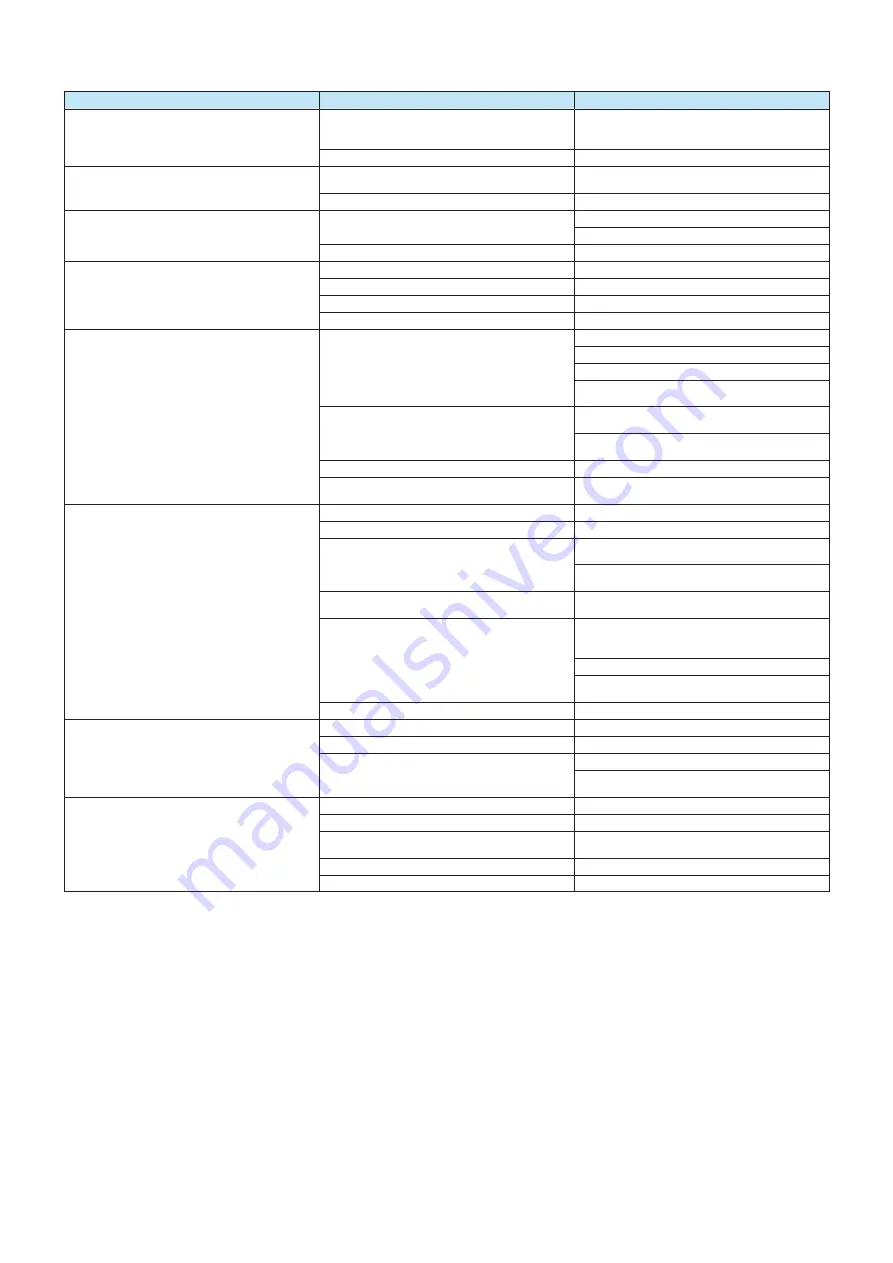
Use
26
ANY ANOMALIES AND REMEDIES
ANOMALY
CAUSE
REMEDY
Safety valve(s) opening
Exceeding of the max pressure regulated on the
valve that must be equal to the appliance design
pressure
Adjustment of block pressure switches and/or limit
too high
Safety valve calibration loss
The valve manufacturer will perform the overhaul
Small leak from the safety valve(s) (leakage)
Dirt around the shutter seat
Cleaning of seat by sometimes acting on the
manual opening lever
Scratched shutter seat
The valve manufacturer will perform the overhaul
Pump block
Disconnected pump thermal relay
Check motor absorption
Check thermal calibration
Blocked pump shaft
Electric pump maintenance
Block pressure switch intervention
Calibrated limit pressure switch too high
Limit pressure switch calibration
Faulty limit pressure switch
Limit pressure switch replacement
Clogged pressure switch coil
Coil cleaning or replacement
Block pressure switch failure
Pressure switch replacement
Level 1 or 2 safety intervention
Interrupted water level detection
Encrusted stainless steel rod
Interrupted connection cable
Check the conductivity of the water
Check the pump on-off trimmer calibration on the
RR relay
Faulty safety level relay
Temporary replacement of electronic safety relay
with one of the two relays in the panel
If the problem is solved, permanently replace the
faulty relay.
Lack of water filling
See "Loading" Problems
Incorrect electrical panel probe power supply
electrical cable wiring
Wiring diagram check
Insufficient water loading
Pump block
See "Pump block" Problems
Dirty pump intake filter
Filter cleaning
Level adjustment anomaly
Temporary replacement of electronic adjustment
relay with one of the two relays in the panel.
If the problem is solved, permanently replace the
faulty relay.
Level adjustment probes short-circuit
Disassemble the adjustment probes to visually
check the ceramic insulation
Pump cavitation
Head (=height difference between the collection
vessel level and the pump) insufficient in relation to
the water temperature
Pump intake filter cleaning
Reduce resistance of the duct between collection
vessel and pump by increasing the passage section
Pump rotation direction
Invert one of the phases (three-phase pump)
Burner always on
Incorrect connection to the electrical panel
See the wiring diagram
Faulty level safety relays
See "Level 1 or 2 safety intervention"
Block and/or adjustment pressure switches not
active
Pressure switches calibration check
Check of pressure switch connections to the
electrical panel
Burner always off
Burner problems
See specific Burner manual
Burner fuses interrupted
Fuses replacement
No consent to burner from adjustment pressure
switch
Adjustment pressure switch replacement
No consent to burner from level safety relays
See "Level 1 or 2 safety intervention"
Incorrect connection to the electrical panel
See the wiring diagram
Cooke Industries - Phone: +64 9 579 2185 Email: [email protected] Web: www.cookeindustries.co.nz