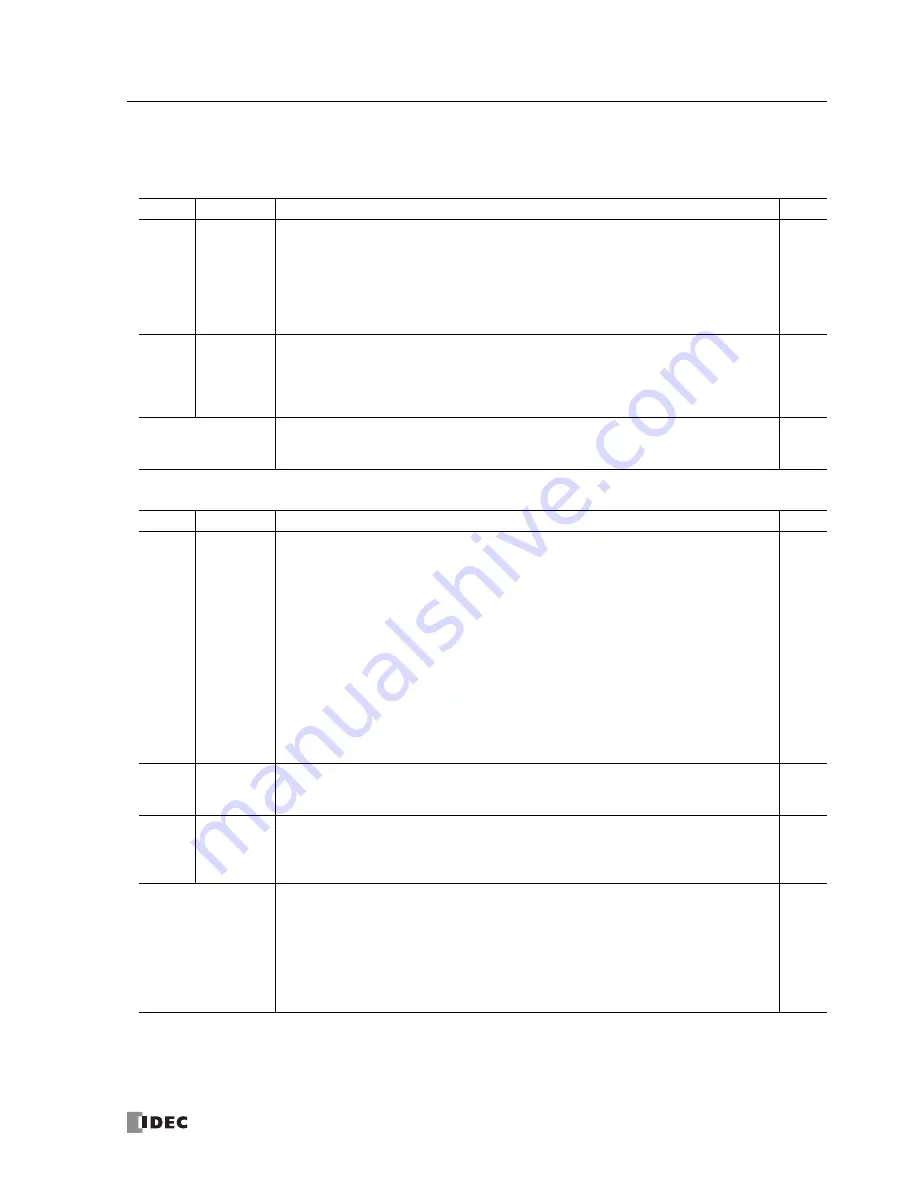
12: M
ODBUS
ASCII/RTU C
OMMUNICATION
FC5A M
ICRO
S
MART
U
SER
’
S
M
ANUAL
FC9Y-B1268
12-9
Device Addresses for Modbus Master
Special internal relays and special data registers are allocated to Modbus master communication as shown below.
Internal Relay and Special Internal Relay Device Addresses
Port 2
Ports 3 to 7
Description
R/W
M8005
—
Communication Error
When a communication error occurs, communication error special internal relay M8005 turns
on for 1 scan time immediately after the error. Communication error occurs when communica-
tion failure has repeated more than the designated retry cycles or when the master station
does not receive response within the designated receive timeout period. When a communica-
tion error occurs, the request is canceled and the next request is transmitted.
The completed request number and error code are stored to special data register D8053.
R
M8080
—
Modbus Communication Completion Relay
Immediately after a request communication has been completed, Modbus communication
completion relay M8080 turns on for 1 scan time. Similarly, when an error occurs, M8080 turns
on for 1 scan time. At the same time, the completed request number and error code are stored
to special data register D8053.
R
Function Area Settings
Request Execution Device
When a request execution device is turned on, the corresponding request is executed. When
communication is completed, the request execution device turns off automatically.
R/W
Data Register and Special Data Register Device Addresses
Port 2
Ports 3 to 7
Description
R/W
D8053
(Note)
—
Modbus Communication Error Code
When a Modbus communication is completed, the request number and error code are stored.
High-order 11 bits: Request No.
1 to 2040
Low-order 5 bits: Error code
00h: Normal completion
01h: Function error
02h: Access destination error (address out of range, device quantity out of range)
03h: Device quantity error, 1-bit write data error
11h: ASCII code error (ASCII mode only)
12h: Frame length error
13h: BCC error
14h: Slave number error
16h: Timeout error
R
D8054
Function
Area Set-
tings
Modbus Communication Transmission Wait Time
When the MicroSmart sends communication, transmission wait time can be designated by
storing a wait time value to D8054. Valid values are 1 through 5000 in milliseconds.
R/W
D8069-
D8099
—
Error Station Number and Error Code
When a communication error occurs in the Modbus communication, the slave number (high-
order byte) and error code (low-order byte) are stored to these data registers. Error codes are
the same as D8053. When the CPU module is powered up, these data registers are cleared.
R
Function Area Settings
Error Status
When a communication error occurs in the Modbus communication, the slave number (high-
order byte) and error code (low-order byte) are stored to the Error Status data registers allo-
cated to each request. Error codes are the same as D8053. When the CPU module is powered
up, these data registers are cleared.
When Use a single DR for all communication requests is selected, the Error Status data register
is shared by all requests. The value in the data register is overwritten every time an error
occurs.
R
Phone: 800.894.0412 - Fax: 888.723.4773 - Web: www.clrwtr.com - Email: [email protected]