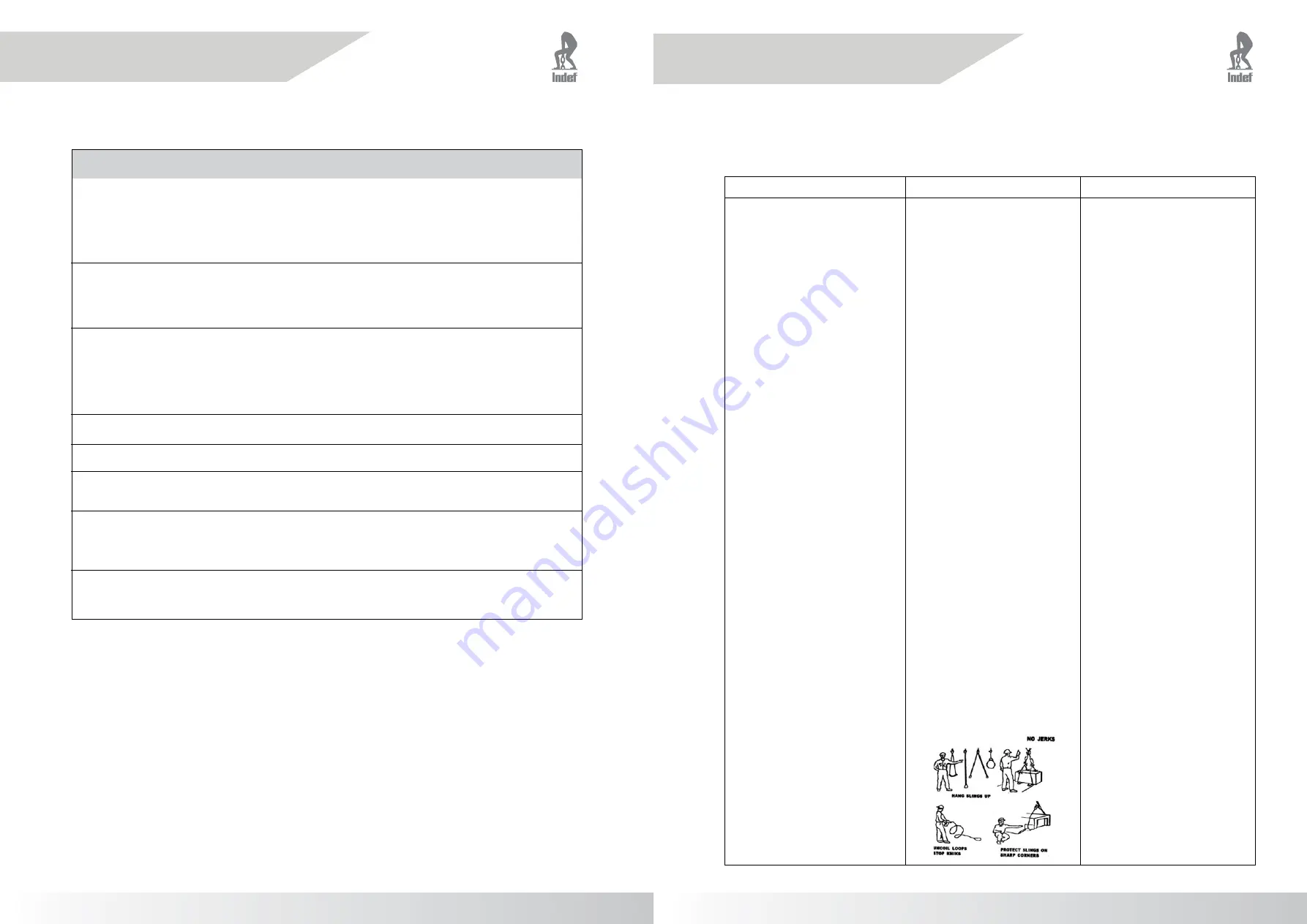
12
13
TROUBLE SHOOTING
TROUBLE
Hoist does not start
No contractor operates.
Hoist does not start
Contractors are working.
Operation interrupted
Chattering of contractors.
Push button gets stuck.
Braking time too long.
Brake & motor overheats
Causes of excessive load
chain waer.
Fast wear load chain
wheel.
CAUSE
Phase sequence wrong or
one phase failed or limit
switch operated.
Brake not opening or motor
defect or overloaded.
Loose connection or wire
broken, current collector
contact poor.
Push button sections shifted
Brake liner is worn.
Brake not properly opening
incorrect air-gap.
Lack of lubrication excessive
duty/load
Excessive worn out chain
HOW TO SET RIGHT
Change to phases of main supply.
Check with lamp.
Check movement of limit switch
levers.
Remove brake cover and see
movement of brake plate.
Check without load
Tighten all connections.
Check wires.
Check sitting of shoe & free
movement of arm
Tighten the housing screw.
Adjust brake as per Instructions.
Check brake air gap (see the
instructions).
Lubricate chain with harmony – 53
or equivalent oil. Check load & No
of start / stop per day.
Refer guide lines for chain.
SAFE OPERATING PROCEDURES FOR OVERHEAD CRANES / HOISTS
& SLINGS
DO Not
• Lift more than rated capacity
of Hoist.
• Operate Hoist with twisted,
kinked or damaged hoist-
rope
• Operate if rope is not seated
in drum or sheave grooves.
• Lift unless load slings are
centered on hook.
• Lift people or travel with
people on load.
• Make side pulls which
misalign rope with hoist.
• Operate unless all travel limit
devices are functioning.
• Lower below point where
less than two full wraps of
rope remain on hoist drum.
• Use upper limit switch to
stop hoist limit which is
emergency stop only.
• Leave operating position
with suspended load on
hook.
• Permit load to contact
obstacles.
• Exceed recommended duty
cycle.
• Use Hoist Rope or chain as
a sling or as an earthing for
welding.
• Divert his attention while
operating.
• Remove or obliterate
warning label
• Exceed fuse rating.
DO
• Test hoist & travel limit
devices at a start of each
shift.
• Position the Hoist so that
lifting appliance is directly
over the load.
• Take load gently & avoid
shock loads.
• Ensure the travel path is
clear before traveling.
• Sound warning single when
approaching personnel.
• Balancer the loading sling
before lifting more than few
inches.
• Test hoist brakes whenever
lifting load approaching
rated load capacity. Lift
load a few inches & test
hoist brakes before making
complete lift.
• Make visual checks on
equipment at reasonable
intervals & report the defects
immediately.
• Use controller to “stop” hoist
not limit switch.
• Watch for proper rigging on
load before lifting.
• Know standard hand signals.
• Check Lubricants.
• Check for proper phasing.
• Always anchor outdoor
hoists when not attended.
• Keep load block safely
overhead when not in use.
CAUTIONS
WHENEVER LEAVING OR
PARKING ANY HOIST OR CRANE
• Raise all hook to-but not
through-limit switches.
• Place all controls in off
position
• Place main power switch in
off position.
• Make visual check for
any dangerous condition
& report any defect
immediately.
• Report to supervisor when
Hoist is not in operation.
• Take up slacks, than start
load slowly.
• Keep chains free from twists,
knots & knits.
• Lift form Center of hooks.
Avoid lifting form points.
• Distribute load evenly on all legs.
• Inspect chain regularly.
Remember elongation of
links is a sign of overloading.
• A sharp edge can cut the lift
of your sling. Use blocking
padding or a corner saddle.
• Remove knots large enough
for the load.
• Don’t jerk loads- jerking may
double the stress in your
sling. Lift load gradually.
Hercules Hoists Limited ©2020
Note :- Due to continuous development and improvement specification listed above may be changed without notice
Hercules Hoists Limited ©2020
Note :- Due to continuous development and improvement specification listed above may be changed without notice
Indef CHAIN ELECTRIC HOIST
Hercules Hoists Limited ©2020
Note :- Due to continuous development and improvement specification listed above may be changed without notice
Indef CHAIN ELECTRIC HOIST