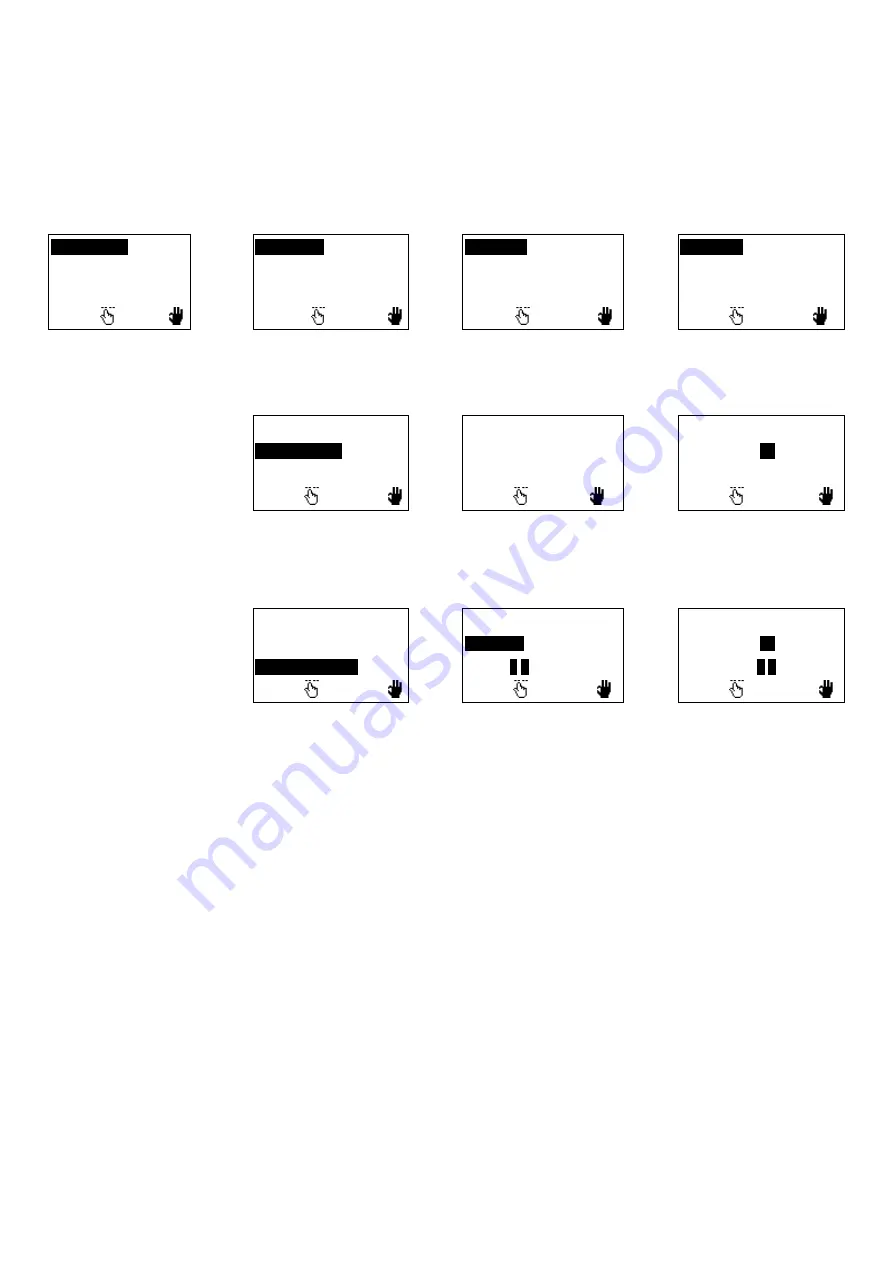
29
3.5. Timing set
Press <Down> or <Up> to select timing set.
【
3
】
↑
>1 timing set
▲
>2 status inquiry
>3 clock inquiry
▼
Return
Enter
<enter>
———→
←———
<function>
1 timing set
: disabled
Primary timing
01 group timing ▼
Return
Set
Error!
Timing set
: disabled
Primary timing
01group timing ▼
Cancel
Enter
Error!
Timing set
: disabled
Primary timing
01group timing ▼
Return
Set
<d
o
wn>
——
—
→
↓
【
1
】
↓
【
2
】
【
4
】
↑
Timing set: disabled ▲
Primary timing
01group timing
▼
Return
Set
<enter>
———→
Primary timing
Timing off
21:00
Return
Switch
<enter>
———→
Primary timing
Timing off
21
:00
Return
Switch
<d
o
wn>
——
—
→
【
5
】
↑
Timing set: disabled ▲
Primary timing
01group timing
▼
Return
Set
<enter>
———→
01 group timing
Timing off
21:00
1 2 3 4
5
6
7
Return
Switch
<enter>
———→
01 group timing
Timing off
21
:00
1 2 3 4
5
6
7
Return
Switch
Description:
【
1
】
Press <Function> key to return to menu of previous level.
【
2
】
Press <Function> key to changed timing value.
【
3
】
Indicates the selection of the timing setting.
【
4
】
Indicates the selection of primary timing.
【
5
】
Indicates to select 01 group timing. Press <Up> or <Down> to switch among use of timing, primary
timing and setting from 01 group to 10# group. After entering the selected timing item, press <Enter>
key to change the set timing On/Off, Hour and Minute, Week (1, 2···7; when week is selected, the
corresponding will flash). Press <Up> or <Down> key to change the selected value. Inverse display
of week (1, 2···7) indicates that timing is effective on the day. As shown in the figure above, shutdown
will be performed at 21:00 on Friday and Saturday.
Note: If the timing is set to 00:00, it indicates the function is not used.
Summary of Contents for ccHPWH Series
Page 11: ...8 III Product specification 1 Dimensions Unit inch ccHPWH275 S ccHPWH275 D ...
Page 12: ...9 ccHPWH550 S ccHPWH550 D ...
Page 26: ...23 2 Wiring diagram ccHPWH275 S ccHPWH275 D ...
Page 27: ...24 ccHPWH550 S ccHPWH550 D ...
Page 42: ...39 Schematic diagram of control wiring and code dialing of each module ...