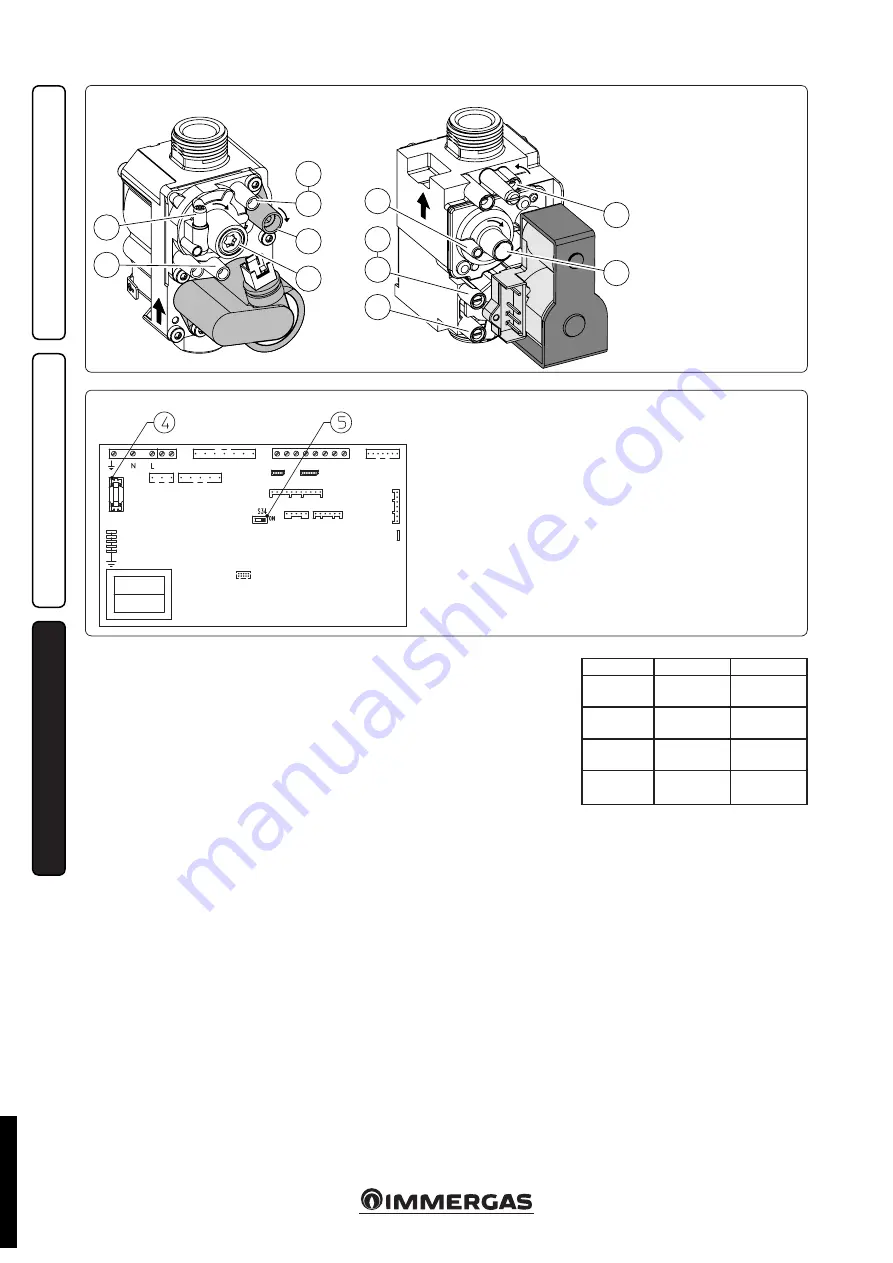
30
+
+
3
12
2
1
P1
P3
+
+
3
12
1
P1
2
P3
3-3
3-4
INS
TALLER
US
ER
MAINTEN
AN
CE TECHNI
CI
AN
3.4 CONVERTING THE BOILER TO
OTHER TYPES OF GAS.
If the boiler has to be converted to a different gas
type to that specified on the data plate, request
the relative conversion kit for quick and easy
conversion.
The appliance gas conversion must be carried out
by a qualified technician (e.g. Authorised After-
Sales Technical Assistance Service).
To convert to another type of gas the following
operations are required:
- remove the voltage from the appliance;
- replace the nozzle located between the gas pipe
and gas/air mixing sleeve (Part. 6 Fig. 1-28),
taking care to remove the voltage from the
appliance during this operation;
- apply voltage to the appliance;
- calibrate the number of fan revs. (Par. 3.5);
- adjust the correct air/gas ratio (Par. 3.6);
- seal the gas flow rate devices (if adjusted);
- after completing conversion, apply the sticker,
present in the conversion kit, near the data-
plate. Using an indelible marker pen, cancel
the data relative to the old type of gas.
These adjustments must be made with reference
to the type of gas used, following that given in
the table (Par. 3.18).
3.5 CALIBRATION OF NUMBER
OF FAN REVS.
Attention:
verification and calibration is
necessary, in the case of transformation to other
types of gas, in the extraordinary maintenance
phase with replacement of the circuit board,
air/gas circuit components or in the case of
installations with fume extraction systems, with
horizontal concentric pipe measuring more
than 1 metre.
The boiler heat output is correlated to the
length of the air intake and flue exhaust pipes.
This decreases with the increase of pipe length.
The boiler leaves the factory adjusted for
minimum pipe length (1m). It is therefore
necessary, especially in the case of maximum
pipe extension, to check the ∆p gas values after at
least 5 minutes of burner functioning at nominal
heat output, when the temperatures of the intake
air and exhaust flue gases have stabilised. Adjust
the nominal and minimum heat output in the
domestic hot water and central heating modes
according to the values in the table (Par. 3.18)
using the differential manometers connected to
the ∆p gas pressure point (13 and 14 Fig. 1-28).
Enter in the M5 menu (Parag. 3.8) and adjust
the ignition power “P50”, meanwhile under
“SERVICE” adjust the following parameters:
- boiler maximum heat output “P62”;
- boiler minimum heat output “P63”;
- maximum central heating output “P64”;
- minimum central heating output “P65”.
Below find the default settings present on the
boiler:
P50
36 %
40%
P62
G20:
5100 (rpm)
LPG:
4600 (rpm)
P63
G20:
980 (rpm)
LPG:
1020 (rpm)
P64
G20:
5100 (rpm)
LPG:
4600 (rpm)
P65
G20:
980 (rpm)
LPG:
1020 (rpm)
P.C.B.
Key:
1 - Gas valve inlet pressure
point
2 - Gas valve outlet pressure
point
3 - Off/Set adjustment screw
12 - Outlet gas flow rate
adjuster
Gas Valve 8205
Gas Valve 848
Key:
4 - 3,15 AF fuse
5 - S34 selector: On = external probe; Off = system supervisor
STD.002229/002
Summary of Contents for VICTRIX ZEUS SUPERIOR 32 2 ERP
Page 1: ...VICTRIX SUPERIOR 32 2 ERP Instruction and warning book IE 1 037985ENG STD 002229 002 ...
Page 2: ...STD 002229 002 ...
Page 44: ...44 STD 002229 002 ...
Page 45: ...45 STD 002229 002 ...
Page 46: ...46 STD 002229 002 ...
Page 47: ...47 STD 002229 002 ...