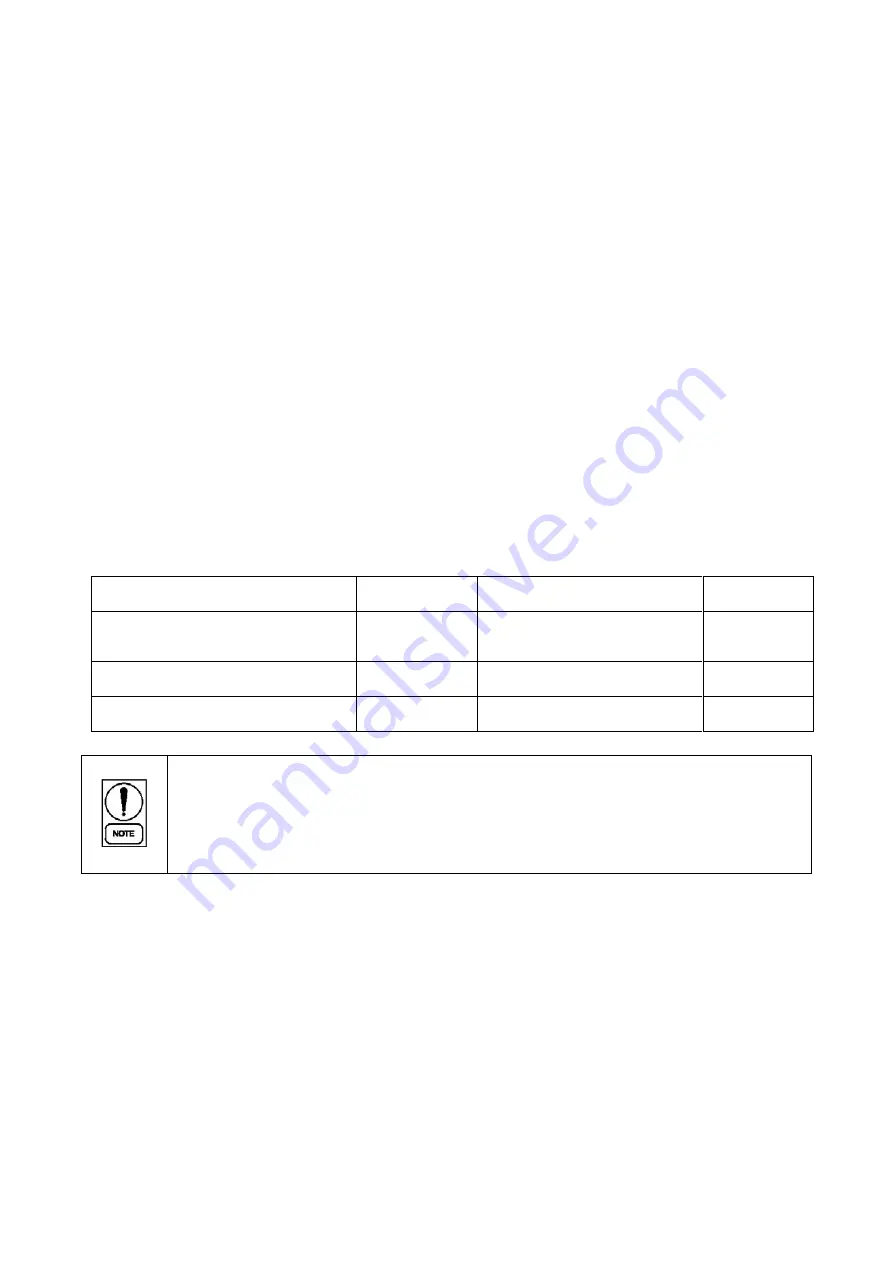
2
To avoid injury or damages to the units, please observe these notes:
•
The supply power wiring must be selected according to the maximum overcurrent protection (MOCP) or
maximum power.
•
Power must be ground in accordance with the National Electrical Code.
•
Confirm the fastening of power wiring prior to start-up
•
Connect the supply wiring in accordance with the wiring diagram.
•
Installation professionals are advised to wear protective gear, such as anti-static gloves during electrical
operations, etc.
•
Check the parts, integrity, and insulation of wiring, and repair if needed.
•
This unit is intended to operate within the ranges specified.
•
It is strictly prohibited to refit the unit or modify the parameters.
Water system installation
•
Isolation valves and drains shall be installed at the inlet and outlet of the water pipes; strainers are
recommended on the inlet piping.
•
Gauges and thermometers are recommended to be installed on the inlet and outlet pipes to monitor the
operation of the system and equipment.
•
The temperature difference of water inlet and outlet are suitable between 7°F (4
℃
) and 11°F (6
℃
) when
operating at full load.
•
The water quality should meet the requirement below
:
pH value
(
25
℃
)
6.5 − 8.0
Chloridion
(
Cl
(
mg/L
)
<
50
Electrical conductivity
(
25
℃
)
(
μs/cm)
<
250
Silver sulfate
(
SO4
2
−
)
(
mg/
)
<
50
TFe
(
mg/L
)
<
0.3
Total alkalinity
<
50
Total hardness
(
mg/L
)
<
50
Silicon dioxide
(
SiO2
)
<
30
Compressor shipping brackets are mounted to the bottom of the compressors to prevent the
vibration isolation mounts from damage during shipment. REMOVE the compressor shipping
brackets prior to start-up.
Warning
•
Prior to start-up, the compressor should be powered on to preheat the system. Recommended preheat
cycle is 8 hours prior to initial start-up. Completing the recommended preheat improves the temperature of
the compressor lubricating oil. Failing to properly preheat the system can result in poor operation or damage
to the compressor
.
•
CFC’s can destroy the ozone layer in the atmosphere and pollute the environment. Utilize recovery devices
to recover refrigerant when servicing the system.
•
If the operation of this system has the potential for power loss and has the potential to experience ambient
temperatures below freezing [32°F (0°C)], then the user should utilize one of three strategies: A) Order the
unit with factory mounted heat trace, then provide field heat trace on external piping and an emergency
power source for the heat trace, or B) Utilize glycol (anti-freeze) solution within all external hydronic piping.
Summary of Contents for ccHPWH Series
Page 11: ...8 III Product specification 1 Dimensions Unit inch ccHPWH275 S ccHPWH275 D ...
Page 12: ...9 ccHPWH550 S ccHPWH550 D ...
Page 26: ...23 2 Wiring diagram ccHPWH275 S ccHPWH275 D ...
Page 27: ...24 ccHPWH550 S ccHPWH550 D ...
Page 42: ...39 Schematic diagram of control wiring and code dialing of each module ...