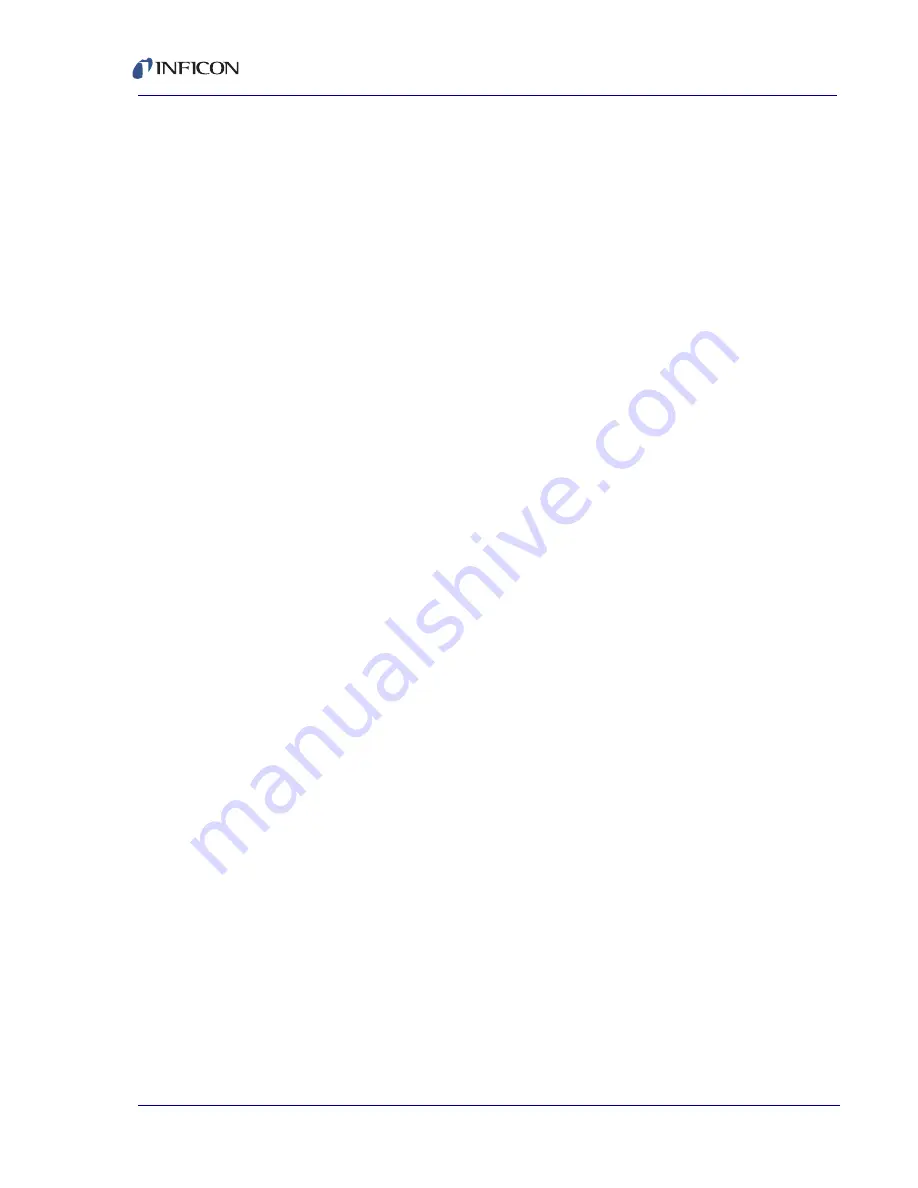
4 - 9
XTC/3 Operating Manual
Tooling is a correction factor used for correlating the rate and thickness
accumulation on the crystal with the thickness accumulation on the substrate.
This thickness difference is due to the geometric distribution of material flux from
the source.
The tooling factor is calculated using the equation:
[1]
where TF
i
= Initial Tooling Factor, T
m
= Actual Thickness at the Substrate, and
T
x
= Thickness on the Crystal.
If the
TOOLING
parameter is changed, the new
TOOLING
value is used for
subsequent calculation of the rate and thickness. Also, the thickness accumulated
thus far will be re-scaled based on the change to the
TOOLING
.
4.2.3.3.1 Setting S&Q Parameters (Soft Crystal Failures)
At some point during deposition the crystal may become unstable or erratic
yet continue to oscillate within XTC/3 acceptable frequency range of
6.0 MHz to 5.0 MHz. The resulting rate control will be poor and thickness
measurements may be inaccurate. By programming non-zero values for
Stability
and/or
Quality
, various improvements in process control can be achieved if one or
more backup crystals are available. XTC/3 can be made to automatically switch
to a different crystal and continue the deposition normally, or complete the run in
the
TIME-POWER
mode or even terminate the process if a backup crystal is
not available.
4.2.3.3.2 Stability
Under ideal conditions, the crystal’s frequency will only decrease during a
deposition due to the added mass of the material accumulating on the crystal.
Occasionally however, the crystal’s frequency may increase during a deposition
as a result of an undesired external influence.
Stability
selects the permissible
increase in frequency between successive measurements of the sensor before the
crystal is declared failed and an automatic crystal switch is initiated (if a backup
crystal or sensor is available) or the layer is completed in
TIME-POWER
mode
or ends in
STOP
.
There are many reasons for a crystal to exhibit an increase in frequency. For
example, when a crystal is near the end of its life, it is prone to instabilities that may
result in a temporary increase in crystal frequency. Also, an increase in frequency
may occur due to film stress relieving or a film tearing off a crystal. Additionally,
temperature effects may cause an increase in frequency. A crystal subjected to
temperatures over 100°C is more sensitive to small changes in temperature,
inducing frequency changes. When heat is applied inside a chamber and/or when
the shutter is opened (exposing the crystal to the hot source), the crystal frequency
will increase until thermal equilibrium is obtained. When the active process ends
Tooling
TF
i
T
m
T
x
-------
=