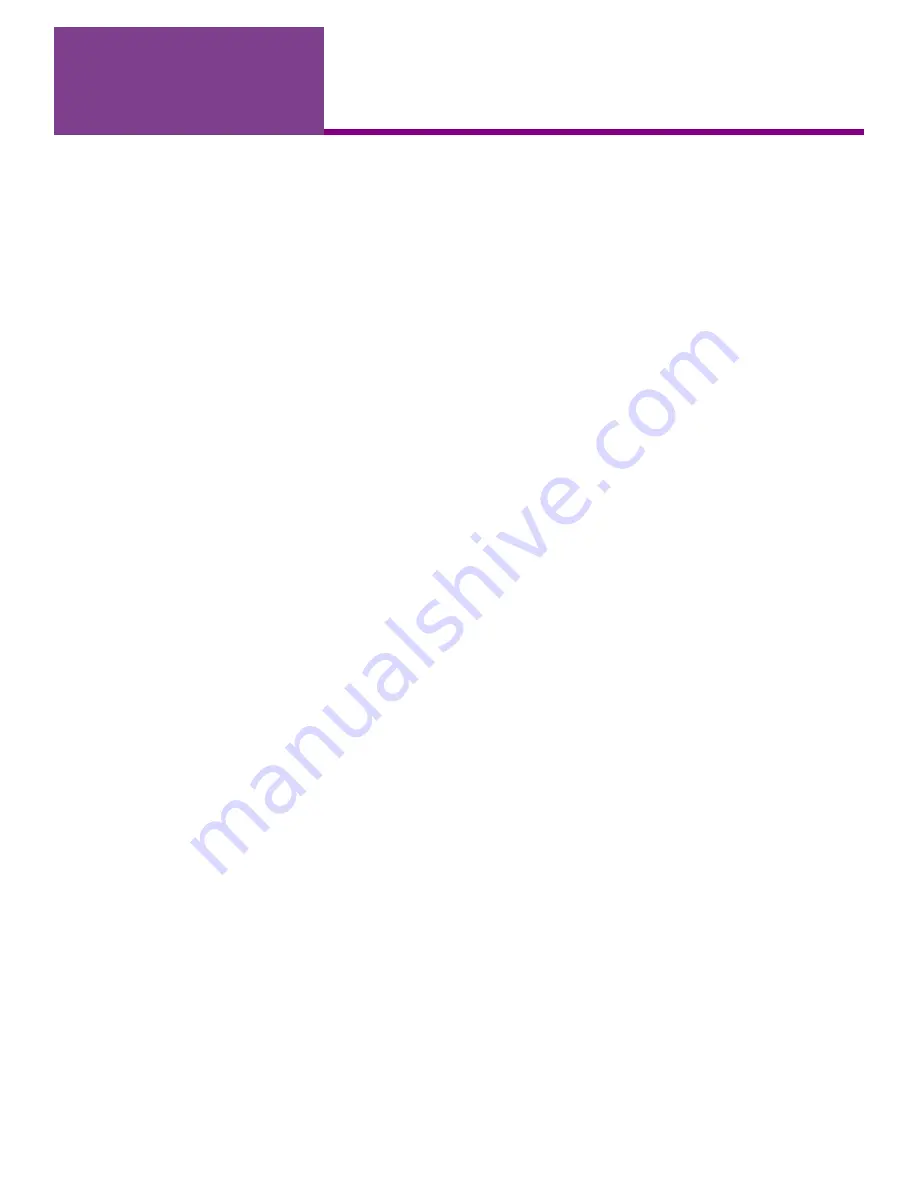
Section 2
Section 4
Special Welding Techniques
19
19
Shielding Gas Selection for Steels
The choice of gas depends on two factors, weld penetration and appearance. Pure argon provides the best looking welds,
but has the least weld penetration. To increase penetration C02 is added to the mix. C02 percentages range from 10% to
25% depending on the desired level of penetration. Stainless steel will typically use a mix of 82% Argon and 18% C02.
Other mixes are used to achieve different results.
Summary of Contents for QuikLinx 10700
Page 9: ...Safety Precautions Section 1 8 Symbols and Definitions ...
Page 28: ...Section 2 Section 7 Exploded Diagram 27 Figure 21 1 9 8 12 13 4 5 7 6 10 11 3 2 ...
Page 30: ...Section 2 Section 7 Exploded Diagram 29 Figure 22 5 1 2 3 4 ...
Page 32: ...Please visit us on the web www imageindustries com twitter studwelding ...