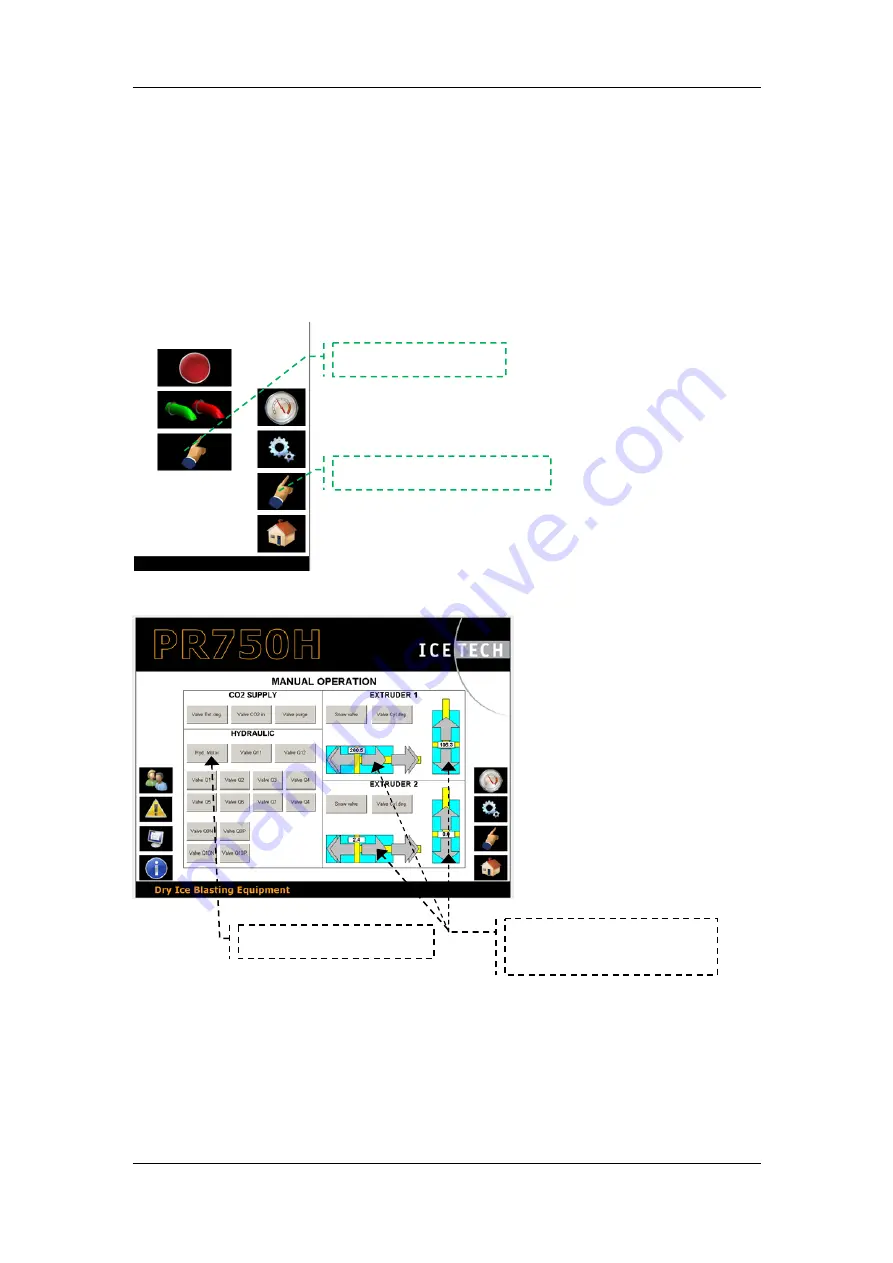
Procedures for maintenance and repair
www.icetechworld.com | IceTech Dry Ice Technology |
Rev 1
Page 54
Procedure no. 12 Changing Air filter.
BEFORE STARTING PRODUCTION THE HYDRAULIC STATION SHOULD
BE CHECKED IN SINGLE MODE!
Operating in single mode control
Check that there are no leaks on the hydraulic station.
The operation is complete.
1
Select
single
mode
2
Enter
Manual
operation
3
Start
the
hyd.
pump
4
Move
the
pistons
using
the
arrow
buttons
Summary of Contents for PR350H
Page 1: ...User s Manual Technical file 1 2 User s manual PR350H...
Page 2: ...User s Manual 1 User s manual PR350H...
Page 24: ...Technical file 2 User s manual PR350H...
Page 26: ...Table for mechanical maintenance 1 Technical file PR350H...
Page 29: ...Procedures for maintenance and repair 2 Technical file PR350H...
Page 89: ...Alarm list 3 Technical file PR350H...
Page 93: ......
Page 113: ...P I Diagram 4 Technical file PR350H...
Page 117: ...Assembly drawings 5 Technical file PR350H...
Page 130: ...Installation layout drawings 6 Technical file PR350H...
Page 134: ...Page 4 of 5 16 10 2012 Rev 2 PJ BN...
Page 138: ...Wiring diagram 7 Technical file PR350H...
Page 140: ...Holtec Automatic A S Index...
Page 147: ...Holtec Automatic A S EC Declaration of Conformity...
Page 149: ...Holtec Automatic A S Maintenance...
Page 152: ...Holtec Automatic A S Project Info...
Page 158: ...Holtec Automatic A S Power Circuit Diagrams...
Page 160: ...Holtec Automatic A S Control Voltage...
Page 162: ...Holtec Automatic A S Motor Circuits...
Page 164: ...Holtec Automatic A S Safety Circuit Diagrams...
Page 166: ...Holtec Automatic A S PLC Reference...
Page 172: ...Holtec Automatic A S Touchpanel Modem...
Page 174: ...Holtec Automatic A S PLC I O...
Page 177: ...Holtec Automatic A S PLC Digital Output...
Page 180: ...Holtec Automatic A S PLC Output 24VDC Solenoids...
Page 184: ...Holtec Automatic A S PLC Output 230VAC Solenoids...
Page 187: ...Holtec Automatic A S PLC RTD Input...
Page 189: ...Holtec Automatic A S PLC Analog Input...
Page 193: ...Holtec Automatic A S Cableplan...
Page 206: ...Holtec Automatic A S Bill of Components...
Page 212: ...Datasheets 8 Technical file PR350H...
Page 221: ...Accessories 9 Technical file PR350H...
Page 222: ......
Page 223: ......