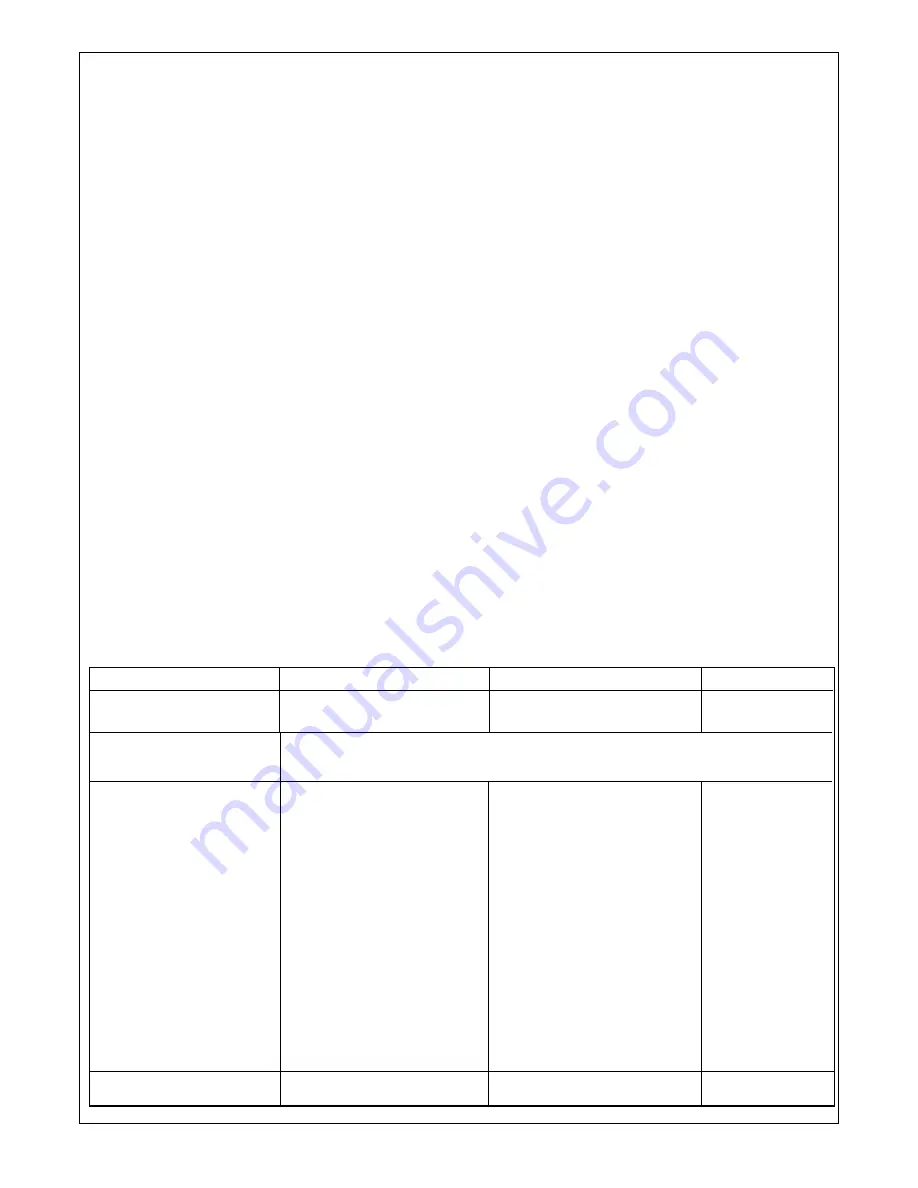
10
Classic FF -
Propane Installation & Servicing
GENERAL
6
SEALED SYSTEM REQUIREMENTS - cont.
Sizing procedure for expansion vessels: The volume of the expansion vessel (litres) fitted to a sealed system shall not be
less than that given by the table on the following page, multiplied by a factor of 0.8 (for flow temperatures of less than 88
o
C).
Safety valve setting
3.0 bar
2.5 bar
2.0 bar
Vessel charge and initial
0.5
1.0
1.5
0.5
1.0
1.5
0.5
1.0
system pressure
bar
bar
bar
bar
bar
bar
bar
bar
Total water content of system
Expansion vessel volume
(litres)
(litres)
25
2.1
2.7
3.9
2.3
3.3
5.9
2.8
5.0
50
4.2
5.4
7.8
4.7
6.7
11.8
5.6
10.0
75
6.3
8.2
11.7
7.0
10.0
17.7
8.4
15.0
100
8.3
10.9
15.6
9.4
13.4
23.7
11.3
20.0
125
10.4
13.6
19.5
11.7
16.7
29.6
14.1
25.0
150
12.5
16.3
23.4
14.1
20.1
35.5
16.9
30.0
175
14.6
19.1
27.3
16.4
23.4
41.4
19.7
35.0
200
16.7
21.8
31.2
18.8
26.8
47.4
22.6
40.0
225
18.7
24.5
35.1
21.1
30.1
53.3
25.4
45.0
250
20.8
27.2
39.0
23.5
33.5
59.2
28.2
50.0
275
22.9
30.0
42.9
25.8
36.8
65.1
31.0
55.0
300
25.0
32.7
46.8
28.2
40.2
71.1
33.9
60.0
Multiplying factors for
other system volumes
0.0833
0.109
0.156
0.094
0.134
0.237
0.113
0.20
7. Mains Connection
There must be no direct connection to the mains water supply
or to the water storage tank supplying domestic water, even
through a non-return valve, without the approval of the local
water authority.
8. Filling
The system may be filled by one of the following methods:
a. Through a cistern, used for no other purposes, via a ball
valve permanently connected directly to a service pipe
and / or a cold water distributing pipe.
The static head available from the cistern should be
adequate to provide the desired initial system design
pressure. The cold feed pipe from the cistern should
include a non-return valve and a stop valve with an
automatic air vent connected between them, the stop
valve being located between the system and the
automatic air vent. The stop valve may remain open
during normal operation of the system if automatic water
make-up is required.
b. Through a self-contained unit comprising a cistern,
pressure booster pump (if required) and, if necessary,
an automatic pressure reducing valve and flow restrictor.
The cistern should be supplied through a temporary
connection from a service pipe or cold water distributing
pipe.
This unit may remain permanently connected to the
heating system to provide limited automatic water
make-up. Where the temporary connection is supplied
from a service pipe or distributing pipe which also
supplies other draw-off points at a lower level then a
double check valve shall be installed upstream of the
draw-off point.
c. Through a temporary hose connection from a draw-off tap
supplied from a service pipe under mains pressure. Where
the mains pressure is excessive a pressure-reducing valve
shall be used to facilitate filling.
The following fittings shall form a permanent part of the
system and shall be fitted in the order stated:
A stop valve complying with the requirements of
BS. 1010, Part 2 (the hose from the draw-off tap shall be
connected to this fitting).
A test cock.
A double check valve of an approved type.
• Thoroughly flush out the whole of the system with cold
water, without the pump in position.
• With the pump fitted, fill and vent the system until the
pressure gauge registers 1.5 bar (21.5lb/in
2
).
Examine for leaks.
• Check the operation of the safety valve by manually
raising the water pressure until the valve lifts. This
should occur within ± 0.3 bar (± 4.3lb/in
2.
) of the pre-set
lift pressure.
• Release water from the system until the initial system
design pressure is reached.
• Light the boiler and heat the system to the maximum
working temperature. Examine for leaks.
• Turn off the boiler and drain the system while still hot.
• Refill and vent the system.
Summary of Contents for FF 350
Page 1: ......
Page 39: ...Classic FF Propane Installation Servicing 39 NOTES...