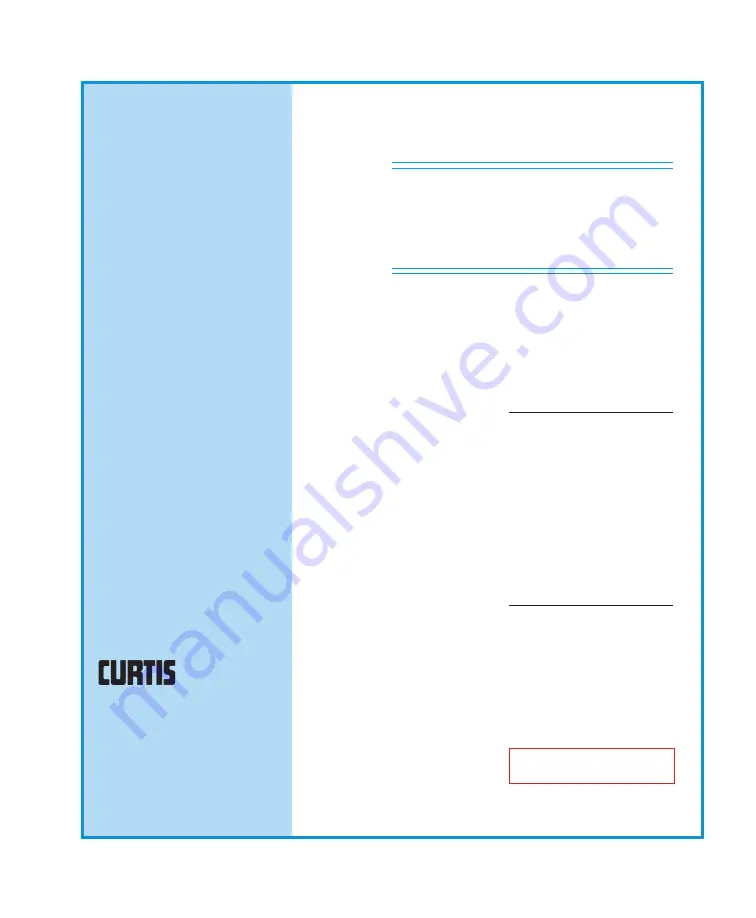
MANUAL
© 2003 CURTIS INSTRUMENTS, INC.
DESIGN OF CURTIS PMC 1200 SERIES
CONTROLLERS PROTECTED BY U.S.
PATENT NO. 4626750.
1214-8 / 1215-8 / 1219-8 Manual
p/n 16369, Rev. C: April 2003
CURTIS INSTRUMENTS, INC.
200 Kisco Avenue
Mount Kisco, NY 10509 USA
Tel: 914-666-2971
Fax: 914-666-2188
www.curtisinst.com
MultiMode™
MOTOR CONTROLLERS
1214-8
1215-8
1219-8