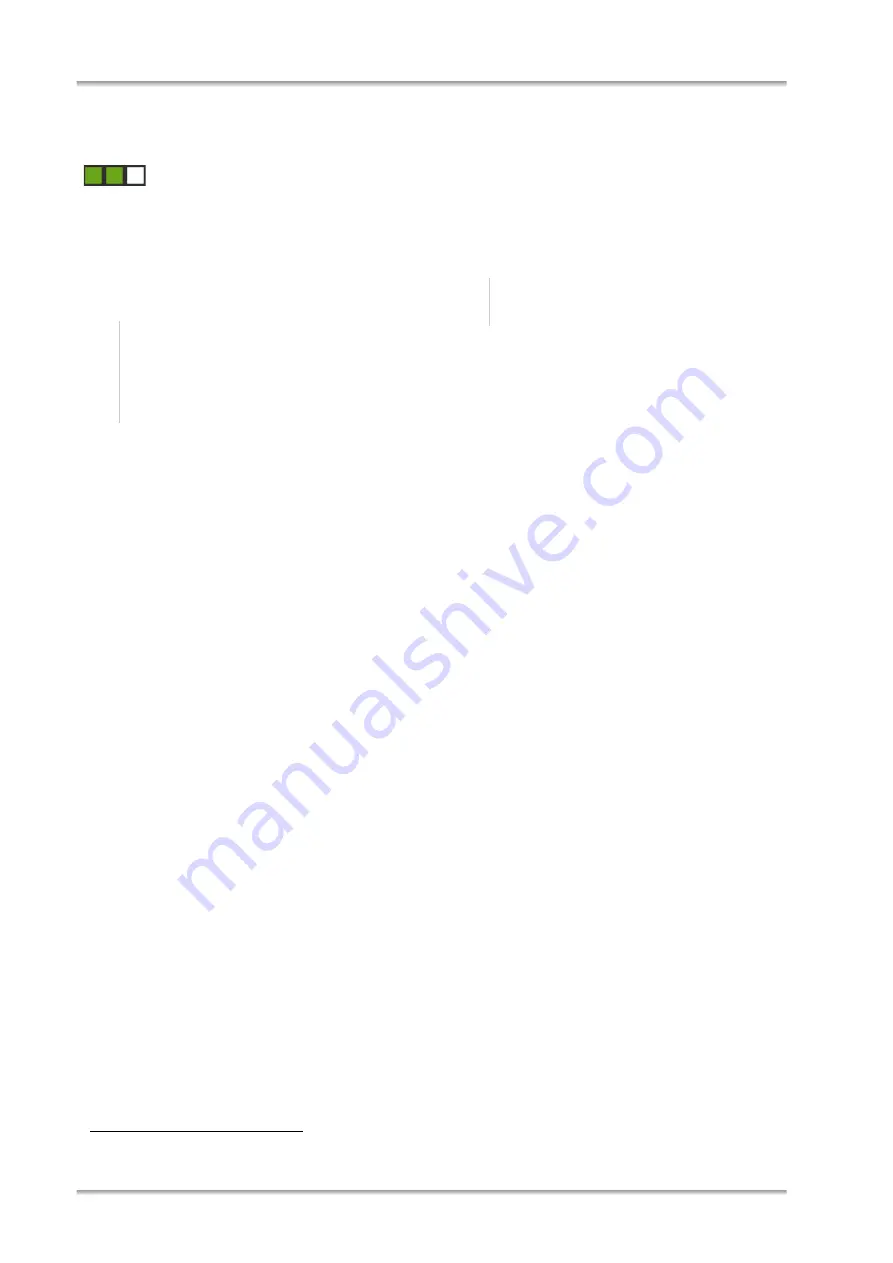
6 Measurement Settings – Products
14
E15IB001EN-N
6.3.3 Check Density Stability
1
TIP:
“Yes” is the recommended standard setting.
Select “No” if the characteristics of your sample
prevent achieving density stability (inhomogeneous
samples like toothpaste or unstable samples like
H
2
O
2
).
6.3.4 Hold Time
The instrument will wait this time span after all
specified stability conditions are met, and then
determines the measurement result. This gives the
sample time for temperature conditioning.
TIP:
A hold time of 4 min for DMA 501 and 5 min for
DMA 1001 is recommended when you measure
without checking density stability.
When you check density stability, the standard hold
time is 0 min.
6.3.5 Timeout
If a stable measurement result cannot be achieved,
the instrument will abort the measurement process
after the specified timeout (e.g. 10 min).
The time span begins with measurement start.
TIP:
A timeout may be caused by a filling error: In
this case repeat the measurement. Or your sample
is inhomogeneous: In this case deactivate checking
for density stability (and set a hold time).
6.3.6 FillingCheck™
FillingCheck™ is an automatic bubble detection
based on an advanced analysis of the U-tube’s
oscillation pattern.
If applicable, a filling warning will be shown in the
measurement information widget on the dashboard.
TIP:
Additionally check the filling visually by means
of the built-in live camera (U-View™).
TIP:
“Yes” is the standard setting. Select “No” if the
detection of filling errors by FillingCheck™ obviously
contradicts what you see in the live camera image.
TIP:
FillingCheck™ provides excellent support to
the operator for samples of low and medium viscos-
ity ranges.
The sensitivity of this feature depends on a combi-
nation of density, viscosity, and temperature, and is
not constant. For example, certain samples with
high density (approx. 1.5 g/cm
3
) and medium vis-
cosity (approx. 550 mPa·s) might generate a filling
warning also for correctly filled samples. In all such
cases, changing the measuring temperature may
influence this combination so that FillingCheck™
continues working as expected.
Some samples may generate a filling warning even
when filled without bubbles, e.g. highly viscous sam-
ples or samples containing inhomogeneities. In
these cases we recommend to disable
FillingCheck
™ and perform repeated measure-
ments to validate the quality of filling.
6.3.7 Other Measurement Parameters
Other measurement parameters may be available
with installed options. For details see the respective
manual of the option.
Example:
The measurement perfor-
mance Precise has been set (white
squares). Currently the measurement
reaches measurement performance
Standard (green squares).
1
Only available for measurement performance Precise.
Yes
The measurement result is determined
when the temperature value as well as the
density value are stable.
No
The measurement result is determined
when the temperature value is stable.
Indicator Measurement performance
Yes
FillingCheck™ is active.
No
FillingCheck™ is deactivated.