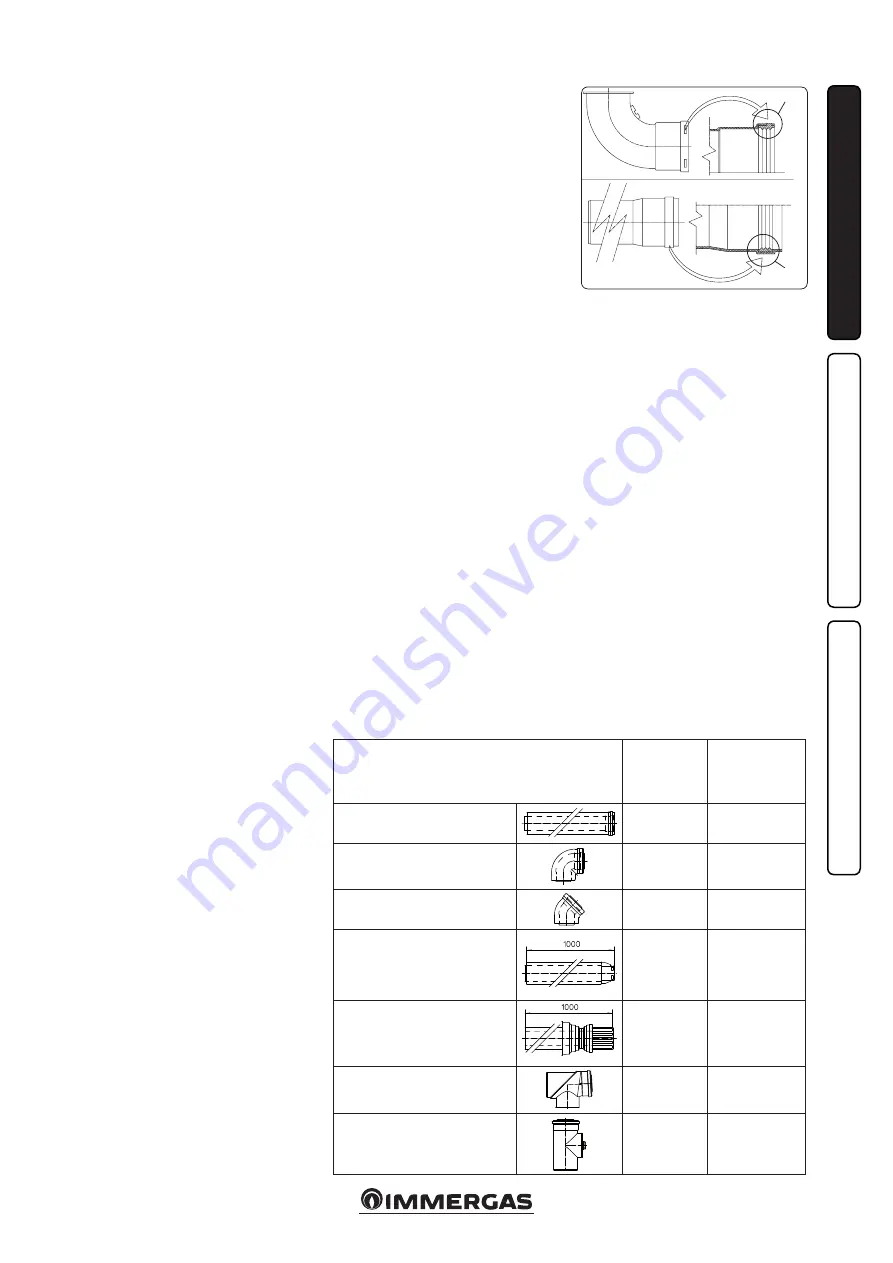
9
(
A
)
(
B
)
1-8
INS
TALLER
US
ER
MAINTEN
AN
CE TECHNI
CI
AN
1.9 IMMERGAS FLUE SYSTEMS.
Immergas supplies various solutions separately
from the boilers regarding the installation of air
intake terminals and flue extraction, which are
fundamental for boiler operation.
Attention: the boiler must be installed
exclusively with an original Immergas “Green
Range” inspectionable air intake device and
fume evacuation system made of plastic, as
required by the regulations in force.
The plastic pipes cannot be installed outdoors,
for tracts longer than 40 cm, without suitable
protection from UV rays and other atmospheric
agents.
This system can be identified by an
identification mark and special distinctive
marking bearing the note: “only for condensing
boilers”.
• Resistance factors and equivalent lengths.
Each flue component has a
Resistance Factor
based on experimental tests and specified
in the table below. The Resistance Factor for
individual components is independent from
the type of boiler on which it is installed
and has a dimensionless size. It is however,
conditioned by the temperature of the fluids
that pass through the pipe and therefore,
varies according to applications for air intake
or flue exhaust. Each single component has a
resistance corresponding to a certain length
in metres of pipe of the same diameter; the
so-called
equivalent length
, obtained from the
ratio between the relative Resistance Factors.
All boilers have an experimentally obtainable
maximum Resistance Factor equal to 100.
The maximum Resistance Factor allowed
corresponds to the resistance encountered with
the maximum allowed pipe length for each
type of Terminal Kit. This information allows
calculations to be made to verify the possibility
of setting up various flue configurations.
•
Positioning of the gaskets (black) for “green
range” flue extraction systems.
Position the
gasket correctly (for bends and extensions)
(Fig. 1-8):
- gasket (A) with notches, to use for bends;
- gasket (B) without notches, to use for
extensions.
N.B.:
if component lubrication (already carried
out by the manufacturer) is not sufficient,
remove the residual lubricant using a dry cloth,
then to ease fitting spread the elements with
common or industrial talc.
• Coupling extension pipes and concentric
elbows. To install push-fitting extensions with
other elements of the flue, proceed as follows:
Install the concentric pipe or elbow with the
male side (smooth) on the female section
(with lip seal) to the end stop on the previously
installed element in order to ensure sealing
efficiency of the coupling.
Attention:
if the exhaust terminal and/or
extension concentric pipe needs shortening,
consider that the internal duct must always
protrude by 5 mm with respect to the external
duct.
•
N.B.:
for safety purposes, do not obstruct
the boiler intake-exhaust terminal, even
temporarily.
•
N.B.:
when installing horizontal pipes,
a minimum inclination of 3% must be
maintained and a section clip with pin must
be installed every 3 metres.
1.10 TABLES OF RESISTANCE FACTORS
AND EQUIVALENT LENGTHS.
TYPE OF DUCT
Resistance
Factor
(R)
Equivalent
length in m of
concentric pipe
Ø80/125
Concentric pipe Ø80/125 m 1
2.1
1
Concentric bend 90° Ø80/125
3.0
1.4
Concentric bend 45° Ø80/125
2.1
1
Terminal complete with concentric
horizontal intake-exhaust Ø80/125
2.8
1.3
Terminal complete with concentric
vertical intake-exhaust Ø80/125
3.6
1.7
Concentric bend 90° Ø80/125 with
inspection
3.4
1.6
Stub pipe with inspection Ø80/125
3.4
1.6