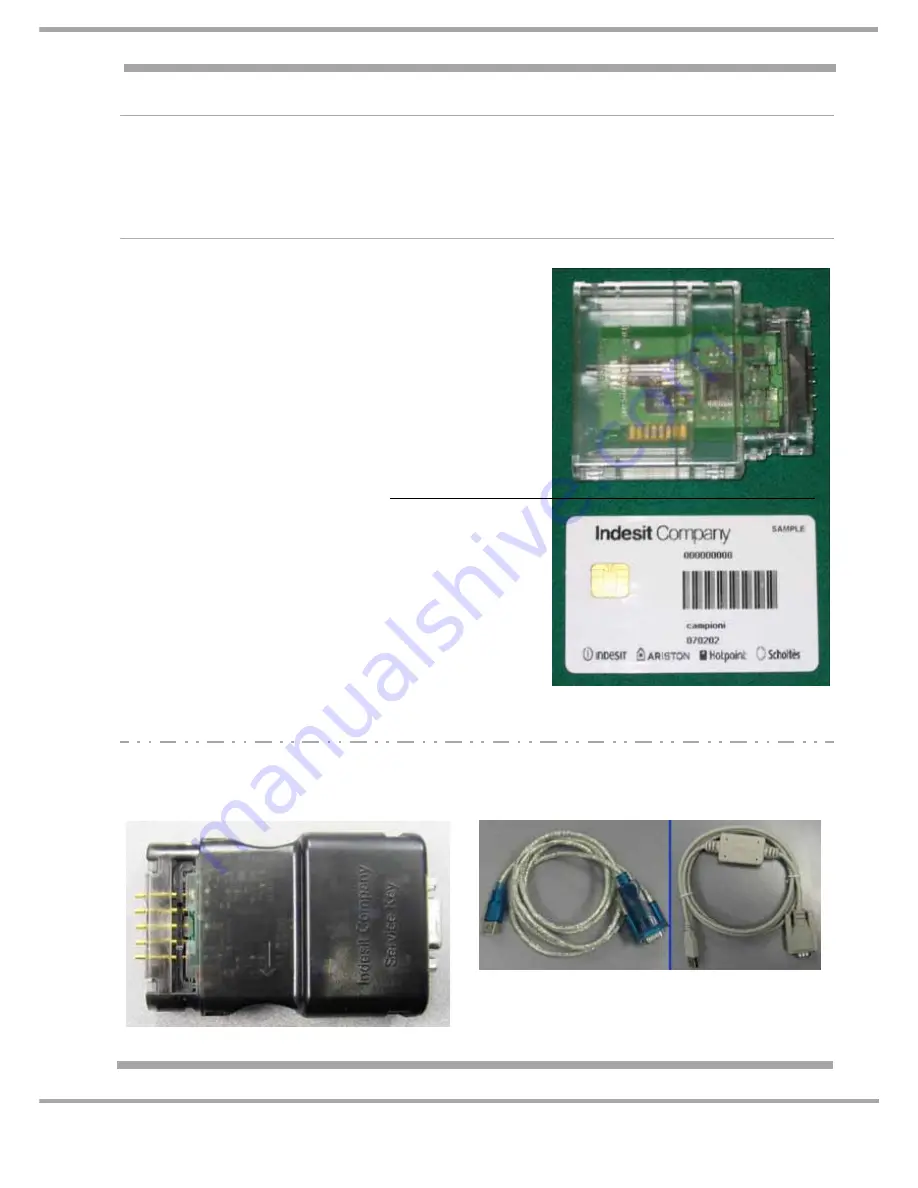
19 of 28
Indesit
Company
Service Manual UK
English
CONTROLS INFORMATION
A single control board located at the back of the machine contains all the circuitry to control the
machine and interfaces with the programme selector, option buttons and LEDs located on the
console panel. The control board has an access port to the rear of the machine.
MAIN BOARD PROGRAMMING - For Modules with fixed EEProm
PROGRAMMING (Using EMIT)
This machine can be programmed via the Emit, using a USB lead (Part number C00222800),
Hardware key (Part number C00115587) & the Memwriter software.
The module will always be supplied
without a programme when
supplied as a spare part.
NOTE:
This board does not have a
physically replaceable EEProm.
Programming a Main Board
There are a number of ways the
board can be programmed - some
of which are not applicable to
certain markets.
Types of programming:
1.
Handheld Terminal (Not UK)
2.
Emit / Memwriter (UK Indesit
Service Engineers)
3.
Smart Reader & Smart Card
(certain areas of UK market)
see photo.
Smart Card
Smart Card
this card holds the
program file and can
only be used ONCE.
Reader
Black Hardware Key
USB - Serial Cable
A Hardware Key Pin Repair Kit is
available which contains 5 replacement pins
(order Part No. C00114723).