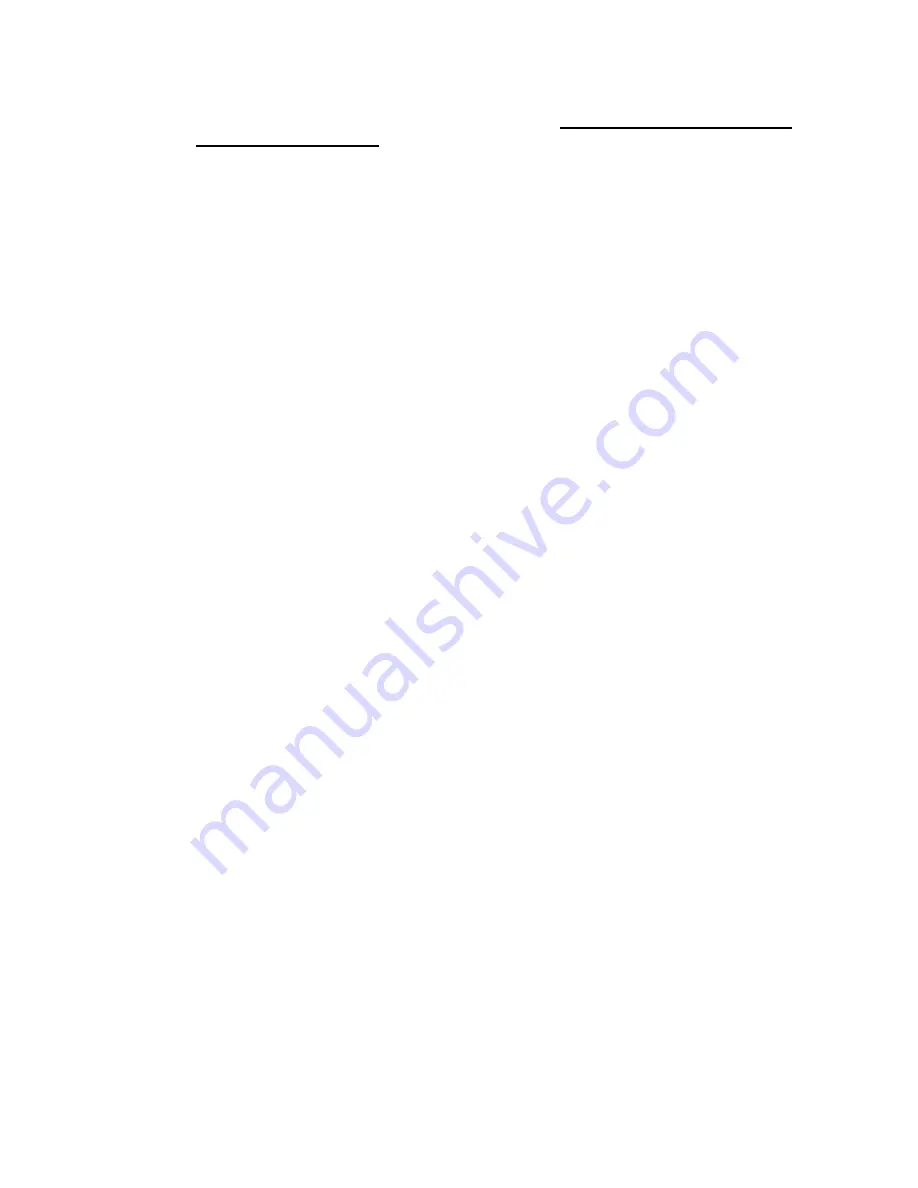
IBC Technologies Inc.
36
VFC 15-150 and VFC 45-225
3.1
PRIOR TO START-UP
a)
Ensure venting system is complete
and seal tested. Confirm any
common venting system at the
installation site is isolated and
independent of the VFC boiler, that
any holes left from removal of a
previous boiler have been sealed,
and that any resizing of the old flue
has been done. Fill condensation
trap to full 7” (min) neck height for
VFC 15-150 or 28” for VFC 45-
225.
b)
Check water piping system is fully
flushed and charged, and that all
air has been discharged through
loosened bleed caps. Note it is
possible to switch all pumps on/off
from the keypad – without a call
for heat. This greatly simplifies
system filling and air bleeding (go
to
Installer Setup
, drop down to
Pump Purge
and toggle to
On
.
When complete, return to
Off
, or
this will automatically occur with a
call for heat). Use a minimum
water pressure of 12 psig. And
confirm pressure relief valve is
installed and safely drained.
c)
Perform a final check of electrical
wiring.
3.1.1 Test Ignition Safety Shutoff
With the boiler in operation, test the
ignition system safety shutoff device by
shutting the manual gas valve immediately
outside the boiler case. Ensure boiler has
shut off and the appropriate Error
information is displayed on the LCD
screen. To restart boiler, reset power.
3.2
GAS VALVE ADJUSTMENT
The VFC modulating boilers are factory
calibrated to operate with natural gas (or
propane if so ordered) at sea level. The
relevant valve adjustment screws have
been factory sealed using Loctite thread-
lock compound, which can be broken
where required. However,
no mixture
adjustment shall be performed unless
done by a qualified technician using
properly functioning combustion
analyzing equipment.
Upon initial set up, the installer can
enter the site elevation to compensate
for altitude.
Without such intervention,
the gas valve will automatically de-rate the
maximum input in accordance with the
density altitude, at approximately 2% per
1,000' above sea level. The gas valve's
zero govenor will ensure that the gas:air
mixture is not affected at altitude.
To verify the proper operation of the gas
valve in the field, the following procedure
can be carried out by a qualified technican
(refer to Figure 12):
1.
with a small (1/8" or 3 mm) flat
screwdriver, open the manifold
pressure test port by turning its centre-
screw 1 full turn counterclockwise.
Attach a manometer between the
manifold pressure test port and the
reference line.
2.
Allow the boiler to ignite / run against
a large load, to maintain high fire
3.
With the boiler at maximum output,
use a 2 mm hex key to adjust the zero-
offset (see Fig.12, #9) as required to
achieve 0" wc. This adjustment is
only necessary if this screw has been
tampered with.
4.
With a combustion analyzer probe in
the flue gas, turn the Gas:Air Ratio
Adjustment screw (Fig.12, #11) to