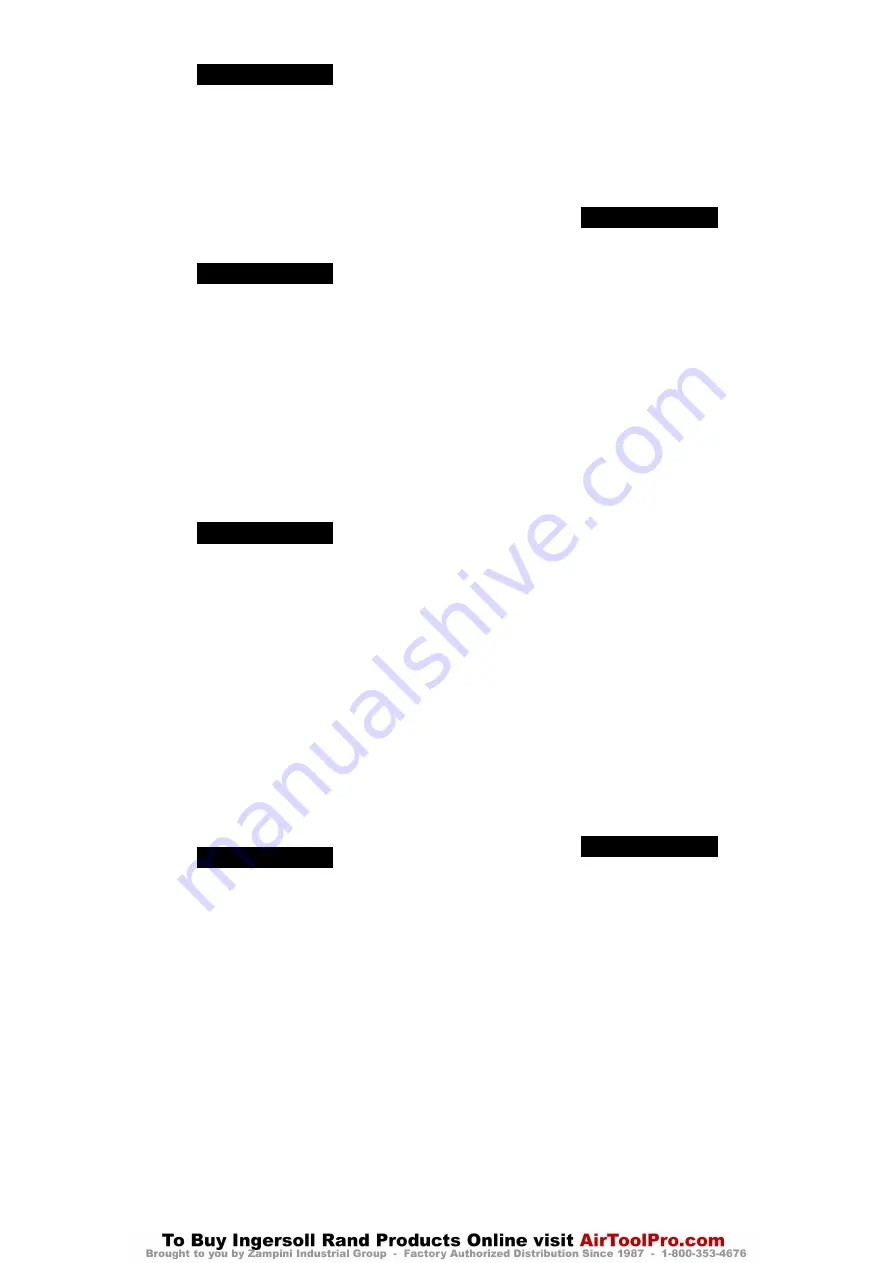
NOTICE
•
Do not rotate reverse valve past a 90 degree position; it may result in ball
(916) falling into motor.
5. Slowly push reverse valve, while still in the 45 degree position, the rest of the
way in housing until flush with surface. From other side of valve, rotate reverse
valve back to neutral position. Ball should be seated in ball slot at that time.
6. Lubricate ‘O’ ring (942) and place into groove in exhaust flange (955).
7. Secure exhaust flange (955) to valve housing (917) with capscrews (901) and
washers (902).
8. Insert ‘O’ ring (941) into seal bracket (939). Lubricate ‘O’ ring (942) and place in
groove in seal bracket.
9. Place seal bracket over end of reverse valve. Using finger pressure, press until
seal is seated on reverse valve and seal bracket is seated on valve housing. Secure
with washers (924), capscrews (925) and buttonhead screws (938).
Pilot Valve Assembly:
NOTICE
•
For easier installation, it is recommended to use Ingersoll Rand pilot valve
tool (920). This must be purchased separately.
1. Install pilot valve assembly (910).
2. Apply thread sealant Loctite® 567 to pilot valve assembly (910) and place pilot
valve assembly into valve housing (917). Use a large flat-tipped screwdriver to
engage slots in pilot seat to tighten until pilot assembly is 1/8 inch (3.175 mm)
from housing bore.
3. Insert plug (912) and tighten.
Piston Assembly:
1. Lubricate and install ‘O’ rings (921) and (923) on piston (922).
2. Insert assembled piston into valve housing (917) from handle side.
3. Secure gasket (918), piston cover (919) and washers (902) with capscrews (901).
4. Place poppet seal (907) into poppet cap (906). Place this assembly into valve
housing and seat on piston (922).
5. Place spring (905) over this assembly.
6. Secure with gasket (904), poppet cover (903), washers (902) and capscrews (901).
Handle Assembly:
1. Place spring (937) over reverse valve handle end in seal bracket (939).
NOTICE
•
Spring (937) will have to be 'cocked' over stud in bracket. This will ensure
handle returns to neutral.
2. Install handle assembly (930) over reverse valve end. Handle will have to be lifted
slightly to allow pin to fit into slot in seal bracket (939).
3. Secure handle assembly (930) to reverse valve with tab lockwasher (909) and
capscrew (901). Refer to “TORQUE CHART” on page 16 for torque requirements.
Washer (909) has small tab on side; engage with small hole in handle.
4. Bend tabs of washer (909) over flats of capscrew.
5. Press plug (935) into handle assembly to cover capscrew. Check control handle
movement. Correct any discrepancies.
n
Emergency Stop and Overload Control Valve Assembly
Refer to Dwg. MHP2697.
Reverse Valve Assembly:
1. Insert reverse valve (943) into bushing (944) with ball slot oriented UP,
approximately 2-1/2 inches (64 mm).
2. Insert bushing (944) and reverse valve (943) into valve housing (917) from
exhaust flange side, ensuring that groove in bushing is aligned with dowel pin
(945).
3. Apply grease to ball (916) and insert into reverse valve platform. With finger,
push ball (916) in housing until ball hits end of reverse valve.
4. Holding ball (916) in position on reverse valve platform, rotate reverse valve from
neutral position to approximately 45 degrees in either direction. Ball will ‘walk’
up side of reverse valve platform and move in ball hole in bushing (944).
NOTICE
•
Do not rotate reverse valve past a 90 degree position; it may result in ball
(916) falling into motor.
5. Slowly push reverse valve, while still in the 45 degree position, the rest of the
way in housing until flush with surface. From other side of valve, rotate reverse
valve back to neutral position. Ball should be seated in ball slot at that time.
6. Lubricate ‘O’ rings (942) and (722), and place in grooves in exhaust adapter (723).
7. Lubricate ‘O’ ring (942) and place in groove in exhaust flange (955).
8. Secure exhaust adapter (723) with exhaust flange (955) to valve housing (917)
with capscrews (721) and washers (902).
9. Insert ‘O’ ring (941) into seal bracket (939). Lubricate ‘O’ ring (942) and place into
groove in seal bracket.
10. Place seal bracket over end of reverse valve. Using finger pressure, press until
seal is seated on reverse valve and seal bracket is seated on valve housing. Secure
with washers (924), capscrews (925) and buttonhead screws (938).
Pilot Valve Assembly:
Follow assembly instructions in ‘Control Valve Assembly’ on page 10.
Piston Assembly:
Follow assembly instructions in ‘Control Valve Assembly’ on page 10.
Handle Assembly:
Follow assembly instructions in ‘Control Valve Assembly’ on page 10.
Emergency Stop Assembly:
1. Insert spring (711) into valve housing (917).
2. Place ‘O’ rings (703) on plunger (707).
3. Insert plunger into valve housing.
4. Screw adapter (706) and E-Stop button (705) into valve housing.
5. Tighten adapter until snug; do not over tighten.
Overload Valve Assembly:
1. Replace ‘O’ rings (703) on plunger (702).
2. Insert plunger (702) with ‘O’ rings in valve housing (917).
3. Replace grommet (701) in cap (700).
4. Install and tighten cap (700) flush to valve housing.
5. Replace piston (712) if it appears damaged or worn.
6. Insert ‘O’ ring (713) on piston (712).
7. Replace gasket (714).
NOTICE
•
Cover (719) retains spring (718), adjustment nut (717) and plate (715).
Insert capscrews (901) and washers (902) in a crisscross pattern until
tightened evenly.
8. Insert adjusting screw (720). Refer to “OPERATION” section ‘Overload Device’ in
Product Information Manual for adjustment.
9. Secure control valve assembly to intake manifold using capscrews (951) and
washers (949). Use new gaskets (946) between control valve and manifold.
10. Test control valve for proper operation. Lift slide handle and move handle all the
way in one direction and release hand. Control handle should return and lock in
the neutral position. Repeat for other direction.
11. Connect brake line.
12. Connect air supply line.
n
Motor Assembly
Refer to Dwg. MHP1007.
Crankshaft Assembly:
1. If removed, press crank bearing (228) on crank shaft assembly (231). Press only
on inner race of bearing.
2. Place crank assembly (231) on a work bench with oil slinger (230) down and slide
sleeve (232) (with tang up) on crankpin.
3. Slide bushing (233) over sleeve (232) and first connecting rod ring (234) with
chamfer up.
4. Install connecting rods (206) in same order as removed, with all feet pointing in
same direction, using first connecting rod ring (234) to hold one side of
connecting rod feet.
5. Slide second connecting rod ring (234) over other side of connecting rod feet
with chamfer on ring facing down (toward stem of connecting rod).
6. Slide crank shaft (231) (valve end) over crankpin while simultaneously aligning
tang on sleeve (232) with slot in crank shaft.
7. Rotate and position crank shaft (valve end) relative to crankpin to allow
installation of lock pin (235).
8. Tap lock pin (235) in place and install pin nut (237). Refer to “TORQUE CHART”
on page 16 for torque requirements.
9. Install cotter pin (236).
10. Install roll pin (240) and bearing (228) into valve end of crank shaft.
11. Check that all connecting rods move freely around crank.
Motor Body Assembly:
1. Position crank assembly (231) in motor housing (217) with bearing (228) seated
and connecting rods (206) centered in cylinder holes.
2. Assemble throttle valve assembly (500), gaskets (546) and exhaust flange (254)
to rotary valve housing (247) using four capscrews (551) and lockwashers (549).
3. Install bearing (252) on rotary valve (250) by pressing only on inner race of
bearing. With exhaust flange (254) down, install rotary valve (250) into rotary
valve housing (247). Slide rotary valve out of rotary valve housing far enough to
install seal ring (251) on crank shaft end of rotary valve (250). Slide rotary valve
back into rotary valve housing (247).
4. Install ‘O’ ring (244) into motor housing (217).
5. Install rotary valve housing gasket (243) onto rotary valve housing (247). With
exhaust flange down on bench, install motor housing (217) on to rotary valve
housing (247). Check for any evidence of damage to ‘O’ ring (244) when rotary
valve housing is fully engaged. Install capscrews (253). Refer to “TORQUE CHART”
on page 16 for torque requirements.
NOTICE
•
Make certain that roll pin (240) and three lugs on rotary valve (250) line up
with corresponding hole and lugs on crank shaft.
•
Do not allow rotary valve (250) to slide back in rotary valve housing (247).
If rotary valve slides in too far, seal ring (251) will lock up in internal grooves
of rotary valve housing (247) and restrict further assembly.
6. Rotate crank assembly to position one connecting rod (206) at the top of its
stroke. Install a piston (204) with its rings (202) and (207) to connecting rod (206)
with wrist pin (203) and retainer rings (205). Refer to Dwg. MHP0224
on page 12 for oil and compression ring installation. A. Piston Head; B.
Compression Ring Groove; C. Ends of compression rings must be staggered to
avoid alignment with wrist pin opening and ends of oil ring; D. Colored ends of
oil ring must butt together and must not overlap; E. Install one compression ring
on either side of oil ring; F. Wrist pin opening.
7. Install a new cylinder head gasket (209) before installing cylinder (201).
8. Install cylinder (201) over piston (204) by compressing both piston rings (202)
and (207). Secure cylinder head to motor housing (217) with four capscrews
(200). Refer to “TORQUE CHART” on page 16 for torque requirements.
9. Repeat Steps 6 through 9 with remaining cylinders.
10. Rotate motor by hand. Motor should rotate without binding.
11. Press bearing (228) into motor side of mounting flange (216).
12. Install mounting flange (216) and gasket (226) on large base side of motor
housing (217). Make sure notches on both parts are aligned. Temporarily secure
parts with one capscrew (4), lockwasher (3) and a 1/2-NC nut.
13. Lightly lubricate ‘O’ ring (5) and install in groove on motor adapter (6).
Form MHD56401 Edition 3
11