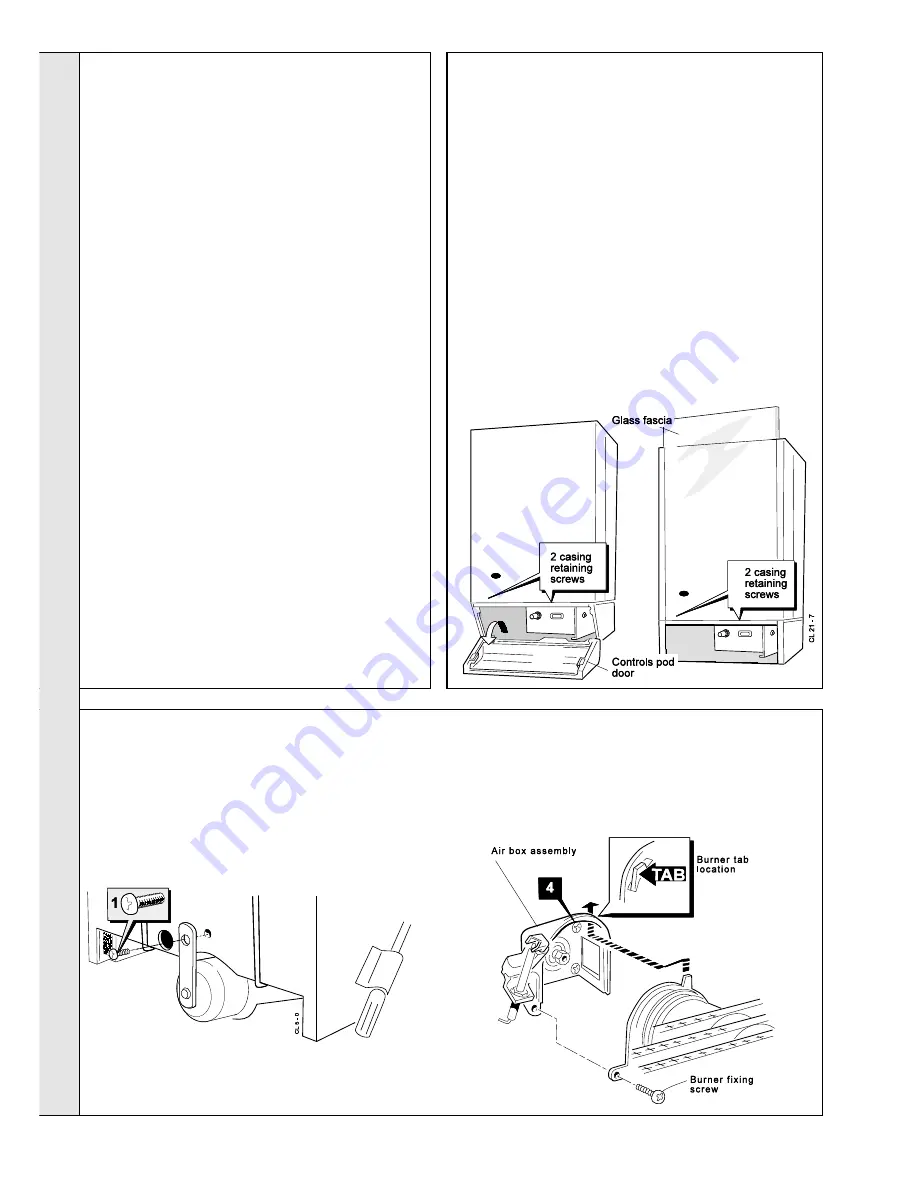
26
Classic
LXFF, FF
-
Installation
SER
VICING
To ensure the continued safe and efficient operation of the
appliance, it is recommended that it is checked at regular
intervals and serviced as necessary. The frequency of
servicing will depend upon the installation condition and
usage, but should be carried out at least annually. It is the
law that any service work must be carried out by a CORGI
registered installer.
a.
Light the boiler and, using the flue sampling point
(provided on the top RH side of the back panel) carry out
a pre-service check, noting any operational faults.
b.
Clean the main burner.
c.
Clean the heat exchanger.
d.
Clean the main and pilot injectors.
e.
Remove any debris from inside the base of the casing.
f.
Check that the flue terminal is unobstructed and that the
flue system is sealed correctly.
g.
If the appliance has been installed in a compartment,
check that the ventilation areas are clear.
The servicing procedures are covered more fully in Frames
48 to 52 and must be carried out in sequence.
WARNING.
Disconnect the electrical supply and turn off gas
supply.
IMPORTANT.
After completing the servicing or exchange of
components always test for gas soundness and carry out
functional checks as appropriate.
When work is complete the casing MUST be correctly
refitted, ensuring that a good seal is made.
T
he boiler must NOT be operated if the casing is not
fitted.
Note.
In order to carry out either servicing or replacement of
components, the boiler casing must be removed. Refer to
Frame 48.
3.
Pull the HT lead connection off the printed circuit board and
pull the lead upwards through the bottom panel grommet.
4.
Remove the 4 screws retaining the air box/pilot assembly to
the vertical manifold and carefully remove the assembly.
49 BURNER AND AIR BOX REMOVAL
1.
Remove the screw retaining the front burner support strap
to the combustion chamber. Remove the M5 pozi situated
at the LH bottom rear of the burner and pull the burner
downwards to disengage the retention tab. Remove the
burner to a safe place for inspection and cleaning.
2.
Remove the control box fixing screw. Pull the box forward
and downward to disengage.
Standard model
Deluxe model (LX)
1.
If the
Classic Sealed System Unit
is fitted (Standard boiler
only), lift off the casing.
2. Deluxe model (LX)
-Lift the glass fascia and pull the sliding
catch out to retain the glass in the upper position. Release
the 2 captive screws at the bottom of the casing. Swing the
bottom of the boiler casing out until the controls pod casing
has cleared the controls, then unhook the casing top from
the back panel. Retain the casing in a safe place.
Standard model
- Open the controls pod door and release
the 2 captive screws at the bottom of the casing. Swing the
bottom of the boiler casing out until the controls pod casing
has cleared the controls, then unhook the casing top from
the pack panel. Retain the casing in a safe place.Where the
removal of the casing is impaired by a pelmet, the instruction
in Frame 2 (page 6) should should be followed.
3.
Isolate the gas supply at the service cock fitted to the boiler.
48 BOILER CASING REMOVAL
SERVICING
47 SCHEDULE
Summary of Contents for Classic FF230
Page 1: ......