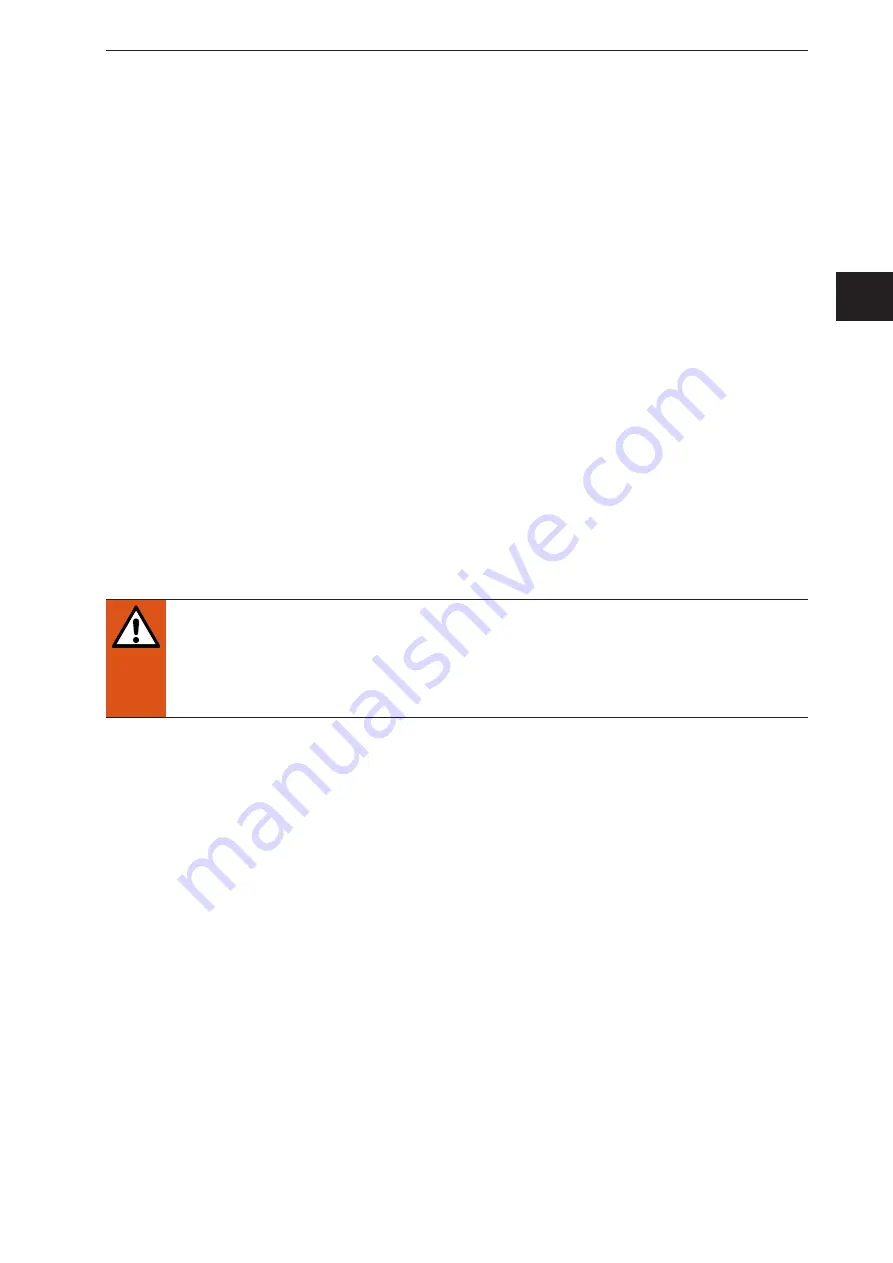
3
ZZ1102 I/O module
UK
2 Safety instructions
●
The devices described are subcomponents for integration into a system�
– The operator is responsible for the safety of the system�
– The system architect undertakes to perform a risk assessment and to create documentation in
accordance with legal and normative requirements to be provided to the operator and user of the
system� This documentation must contain all necessary information and safety instructions for the
operator, the user and, if applicable, for any service personnel authorised by the architect of the
system�
– The system manufacturer is responsible for the proper functioning of the application programs�
●
Read this document before setting up the devices and keep it during the entire service life�
●
The devices must be suitable for the corresponding applications and environmental conditions without
any restrictions�
● Use the devices for their intended purpose (→ „3 Functions and features“).
●
If the operating instructions or the technical data are not adhered to, personal injury and/or damage to
property may occur�
●
The manufacturer assumes no liability or warranty for any consequences caused by tampering with
the devices or incorrect use by the operator�
●
Installation, electrical connection, set-up, programming, configuration, operation and maintenance of
the devices must be carried out by personnel qualified and authorised for the respective activity�
●
Protect units and cables against damage�
●
Because of the requirements for electromagnetic interference emissions, the devices are intended for
use in industrial environments� The devices are not suitable for use in domestic areas�
WARNING
If the set is used for operator protection, death or serious irreversible injuries are possible�
The set is an assistance system and only supports the recognition of objects� The operator of
the system bears full responsibility for persons within the area monitoring�
►
Only use the set for support as an assistance system�
3 Functions and features
The ZZ1102 set digitises all kinds of input signals for the O3M 3D sensor� Moreover, the output signals of
the O3M 3D sensor can be processed in an analogue or digital way�
For this purpose, the BasicController included in the set is operated with the supplied CAN/power adapter
cable�