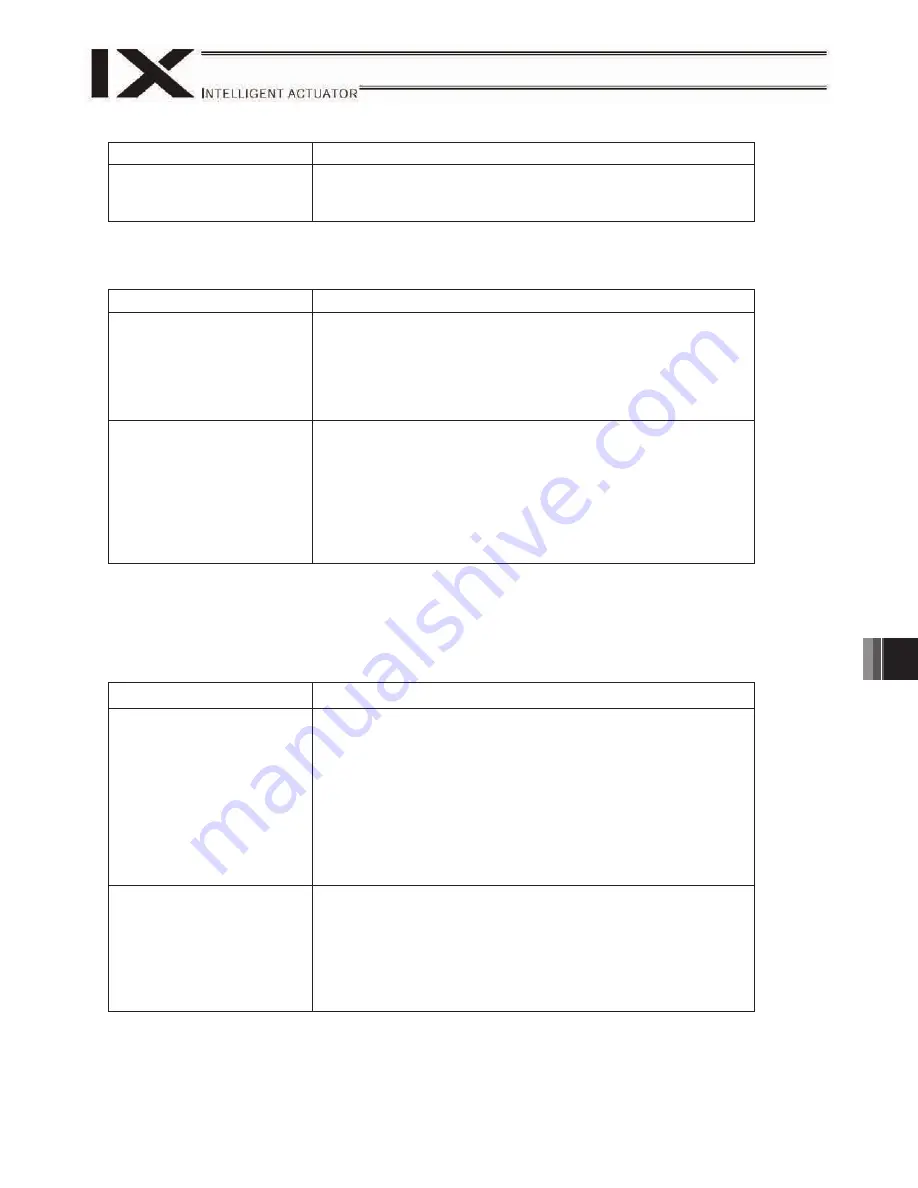
69
13. Maintenance and Inspection
[3] Yearly Maintenance Inspection
Have a maintenance and inspection for the following items every year.
Maintenance Inspection Area
Maintenance Inspection Details
Robot Main Body
Arm Attachment Bolts
Check for any looseness of the bolts on the arm.
(If any play is found on the arm attachment, tighten up the bolts.)
[Refer to 13.3, “Check for Looseness of Arm Attachment Bolts”.]
[4] 2.5 Years Maintenance Inspection
Have a maintenance and inspection for the following items once every 2.5 years.
If the robot main body has flaws or other abnormalities, please contact IAI.
Maintenance Inspection Area
Maintenance Inspection Details
Battery Replacement
Replace the absolute data backup battery.
The battery life may vary depending on the condition and
environment of the robot use, but it is approximately three years.
It is recommended to have the battery replaced every 2.5 years.
(Battery model code: AB-6, Quantity to use: 4 units)
[Refer to 13.4, “Replacement of Absolute Backup Battery”.]
Third Axis Belt
Check the third axis (vertical axis) timing belt surface for any
defect or excessive wear.
(Check it five years later from the operation start, and after that,
check it every year).
When any defect is found, the replacement of the timing belt is
required.
(If any defect is found, contact IAI).
[Refer to 13.5, “Third Axis Timing Belt Visual Check”.]
Note 1: In case the duty of the robot operation is high, or ambient temperature is high, supply the
grease frequently (every year).
[5] 5 Years Maintenance Inspection
Have a maintenance and inspection for the following items once every 5 years.
After 5 years has passed, have a maintenance and inspection for the following items every year.
If the robot main body has flaws or other abnormalities, please contact IAI.
Maintenance Inspection Area
Maintenance Inspection Details
First axis and Second axis
speed reducer
Bearings on joints
Lost motion measurement
If the lost motion value exceeds the allowable range, it is
considered the end of life for speed reducer or bearing. It is
necessary to have the unit disassembled for such work as
replacement of the speed reducer.
(Please contact IAI if any abnormality is found.)
(Note) The life of the speed reducer may vary depending on the
duration of operation, speed or load, but it is approximately
five to seven years.
[Refer to 13.6, “How to Measure Lost Motion”.]
Forth Axis Belt
Check the forth axis (rotational axis) timing belt surface for any
defect or excessive wear.
(Check it five years later from the operation start, and after that,
check it every year).
When any defect is found, the replacement of the timing belt is
required.
[Refer to 13.7, “Forth Axis Timing Belt Visual Check”.]
Summary of Contents for IX Series
Page 2: ......
Page 4: ......
Page 56: ...50 9 How to Install ...
Page 58: ...52 9 How to Install Center of recommended installation part ...
Page 104: ......
Page 105: ......