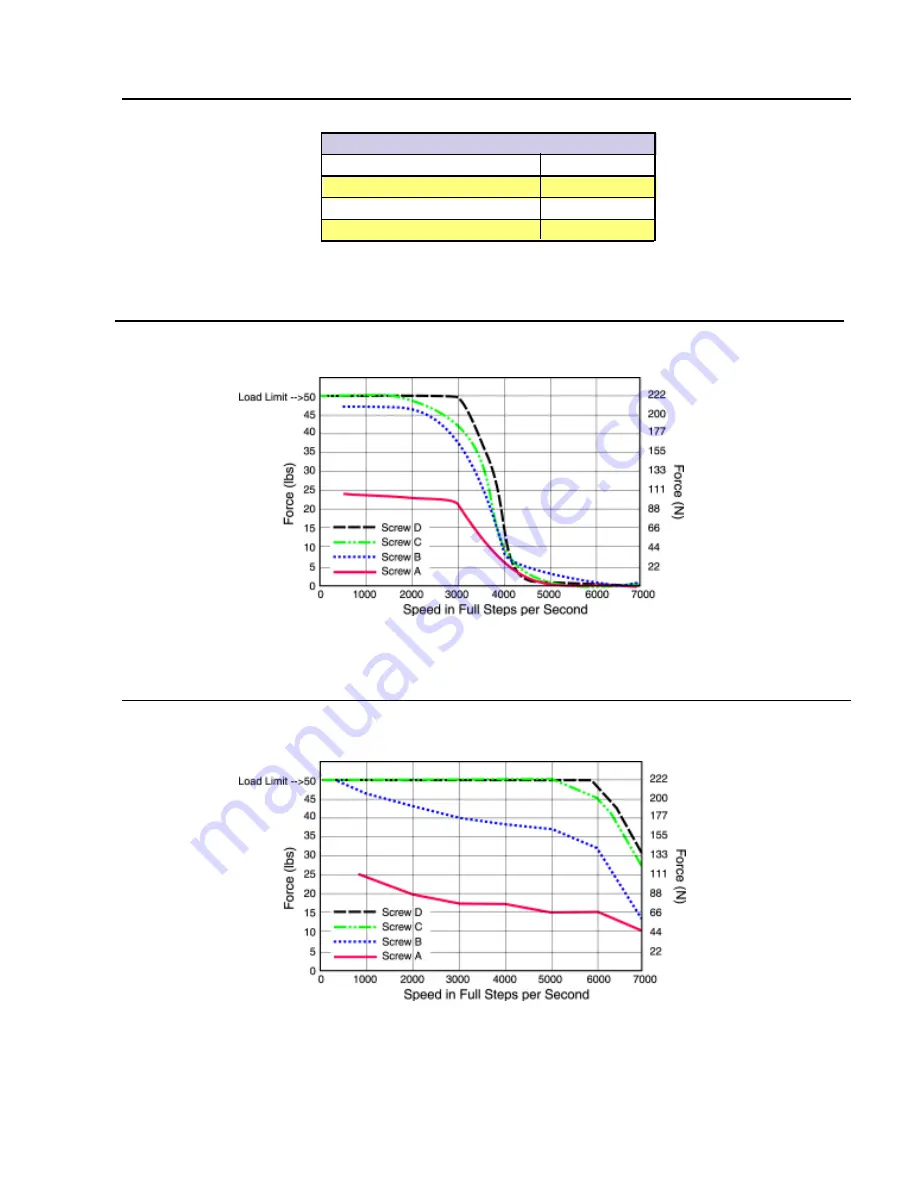
8
S p e e d - F o r c e C u r v e : 2 4 V D C
Refer to Table 1. 5 for screw pitch information
Figure 1.6: Speed-Force Curve - 24VDC (100% Current)
L i n e a r A c t u a t o r M D r i v e M o t i o n C o n t r o l 1 7 1 3 S p e c s a n d S p e e d - F o r c e
C u r v e s
Table 1.4: Linear Actuator MDrive17 Motion Control Motor Specifications
S p e e d - F o r c e C u r v e : 4 5 V D C
Refer to Table 1. 5 for screw pitch information
Figure 1.7: Speed-Force Curve - 45VDC (100% Current)
MDI17 Linear Actuator
Maximum Thrust lbs (kg)
50 (22.7)
Maximum Screw Deflection
±1°
Backlash inches (mm)
0.005 (0.127)
Weight (Motor+Driver) oz (gm)
9.2 (0.127)
Summary of Contents for 17
Page 1: ...OPERA TING INSTRUCTIONS T intelligent motion systems inc Excellence in MotionTM TM ...
Page 5: ...3 Part 1 General Information and Hardware Specifications ...
Page 6: ...4 Intentionally Left Blank ...
Page 19: ...17 Part 2 Connecting Configuring and Programming the MDrive Motion Control ...
Page 20: ...18 Intentionally Left Blank ...