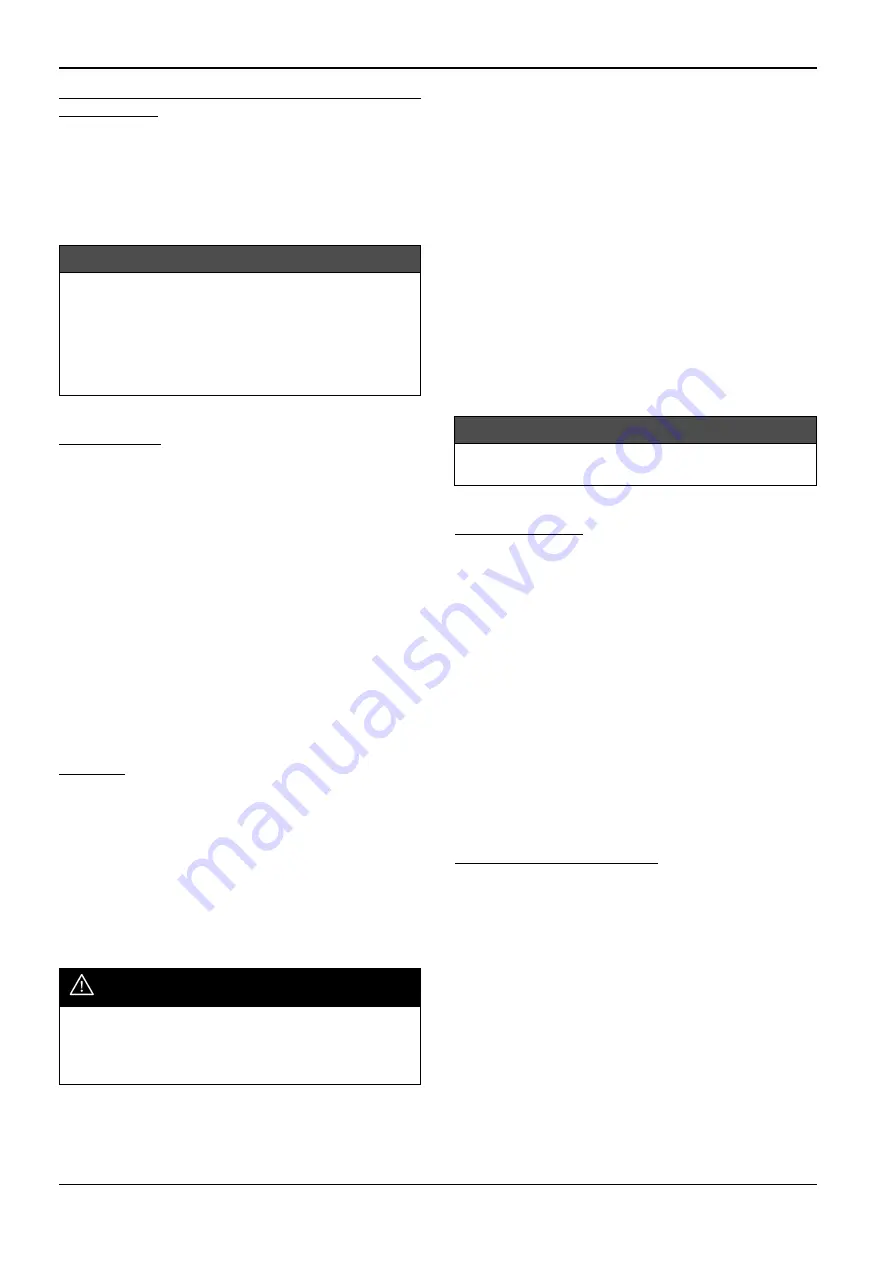
Maintenance
Lightsource LT6K
26
23201387 (03/05)
Operation and Maintenance Manual
Re-adjusting the overrun braking system (KNOTT
Running Gear)
1.
Re-adjustment of the wheel brakes will
compensate for brake lining wear. Follow the
procedure described in 2: Brake Shoe Adjustment.
2.
Check the play in the brake linkage [7] and re-
adjust if necessary.
Re-adjustment
1.
The handbrake lever [1] should be engaged
forcefully several times to set the braking system.
2.
Check the setting of the brake equalisation
assembly [8], which should be at right angles to the
pulling direction.
3.
Check the play in the brake linkage [7] again,
ensuring that there is no play in the brake linkage
and that it is adjusted without pre-tension.
4.
Check the position of the hand brake lever [1],
cable [5] (with little play) and the compression
spring [9] (only slight pre-tension). The start of
resistance of the handbrake lever should be
approximately 10-15mm above the horizontal
position.
Final Test
1.
Check the fastenings on the transmission system
(cables, brake equalization system and linkage).
2.
Apply the handbrake while rolling the machine
forward, travel of the handbrake lever up to 2/3 of
maximum is allowed.
3.
Check the handbrake cable [5] for a small amount
of play and adjust if necessary (variable height
only).
Running Gear Wheel Bearings
Wheel bearings should be packed with grease every 6
months. The type of grease used should conform to
Specification MIL-G-10924.
Instruments
Inspect the instrument lamps, gauges and switches
prior to start-up and during operation to ensure proper
functioning.
Cleaning Instructions (General)
Keeping the generator set clean of any oil and dirt is
recommended for both appearance and maximum
service life of the equipment. The frequency of cleaning
will be dependent on local conditions and the severity
and frequency of operation.
Exterior finish care
This unit was painted and heat cured at the factory with
a high quality, thermoset polyester powder coating.
The following care will ensure the longest possible life
from this finish.
1.
If necessary to remove dust, pollen, etc. from
housing, wash with water and soap or dish washing
liquid detergent. Do not scrub with a rough cloth,
pad, etc.
2.
If grease removal is needed, a fast evaporating
alcohol or chlorinated solvent can be used. Note:
This may cause some dulling of the paint finish.
3.
If the paint has faded or chalked, the use of a
commercial grade, non-abrasive car wax may
partially restore the color and gloss.
Field repair of the texture paint
1.
The sheet metal should be washed and clean of
foreign material and then thoroughly dried.
2.
Clean and remove all grease and wax from the area
to be painted using Duponts 3900S Cleaner prior to
sanding.
3.
Use 320 grit sanding paper to repair any scratches
or defects necessary.
4.
Scuff sand the entire area to be painted with a red
scotch brite pad.
5.
Wipe the area clean using Duponts 3900S.
6.
Blow and tack the area to be painted.
IMPORTANT
Check the brake actuators and cables [11]. The
brake actuators must not be pre-tensioned.
Excessive operation of the handbrake lever,
which may have been caused by worn brake
linings, must not be corrected by re-adjusting
(shortening) the brake linkage [7]
WARNING
Check the wheel nut torque 20 miles (30
kilometres) after refitting the wheels. Wheel
torque moment (screw size M12 X 1,5) 90 ± 5 Nm
(66 ± 4 ft/lbf).
IMPORTANT
Do not use high pressure water, steam or solvent
on the exterior finish of the unit housing.
Summary of Contents for LT6K
Page 3: ...22545495 03 05 3 Lightsource LT6K Operation and Maintenance Manual...
Page 13: ...Safety Lightsource LT6K 12 23201387 03 05 Operation and Maintenance Manual...
Page 19: ...Operating Instructions Lightsource LT6K 18 23201387 03 05 Operation and Maintenance Manua...
Page 29: ...Maintenance Lightsource LT6K 28 23201387 03 05 Operation and Maintenance Manual...