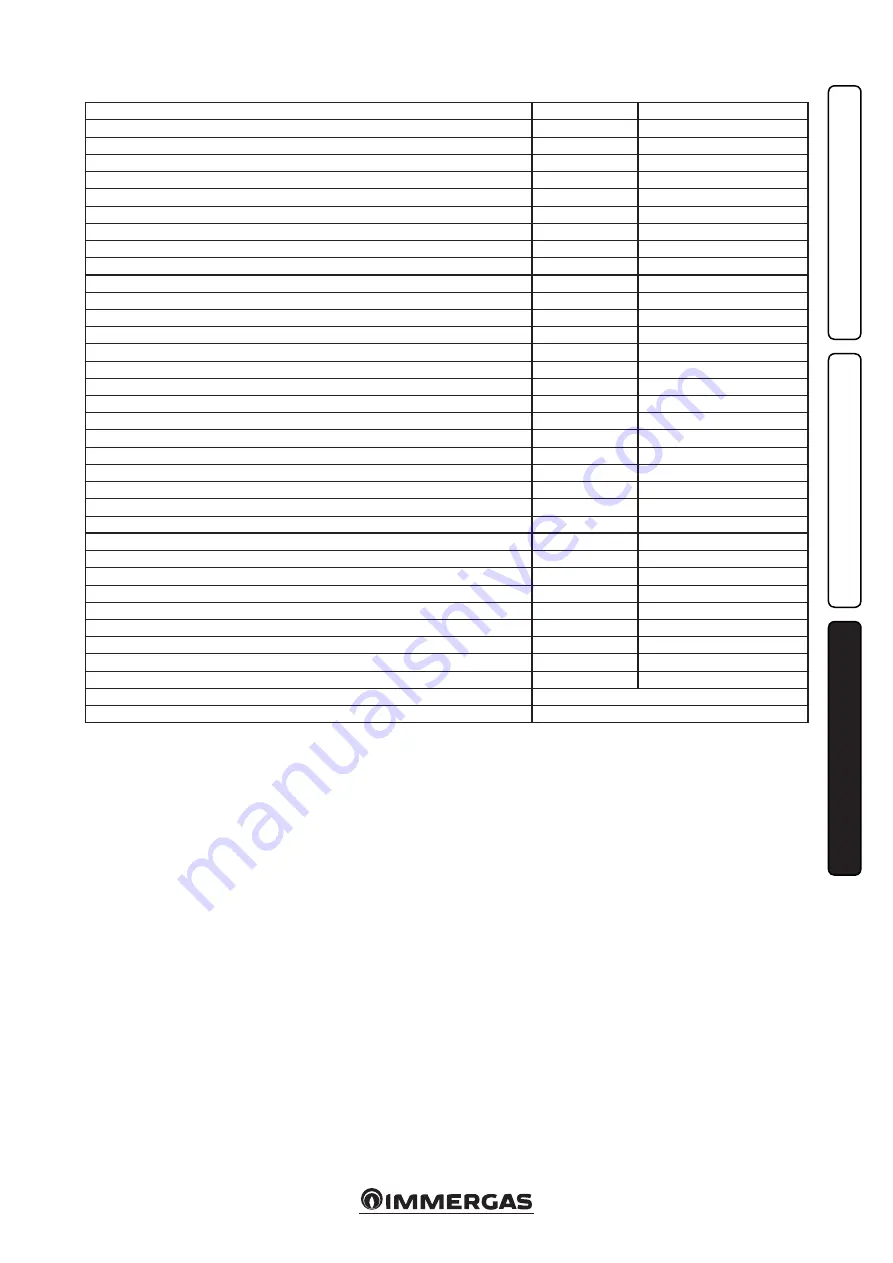
23
INS
TALL
AT
O
R
US
ER
MAINTEN
AN
CE TECHNI
CI
AN
- The data relevant to domestic hot water per-
formance refer to a dynamic inlet pressure of
2 bar and an inlet temperature of 15°C; the
values are measured directly at the boiler outlet
considering that to obtain the data declared
mixing with cold water is necessary.
- The max. sound level emitted during boiler
operation is < 55dBA. The sound level value is
referred to semianechoic chamber tests with
boiler operating at max. heat output, with
extension of flue gas exhaust system according
to product standards.
3.20 TECHNICAL DATA.
Nominal heat input
kW (kcal/h)
26.2 (22492)
** DHW minimum heat input
kW (kcal/h)
8.3 (7116)
CH minimum heat input
kW (kcal/h)
10.9 (9357)
Nominal heat output (useful)
kW (kcal/h)
23.8 (20468)
** DHW minimum heat output (useful)
kW (kcal/h)
7.0 (6020)
CH minimum heat output (useful)
kW (kcal/h)
9.4 (8084)
* Efficiency at nominal heat output
%
91.0
* Efficiency at 30% nominal heat output load
%
89.3
Heat loss at case with burner On/Off
%
2.30 / 1.20
Heat loss at flue with burner On/Off
%
6.70 / 0.09
Central heating circuit max. operating pressure
bar
3
Central heating circuit max. operating temperature
°C
90
Adjustable central heating temperature
°C
35 - 85
System expansion vessel total volume
l
4.0
Expansion vessel factory-set pressure
bar
1
Water content in generator
l
2.5
Total head available with 1000 l/h flow rate
kPa (m H
2
O)
24,52 (2,5)
Hot water production useful heat output
kW (kcal/h)
23.8 (20468)
** Domestic hot water adjustable temperature
°C
10 - 60
** Min. pressure (dynamic) domestic hot water circuit
bar
0.3
** Domestic hot water circuit max. working pressure
bar
10
** Minimum D.H.W. flow rate
l/min
1.5
Drawing capacity in continuous duty with UB Immergas (∆T 30°C)
l/min
11,1
Weight of full boiler
kg
28.0
Weight of empty boiler
kg
25.5
Electrical connection
V/Hz
230/50
Power input
A
0.44
Installed electric power
W
95
Pump consumption
W
87
Equipment electrical system protection
-
IPX4D
Boiler flue circuit resistance
Pa
1.3
NO
X
class
-
3
Weighted NO
X
mg/kWh
139
Weighted CO
mg/kWh
52
Type of appliance
B11BS
Category
II2H3+
- *Efficiencies refer to the lower heating value.
- ** When the boiler is connected to an external
cylinder.
Summary of Contents for 3.020857
Page 1: ...MINI NIKE X 24 3 E Instruction booklet and warning IE 1 038792ENG...
Page 2: ......
Page 20: ...20 3 5 4 4 5 6 6 d d c INSTALLATOR USER MAINTENANCE TECHNICIAN...
Page 25: ...25...
Page 26: ...26...
Page 27: ...27...