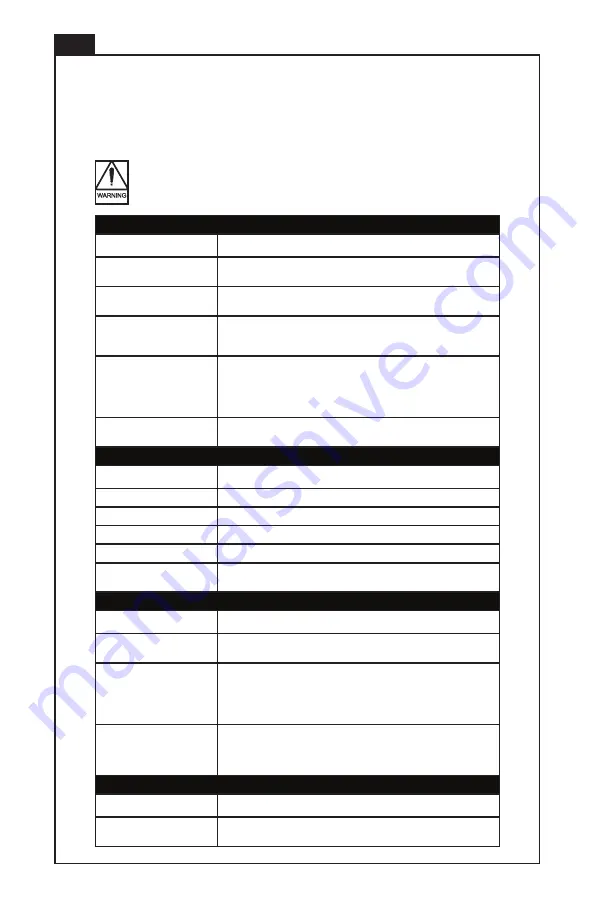
DOC No: 7936 REV
D
Fault Isolation
If the I-Drive does not meet its design performance or fails to operate correctly, refer to
the following tables for assistance in identifying the cause and remedy:
MOTOR WILL NOT OPERATE
Cause
Remedy
No power to motor.
Ensure proper voltage has been applied to motor power leads.
Check leads to ensure no short circuits are present.
Control Input lead is shorted.
Clear and isolate Control Input lead from Tachometer Out lead. Clear and
isolate Control Input lead from Common lead.
No Control Input applied.
Ensure proper control input is applied to Control Input lead.
If manual control I-Drive, adjust potentiometer clockwise.
Ensure control power supply common is connected to the Common lead.
Thermal Limit is active.
Turn off motor and wait for temperature to cool below 70°C (158°F). NOTE: If
power voltage and control signals are present, motor will automatically restart
when temperature is reached.
Reduce motor load conditions and/or improve cooling of motor housing if
persistent limit occurs.
Motor has been damaged.
Contact your Micropump Distributor or contact Micropump directly for replace-
ment product.
CYCLIC NOISE OR VIBRATIONS
Cause
Remedy
Loose motor mounting bolts.
Tighten motor mounting bolts.
Foundation not rigid.
Relocate motor.
Pump loose on motor.
Tighten pump mounting bolts.
Pump is worn.
Replace or repair pump.
Tachometer Out lead is shorted
to FWD/REV lead.
Clear and isolate Tachometer Out lead from FWD/REV lead.
NO TACHOMETER SIGNAL
Cause
Remedy
No power to motor.
Ensure proper voltage has been applied to motor power leads.
Check leads to ensure no short circuits are present.
Improper wiring.
Check that the Tachometer Out lead is connected to the positive input of the
frequency counter.
Check that the common lead of the frequency counter is connected to the motor
Common lead.
Check leads to ensure no short circuits are present.
Motor is stopped.
Ensure proper voltage has been applied to motor power leads Ensure proper
control input is applied to Control Input lead.
If manual control I-Drive, adjust potentiometer clockwise.
Ensure control power supply common is connected to the Common lead.
MOTOR RUNS IN THE WRONG DIRECTION
Cause
Remedy
FWD/REV lead is shorted to
Common lead.
Clear and isolate FWD/REV lead from Common lead. Check leads to ensure no
short circuits are present.
Execution of troubleshooting steps, determination of root cause and
corrective actions should be performed by a skilled maintenance person.