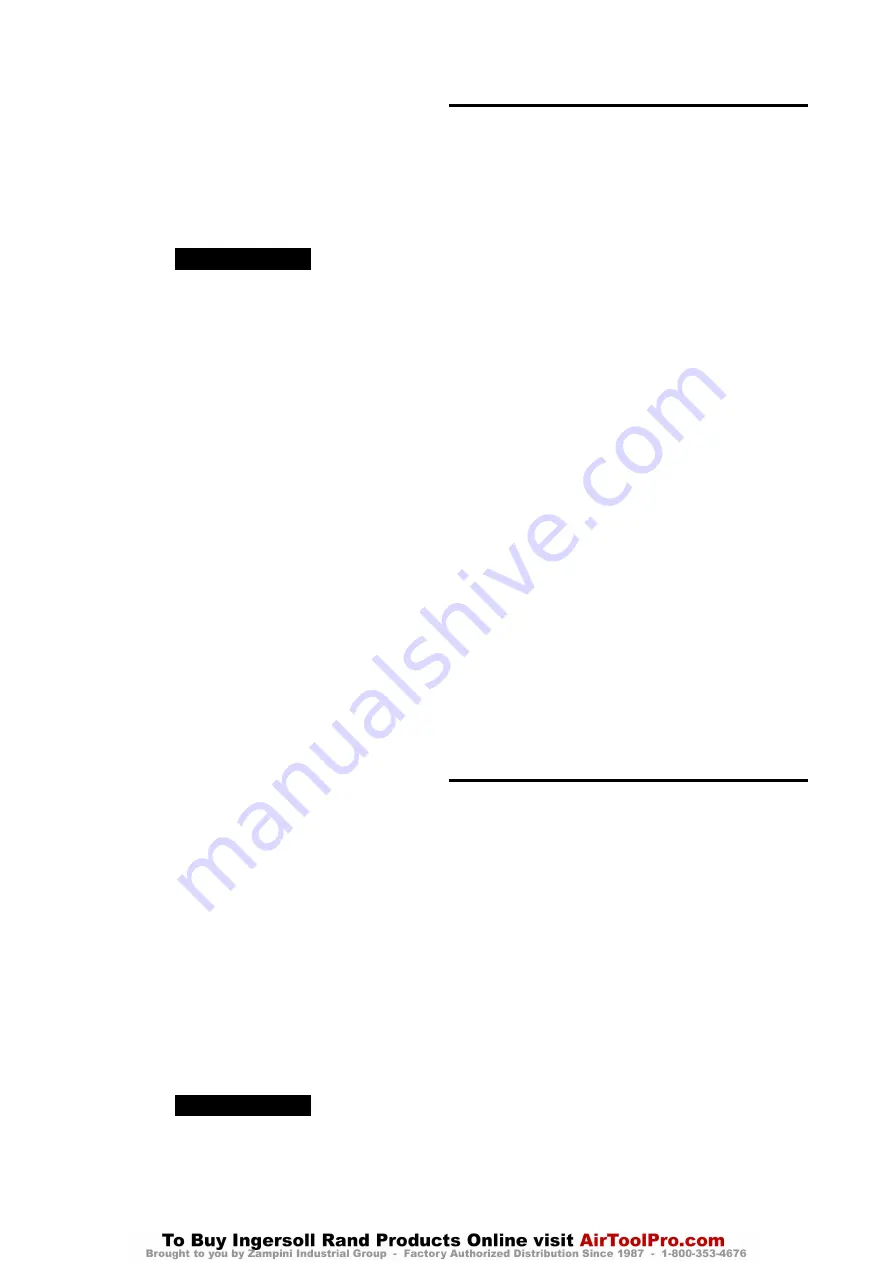
1. Place reduction gear assembly on a clean work bench. Have a couple of wooden
blocks available to prevent assembly from rolling around. There will also be a
small amount of oil remaining in housing so have some absorbent material
readily available.
2. Using a hammer and punch, drive spring pins (404) in, until they are completely
in input housing (424).
3. Remove capscrews (401) and, using a plastic mallet, tap seal support (400) until
loose and remove.
4. Remove oil seal (402) and ‘O’ ring (403).
5. Remove capscrews (425).
6. Using a plastic mallet, tap support (405) and ring gear (409) to separate.
7. Remove ‘O’ ring (408) and bearing (407).
8. Pull out planetary support (410) assembly.
9. From planet gear side reach into planetary support hub and remove retainer
ring (420). Spacer (422) may be on shaft (445) or still in spacer (418). Remove at
this time.
10. Push spacer (418) out of planetary support and remove ‘O’ ring (419).
NOTICE
•
Do not disassemble planetary gears from their housings unless required to
replace damaged parts. Disassembly directions 11 and 12 apply only to
planetary gears (415) housed in planetary support (410). For information
on other planetary assemblies (430 and 440) contact your Ingersoll Rand
distributor or the factory.
11. Place planetary support (410) in a container. Holding the planet gear (415) with
one hand, slowly push planet gear shaft (417) out of support. Carefully remove
planet gear. When thrust bearings (413) become free squeeze together with
fingers. Once spring pins (412) are free they may fly out or roller bearings (414)
might start to fall out. Remove planet gear assembly and carefully place in
container.
12. Slide thrust bearings (413) off ends of planet gear (415) and push out all roller
bearings (414) into container.
13. Separate ring gear (409) from input housing (424) and remove ‘O’ ring (408).
14. Remove spacer (423).
15. Remove capscrews (439).
16. Separate input housing (424) from ring gear (436) and remove ‘O’ ring (434).
17. Remove retainer ring (427) from input housing (424) and pull out cylinder roller
bearing (426).
18. Remove sun gear (429) and spacer (428). Separate the two.
19. Remove planetary assembly (430).
20. Remove sun gear (433) and spacer (422). Separate the two.
21. Remove retainer ring (435) from sun gear (433).
22. Tap out spring pins (437). Separate ring gear (436) from input housing (438) and
remove ‘O’ ring (434).
23. Tap out spring pins (443). Remove capscrews (448) and separate input housing
(438) from ring gear (444) and end cover (446).
24. Remove planetary assembly (440) and ‘O’ ring (442).
25. Remove ‘O’ ring (442) and shaft (445).
26. Remove capscrews (452) and separate front cover (450). Remove thrust plate
(449) and gasket (447).
27. Remove adjusting screw (453).
n
Press Roller Disassembly (optional feature)
Refer to Dwg. MHP2945.
1. Compress the ends of springs (405) and (406) to disengage from siderail (98) and
pins (413) on press roller arm (407).
2. Loosen collars (404).
3. Remove capscrews (408) and washers (409) from both ends of shaft (403), and
carefully slide shaft (403) through hole in upright (42). Press roller assembly (400)
will fall away from shaft (403).
4. It is not necessary to remove bushings (410) unless replacing.
5. Remove springs (405) and (406) from press roller arm (407).
6. Remove capscrews (408), washers (409) and rollers (401) from shaft (411).
7. Remove shaft (411) and center roller (402) from press roller arm (407).
n
Drum Locking Pin Disassembly (optional feature)
Refer to Dwg. MHP2675.
1. Remove capscrews (305) and washers (306) to separate drum locking pin
assembly from winch upright (184).
2. Unscrew drum lock pin (312) from shaft (304). Separate spring (310), drum lock
pin (312) and housing (308) from assembly.
3. Remove nut (303) and capscrew (302) to separate handle (301) from shaft (304).
4. Remove bushing (311) from winch upright (84) only if replacement is required.
n
Two Function Pendant Disassembly (optional feature)
Refer to Dwg. MHP1677 or MHP2346.
1. Remove fittings (348) and lifting eye (440).
2. Unscrew plugs (444). Remove springs (445) and balls (446).
3. Tap out pin (447) and remove levers (453).
4. Remove setscrew (455) from pendant handle (454).
5. Remove valve assemblies (452). Remove ‘O’ rings (443) and (449) and protectors
(451). Discard ‘O’ rings.
6. Remove plug (470) or emergency stop valve (441) from pendant handle.
7. Remove retainer ring (458) and exhaust washer (457).
n
Limit Switch Disassembly (optional feature)
Refer to Dwg. MHP2677.
NOTICE
•
It is not recommended to disassemble limit switch. Contact factory if repair
is required.
1. Remove and tag hose connection if not already done.
2. Remove capscrews (97) and washers (96) that secure limit switch assembly to
upright (84).
3. Store limit switch assembly in a clean, dry area until winch reassembly.
n
Cleaning, Inspection and Repair
n
Cleaning
Clean all product component parts in solvent (except brake bands and disc brake
friction plates). The use of a stiff bristle brush will facilitate removal of accumulated
dirt and sediments in the reduction assembly, on housings, frame and drum. Dry
each part using low pressure, filtered compressed air. Clean brake band using a wire
brush or emery cloth. Do not wash brake band in solvent. If brake band lining is oil
soaked, it must be replaced.
n
Inspection
All disassembled parts should be inspected to determine their fitness for continued
use. Pay particular attention to the following:
1. Inspect all gears for worn, cracked, or broken teeth.
2. Inspect all bushings for wear, scoring, or galling.
3. Inspect shafts for ridges caused by wear. If ridges caused by wear are apparent
on shafts, replace shaft. Inspect all surfaces on which oil seal lips seat.
4. Inspect all bearings for play, distorted races, pitting and roller or ball wear or
damage. Inspect bearings for freedom of rotation.
5. Inspect all threaded items and replace those having damaged threads.
6. Inspect band brake lining for oil, grease and glazing. If band brake lining is oil-
soaked replace brake bands as a set. Remove glazed areas of band brake lining
by sanding lightly with a fine grit emery cloth.
7. Measure thickness of band brake lining. If brake band linings are less than 0.062
inch (2 mm) thick anywhere along edges replace brake bands as a set.
8. Inspect cylinder bores. Minor scratches in bore lining may be repaired by lightly
honing to remove. Refer to tolerances listed below for acceptable clearances.
Replace liner if deep scratches or gouges are apparent. Measure inside diameter
of liner. If measurement is greater than 4.764 inches (121 mm) replace liner. ‘Ring
Gap’ may also be used to determine wear; place compression ring into liner,
using a piston, push ring until approximately half way in liner and measure ‘Gap’
— 0.003 inch (0.076 mm) is normal; replace rings, or liner, if ‘Gap’ exceeds 0.020
inch (0.51 mm).
9. Inspect the drive plates for warpage or other damage, and replace damaged
parts as necessary. Replace the input pinion shaft oil seal.
10. Measure the thickness of the brake friction disc. The brake friction disc must
show an even wear pattern. If the brake friction disc is 0.076 inch (1.93 mm) or
less, replace the disc.
n
Repair
Actual repairs are limited to removal of small burrs and other minor surface
imperfections from gears and shafts. Use a fine stone or emery cloth for this work.
Do not use steel wool.
1. Worn or damaged parts must be replaced. Refer to the applicable parts list in
the Product Parts Information Manual for specific replacement parts
information.
2. Inspect all remaining parts for evidence of damage. Replace or repair any part
which is in questionable condition. Cost of the part is often minor in comparison
with cost of redoing job.
3. Smooth out all nicks, burrs, or galled spots on shafts, bores, pins, or bushings.
4. Examine all gear teeth carefully, and remove nicks or burrs.
5. Polish edges of all shaft shoulders to remove small nicks which may have been
caused during handling.
6. Remove all nicks and burrs caused by lockwashers.
7. Replace all gaskets, oil seals, and ‘O’ rings removed during product disassembly.
n
Assembly
n
General Instructions
•
Use all new gaskets and seals.
•
Replace worn parts.
•
Assemble parts using matchmarks attached during disassembly. Compare
replacement parts with originals to identify installation alignments.
•
Lubricate all internal parts with rust and oxidation inhibiting lubricant, ISO
VG 100 (SAE 30W).
•
Apply a light coat of Loctite® 243 to all threaded components prior to
assembly, unless otherwise specified.
n
Control Valve Assembly
Refer to Dwg. MHP2696.
Reverse Valve Assembly:
1. Insert reverse valve (943) into bushing (944) with ball slot oriented UP,
approximately 2-1/2 inches (64 mm).
2. Insert bushing (944) and reverse valve (943) into valve housing (917) from
exhaust flange side, ensuring that groove in bushing is aligned with dowel pin
(945).
3. Apply grease to ball (916) and insert into reverse valve platform. With finger,
push ball (916) in housing until ball hits end of reverse valve.
4. Holding ball (916) in position on reverse valve platform, rotate reverse valve from
neutral position to approximately 45 degrees in either direction. Ball will ‘walk’
up side of reverse valve platform and move in ball hole in bushing (944).
10
Form MHD56401 Edition 3