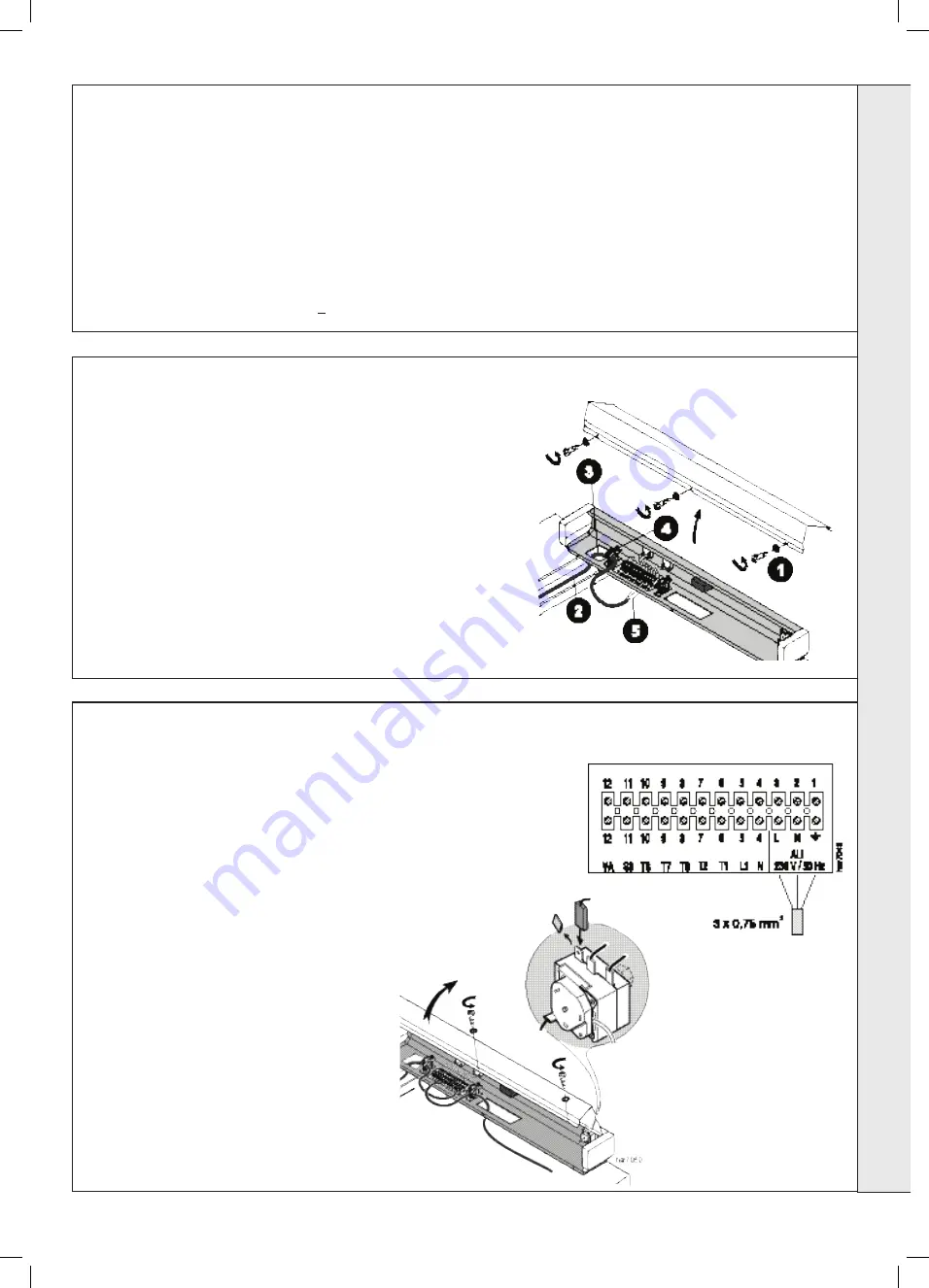
27
Viceroy GTS -
Installation & Servicing
INSTALLATION
39 ELECTRICAL CONNECTIONS
WARNING
. The electrical connections must be made by a
qualified professional. The electrical wiring has been carefully
checked in the factory and the internal connections of the
control panel must not be modified in any event.
The electrical connections should be made following the
information shown on the electrical diagrams delivered with the
unit and the directions given in the instructions.
The electrical connection must comply with standards in force.
The equipment must be powered by a circuit containing a
remote double-pole switch with opening > 3mm.
WARNING.
The boiler must be earthed.
All connections must be made using the terminal blocks provided
for this purpose at the back of the boiler control panel.
Connections cables are brought inside the boiler through cut-outs
provided in the boiler back panel, which are large enough for use
of commercially available conduit if required.
These cables are secured at the back of the control panel using
cable clamps (cable clamps supplied in a separate pack) that are
to be installed on the sheet metal.
40 BASIC CONNECTIONS
1.
To gain access to the connection strip, unscrew the three
screws on the rear of the control panel and open the panel.
2.
Pass the connecting cables to the control panel through the
two cut-outs in the rear panel of the boiler and route them to
the front via the cable channels. (See Frame 30).
3.
Pass the cables into the control panel through the
rectangular openings in the front top panel.
4.
Secure the cables to the base of the control panel with the
cable clamps.
5.
Connect the main supply to terminals 1, 2 and 3 of the
connecting strip as shown. (See also Frame 41)
41 CONNECTING OPTIONAL FEATURES
Flow Switch / Optional Safety Devices
If a flow switch or other safety control is to be
included in the system, connect the device(s)
in series in the safety circuit, (i.e. between
terminal 5 of the connecting strip and burner
terminal L1).
Burner Alarm Indicator
If an alarm indicator is to be included it should
be connected across terminal 12 (live) and
terminal 4 (neutral).
Safety Thermostat Alarm Indicator System
1. The unused insulated terminal on the
safety thermostat may be used to connect
an alarm signal. (This terminal becomes
live if the safety thermostat trips.)
2. Remove the insulation and connect the
live wire from the alarm indicator to the
unused terminal using a suitable spade
connector and the neutral to terminal 4.
INST
ALLA
TION