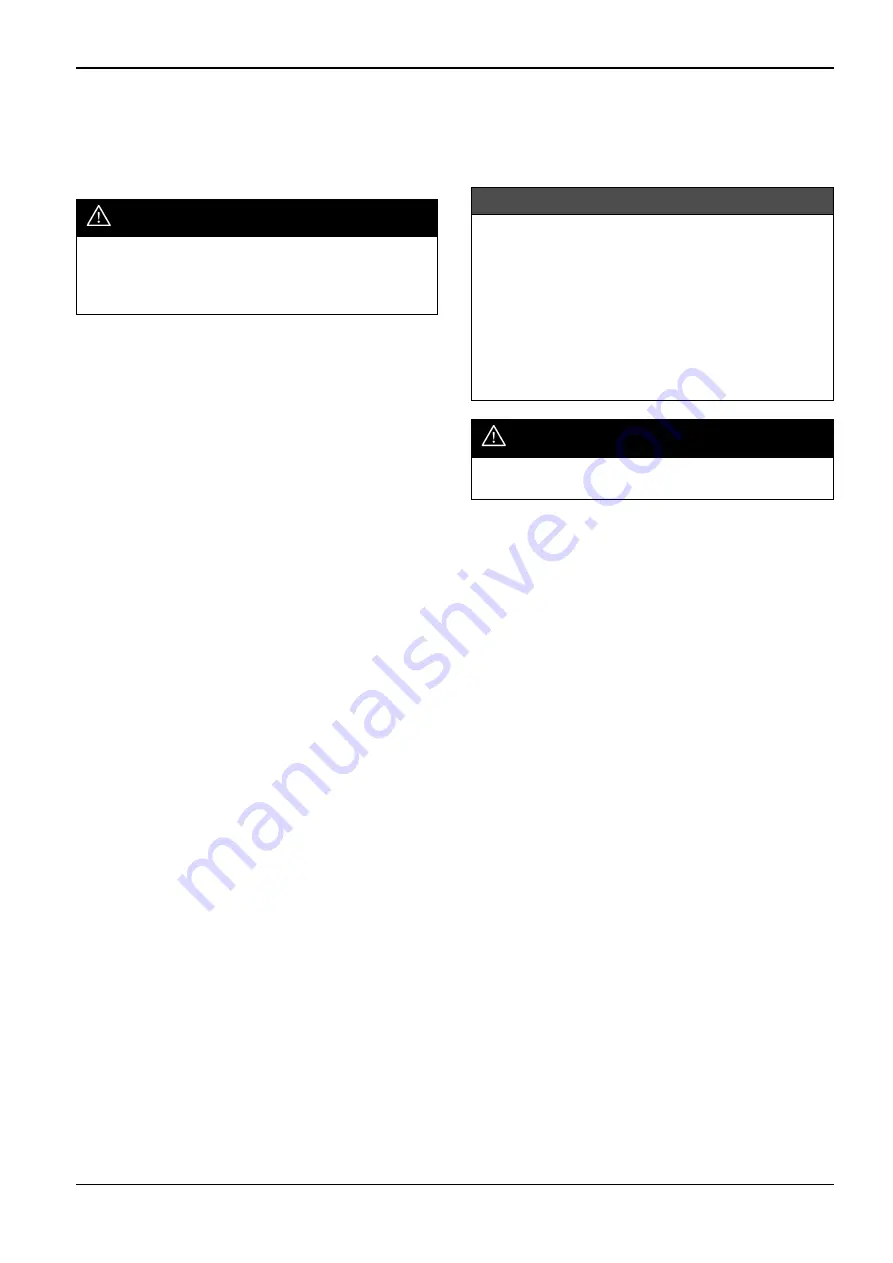
Maintenance
23201387 (03/05)
23
Lightsource LT6K
Operation and Maintenance Manual
Engine Radiator
Check the coolant level in the radiator. The coolant
must cover the tubes in the top tank (approximately 1
inch high on a clean measuring rod, stuck down filler
neck).
The engine coolant system is normally filled with a 50/
50 mixture of water and ethylene glycol. This
permanent type anti-freeze contains rust inhibitors and
provides protection to -35°F (-37°C). The use of such a
mixture is recommended for both summer and winter
operation.
It is recommended to test the freezing protection of the
coolant every six months or prior to freezing
temperatures. Replenish with a fresh mixture every
twelve months.
Each month, inspect the radiator exterior for
obstructions, dirt and debris. If present, blow water or
compressed air containing a non-flammable solvent
between the fins in a direction opposite the normal air
flow. Should the radiator be clogged internally, reverse
flushing, using a commercial product and the supplier’s
recommended procedure, may correct the problem.
Engine Protection Shutdown System
The operation of the engine protection shutdown
system should be checked every month, or whenever it
appears not to be operating properly. The three
switches involved in this protective shutdown system
are the engine coolant high temperature switch, the
engine oil pressure switch and the low fuel switch.
(optional)
The engine oil pressure switch prevents the engine
from operating with low oil pressure. Once a month,
remove a wire from the engine oil pressure switch to
check the shutdown system for proper operation.
Test the engine oil pressure switch by removing it and
connecting it to a source of controlled pressure while
monitoring an ohmmeter connected to the switch
terminals.
As pressure is applied slowly from the controlled
source, the switch should close at 12 psi (84 kPa) and
show continuity through the contacts. As the pressure
is slowly decreased to 10 psi (70 kPa) the contacts
should open and the ohmmeter should show a lack of
continuity through the contacts. Replace a defective
switch before continuing to operate the unit.
Once a year, the temperature actuated switch should
be tested by removing it from the unit and placing it in a
bath of heated oil. The engine coolant high temperature
switch will require a temperature of approximately
220°F (104°C) to actuate.
Control Compartment
Every six months or 500 hours with the unit “OFF”,
perform visual inspection for loose connections, dirt,
arcing, damage to electrical components.
Fuel Tank
In order to minimize condensation inside the fuel tank,
refill as soon as possible after every use or at the end
of each work day. Use only clean, DIESEL fuel. When
using a funnel, ensure that it is clean and free from
dust. Every six month, drain any sediment or
accumulated condensate.
Battery
Keep the battery posts and cable connections clean
and lightly coated with a grease.
Fasteners
Monthly spot check several capscrews and nuts for
proper torque. If any are found loose, a more thorough
inspection must be made and deficiencies corrected.
Running Gear/Wheels
Check the wheel nut torque 20 miles (30 kilometres)
after refitting the wheels.
Lifting jacks should only be used under the axle.
The bolts securing the running gear to the chassis
should be checked periodically for tightness (refer to
the “Preventative maintenance schedule” on page 20
for frequency) and re-tightened where necessary.
WARNING
Remove cap slowly to relieve Pressure from HOT
radiator. Protect skin and eyes. Hot water or
steam and chemical additives can cause serious
personal injury.
IMPORTANT
The engine temperature switch does NOT offer
protection when NO coolant is present. Test the
switch operation by connecting an ohmmeter
between the two wire terminals. The ohmmeter
should show zero ohms. When the switch is
placed in the heated oil bath and its contact open,
the ohmmeter should indicate infinite ohms. Tap
the switch lightly during the checking operation.
Replace any defective switch before continuing
to operate the unit.
WARNING
Never operate the unit with a defective safety
shutdown switch or by by-passing a switch.
Summary of Contents for LT6K
Page 3: ...22545495 03 05 3 Lightsource LT6K Operation and Maintenance Manual...
Page 13: ...Safety Lightsource LT6K 12 23201387 03 05 Operation and Maintenance Manual...
Page 19: ...Operating Instructions Lightsource LT6K 18 23201387 03 05 Operation and Maintenance Manua...
Page 29: ...Maintenance Lightsource LT6K 28 23201387 03 05 Operation and Maintenance Manual...