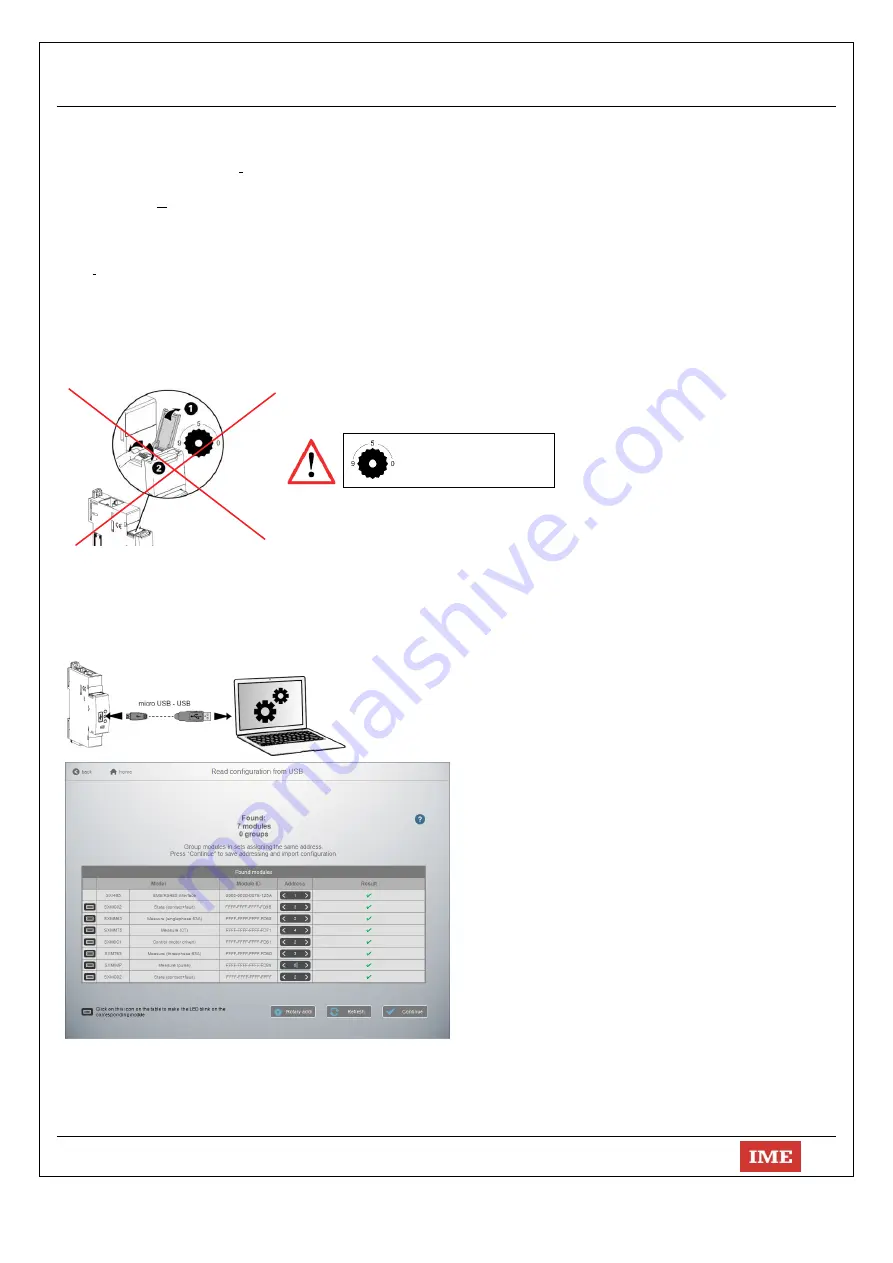
13 / 15
Nemo SX - Multifunction state module
Cat. N°:
SXMC02
6. SYSTEM ARCHITECTURES
(continued)
6.2 Supervised system
(Computer Supervisory System)
(continued)
6.2.2 Supervised system with remote addressing (through a computer)
Remote addressing advantages:
-
Whole of configuration (addresses and functions) can be done a remotely through the Nemo SX Configuration software
-
Configuration software available for free
-
Automatic detection of the Nemo SX modules installed in the system (characteristics, functions, configuration...)
-
Increased settings possibilities: load shedding function
-
Increased addressing: up to 32 Modbus/Nemo SX interfaces
-
Increased addressing: up to 247 Modbus addresses in a system
Programming procedure:
. For Nemo SX modules which need some: possible through the lateral DIP-switches of each Nemo SX
module or via the configuration software
(see § “Module configuration”)
.
Addressing procedure:
. It is not necessary to address the Nemo SX modules.
The track wheel must be left in default position “0”.
. All the addressing/configuring procedure will be done with the Configuration Software (available online for free)
. With remote addressing, the software does the automatic detection of modules installed in the system, but the supervision is not possible until
the user assigns the remote address and all the characteristics to each module.
Note: it is mandatory to connect the computer to the different Modbus/Nemo SX interface with a “Type B” micro USB
- USB cable (one interface
at a time).
[For more details, refer to the technical sheet Modbus/Nemo SX interface]
Note for Measure Module “3x single phase”:
This module is to be consider as 3 modules with 3 different Modbus Address. The module takes automatically the two addresses immediately
following to the programmed one (e.g. Programmed address = 2, Addresses of the module 2, 3, 4)
Technical data sheet: IDP000169EN_04
Updated: 30/09/2020
Created: 31/08/2017
The track wheel must be
left in position “0”.