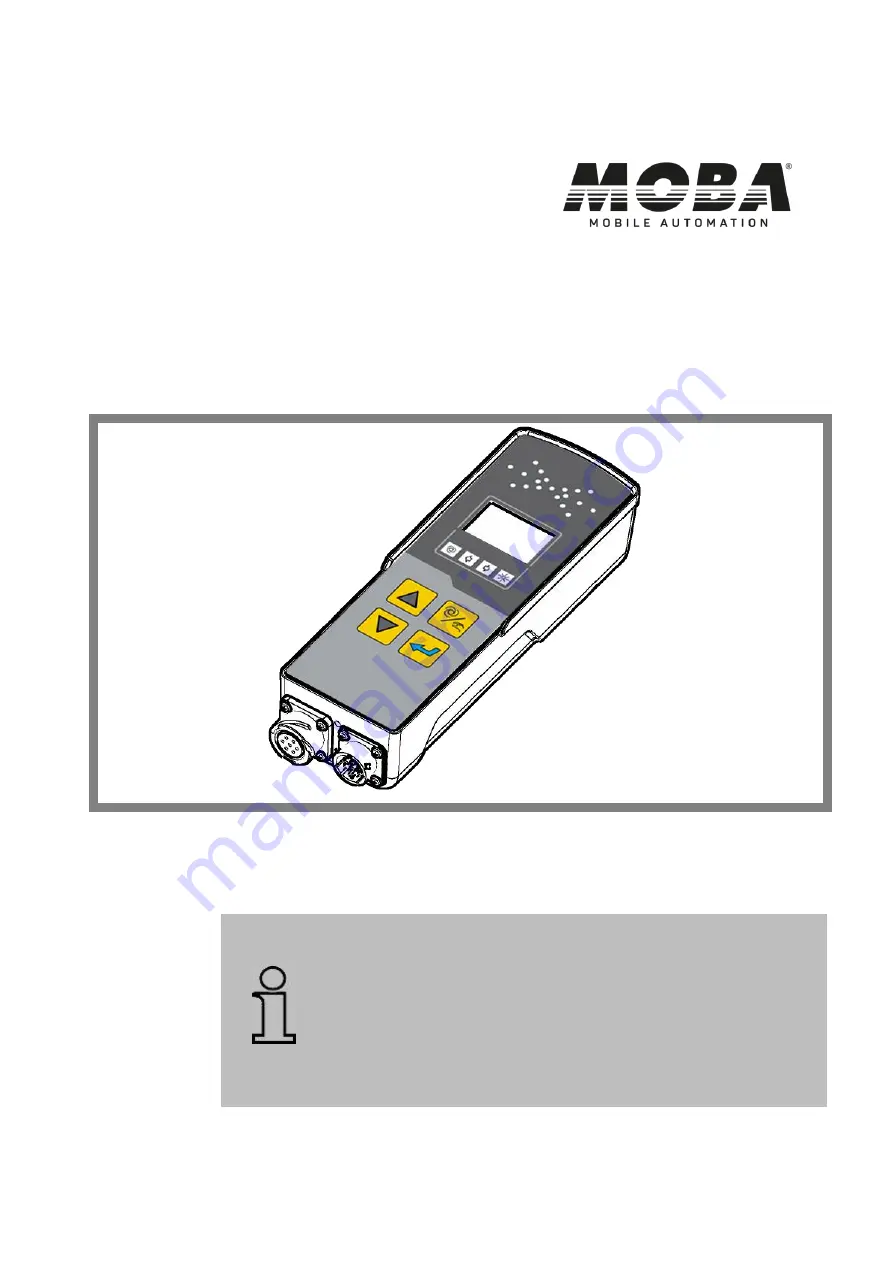
USER MANUAL
MOBA-Matic, CAN, as of Version
V2055
MMC-1000
Levelling System for paver, milling machines
and other mobile applications
Further applicable documents:
Specifications:
04-03-00415 | 04-21-21010 | 04-25-10300
04-21-10100 | 04-21-30070 | 04-60-11311
04-21-10102 | 04-21-40110 |
CE declaration of conformity
ENGLISH
Summary of Contents for MOBA-Matic MMC-1000
Page 7: ...Table of contents 7 12 Declaration of conformity 161 ...
Page 79: ...Operation 79 Graphical representation of the user menu ...
Page 161: ...Declaration of conformity 161 12 Declaration of conformity ...
Page 162: ...162 Declaration of conformity ...
Page 163: ...Declaration of conformity 163 ...
Page 164: ...164 Declaration of conformity ...
Page 165: ...Declaration of conformity 165 ...
Page 166: ...166 Declaration of conformity ...
Page 167: ...Declaration of conformity 167 ...
Page 168: ...168 Declaration of conformity ...
Page 171: ...Notes ...