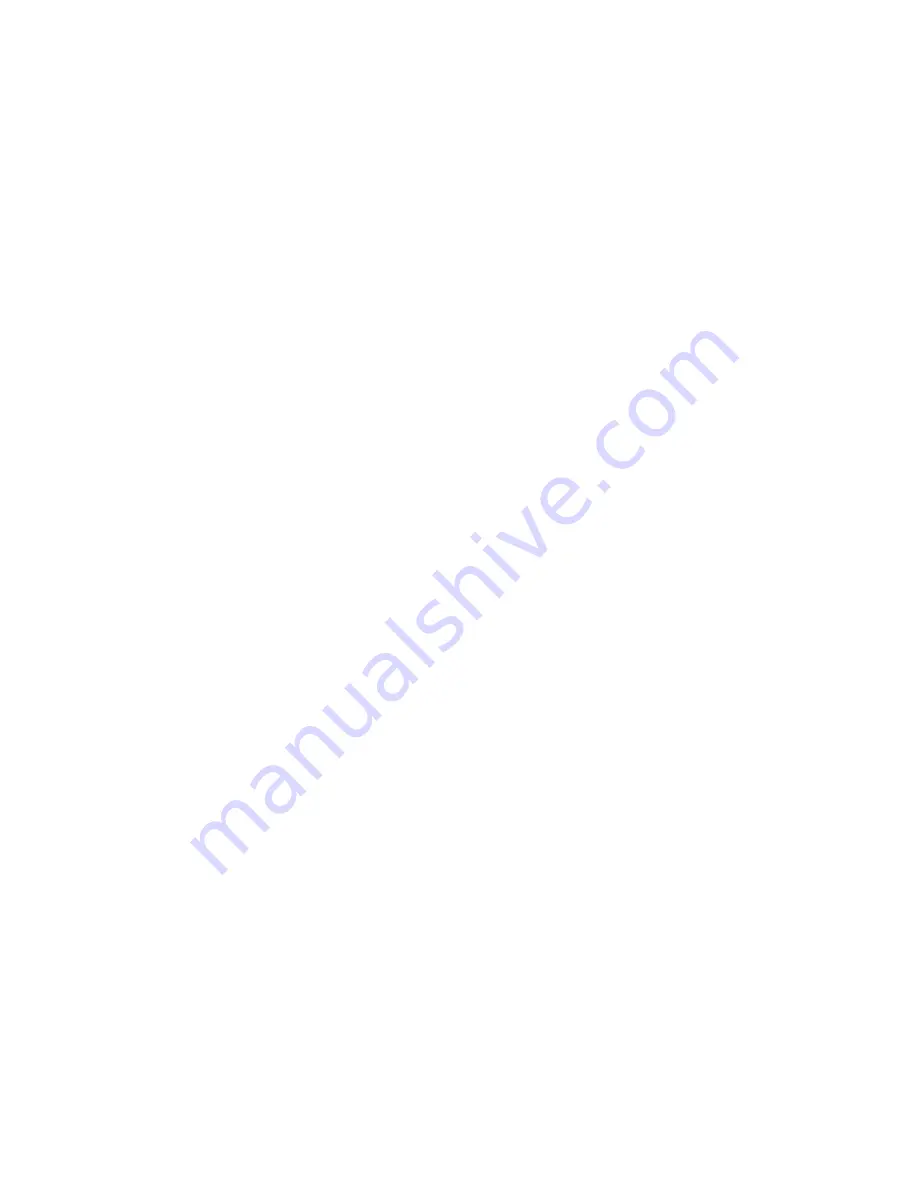
4) Appearance, external cracks, discoloration, leakage. When the measured capacitance of the
capacitor has reduced below 85% of the rating, change the capacitor.
(3) Relays
To prevent a contact fault, etc., relays must be changed according to the number of accumulative switching
times (switching life is approximately 30,000 rides).
5-4 Extended Periods of Non-Use (6 Months or more)
If the unit is to be stored or left inoperable for periods in excess of six months be aware of the effects the
environment on the equipment. Such things as temperature, humidity, sunlight, oils, solvents, corrosive
liquids/gases and insects can affect the systems.
5-5 Harsh Environment Conditions
If conditions exist in which humidity, dust, corrosive materials or any other type of particles that would
collect onto or corrode exposed materials in a fashion thereof, then the scheduled maintenance will be
required twice as frequent as specified in the current time intervals. A determination of the environment
whether it be inside a humid facility or near an exposed opening that moisture can enter or near a dust or
dirt-collecting area should be examined. Keeping the system properly lubricated and cleaned will aid in the
longevity of the system.
During the course of operations some problems may develop. This chapter has been designated to assist in
the locating and repair of any problem that affects the operation or safety of your simulator. At all times
basic troubleshooting procedures will be the most effective method to use. When working on the electrical
system always check the proper power is present. Make sure the Electrical Control Box is unplugged and
all the inverters are discharged before working on any electrical components inside the panel. This chapter
has been broken into the following two sections: Electrical, and Computer.
5-6
Cleaning of Cockpit and Consoles
Cockpit fiberglass can be cleaned using A good glass cleaner for heavy smudges, followed up with a
furniture polish like “PLEDGE” or a wax made specifically for fiberglass. The consoles and the rest of
the cabinetry surfaces can be cleaned using a furniture polish like pledge spray. Always wipe off
residue and polish.
NEVER
wipe the fiberglass area with a dry cloth, fine scratches will dull the
finish.
5-7 TROUBLESHOOTING
Whenever a fault occurs during the operation of this simulator and before you start
troubleshooting, ask yourself some questions. When did the problem occur, what was the
machine/operator doing prior to the event or what maintenance action was taken prior to the event.
Where is the problem? Use the simplistic approach and don’t go for the major parts. Read the
information and use the diagrams provided for you in this manual. If all else fails, call Maxflight
Tech Support for help, Phone 1-732-942-9898 Ext. 300 during the evening or 256 during the day.
Day time is 0800 to 1730 Eastern Daylight Time. Rest of the day is on a Beeper response system.
5-7A Power Problems
Is the unit plugged into a live circuit?
Electrical Requirements:
Three phase 208/440/450 VAC for drive motors and inverters.
Single phase 110/220 VAC for the command console, kiosk and cockpit requirements.
Ensure power is available by checking circuit breakers. Measure power in the electrical panel on the
magnetic contactor input terminals. Measure across any two lugs and you should read 208/440/450 VAC
depending where you are in the world. If you do not get a reading of such across all then you lost a phase
to the machine. Check breakers, input power at the end of the extension or wall receptacle. If the power
reading is OK, then check and see if the BLUE reset on the contactor has tripped , if so reset and try
again. On the Inverters if power is applied by pulling out the E-STOP you must have a small power ON
light at top left side of each inverter. If the computer is up and running you should also have another light
on to the right middle of the inverter, this signals that communications between inverter and CPU are OK.
Summary of Contents for MaxFlight MT3000B ELECTRIC
Page 1: ...MaxFlight MT3000 B ELECTRIC Monster Truck Manual...
Page 8: ...MaxFlight MT3000 B ELECTRIC Operators Manual...
Page 26: ...MaxFlight MT3000 B ELECTRIC Technical Manual...
Page 58: ...Address EDS...
Page 59: ...Path IO Drivers Game log and alert log routing information within the CPU...
Page 60: ...Video Sound This is the page that the Occupant Safety Stop can be tested...
Page 64: ...Regedit 32 Window Hkey Local Machine Window Start Run select Regedit32 enter...
Page 65: ...Lift Motion Editor Settings Counterweight Motion Editor...
Page 66: ...Counterweight Motion Cont Pitch Motion Editor...
Page 67: ...Pitch Motion Filter 1 Editor Pitch Motion Filter 2 Editor...
Page 68: ...Pitch Motion Filter 3 Editor Roll Axes Motion Editor Roll Motion Filter 1 Editor...
Page 69: ...Roll Motion Filter 2 Editor Roll Motion Filter 3 Editor...
Page 84: ......
Page 93: ...MaxFlight MT3000 Installation Manual...
Page 99: ......
Page 100: ......
Page 101: ......
Page 102: ......
Page 103: ......
Page 104: ......
Page 105: ......
Page 106: ......
Page 107: ......
Page 108: ......
Page 109: ......
Page 110: ......
Page 111: ......
Page 112: ......
Page 113: ......
Page 114: ......
Page 115: ......
Page 120: ...Section IV Drawings A Electrical...
Page 121: ...B Mechanical...