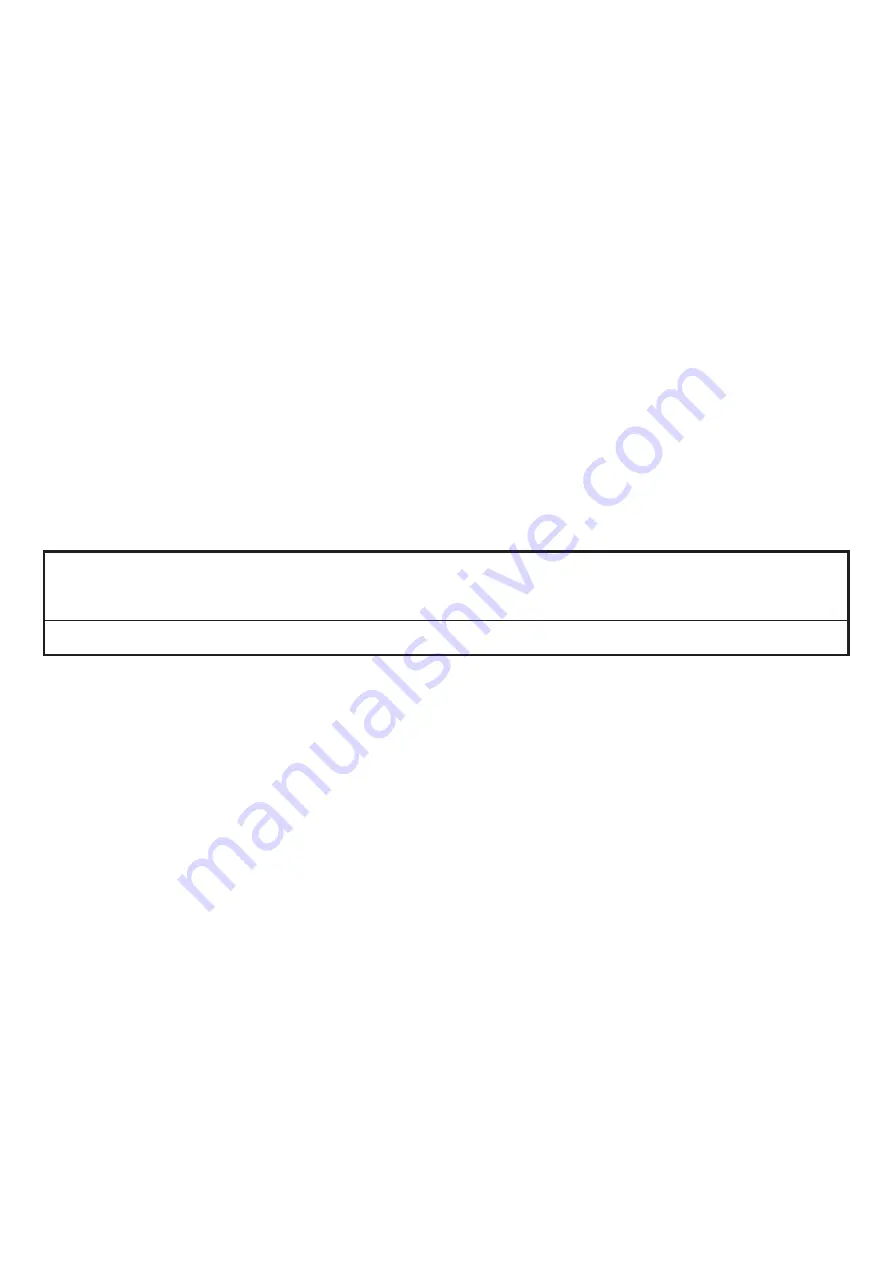
12
9 Operation
9.1 Switching state of the outputs
9.1.1 The safe state
The safe state is when at least one of the outputs A1 and A2 (OSSD) is switched
off (zero-current state: logic "0")�
If one of the outputs A1 and A2 is switched off, the subsequent safety-related logic
unit must bring the complete system into the state defined as safe�
9.1.2 The switched state
If the damping element is in the enable zone and if there is no sensor error, both
outputs A1 and A2 (OSSD) are enabled (logic "1")�
9.1.3 Output characteristics
The output characteristics are compatible with the input characteristics to
EN 61131-2 type 1 or 2:
Logic "1"
≥ 15 V
2���15 mA
≥ 11 V
15���30 mA
Logic "0"
≤ 5 V
leakage current 0�2 mA*)
*) pull-down current typ� 30 mA
9.1.4 Cross faults
• A cross fault between both outputs (A1 and A2) is detected by the fail-safe
sensor and leads to switching off the outputs (OSSD) at the next safety
request� The outputs A1 and A2 remain switched off until the error has been
removed�
• A cross fault between one of the two outputs (A1 or A2) and the supply voltage
leads to switching off the other output (A2 or A1) in case of a safety request�