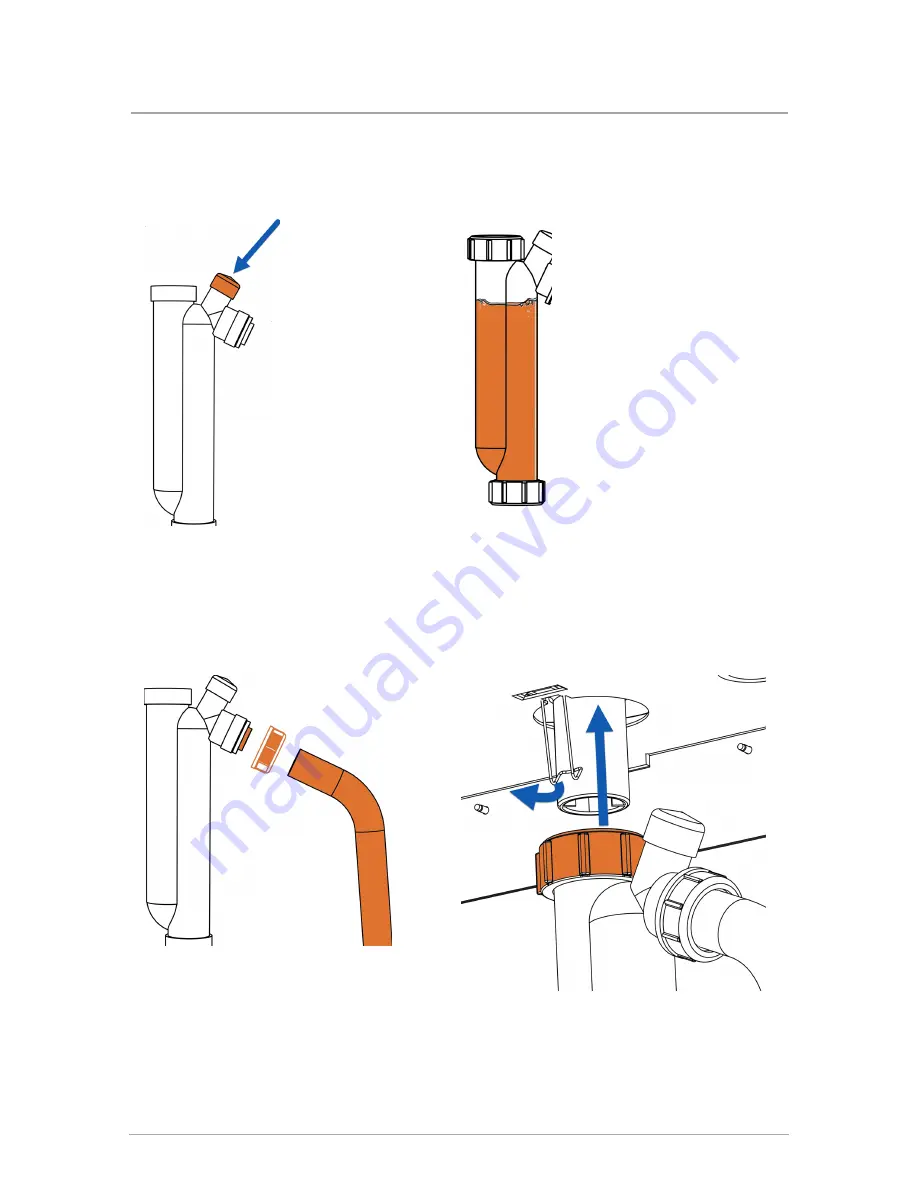
1.
Place the vacuum breaker cap over the
vacuum breaker opening and push
firmly.
2.
Fill the condensate trap with water.
3.
Attach the drain hose and tighten the
drain compression nut (including
washer).
4.
Slide the trap over the boiler drain
outlet, and tighten upper union nut.
44
Section: Installation
Summary of Contents for CX Series
Page 10: ...Intentionally left empty...
Page 70: ...Intentionally left empty...
Page 84: ...Intentionally left empty...
Page 102: ...Intentionally left empty...
Page 114: ...Appendices Wiring diagrams Figure 48 Controller electrical diagram 114 Section Troubleshooting...
Page 115: ...Figure 49 Internal wiring diagram 115 Wiring diagrams...
Page 116: ...Figure 50 Sequence of Operation 116 Section Troubleshooting...