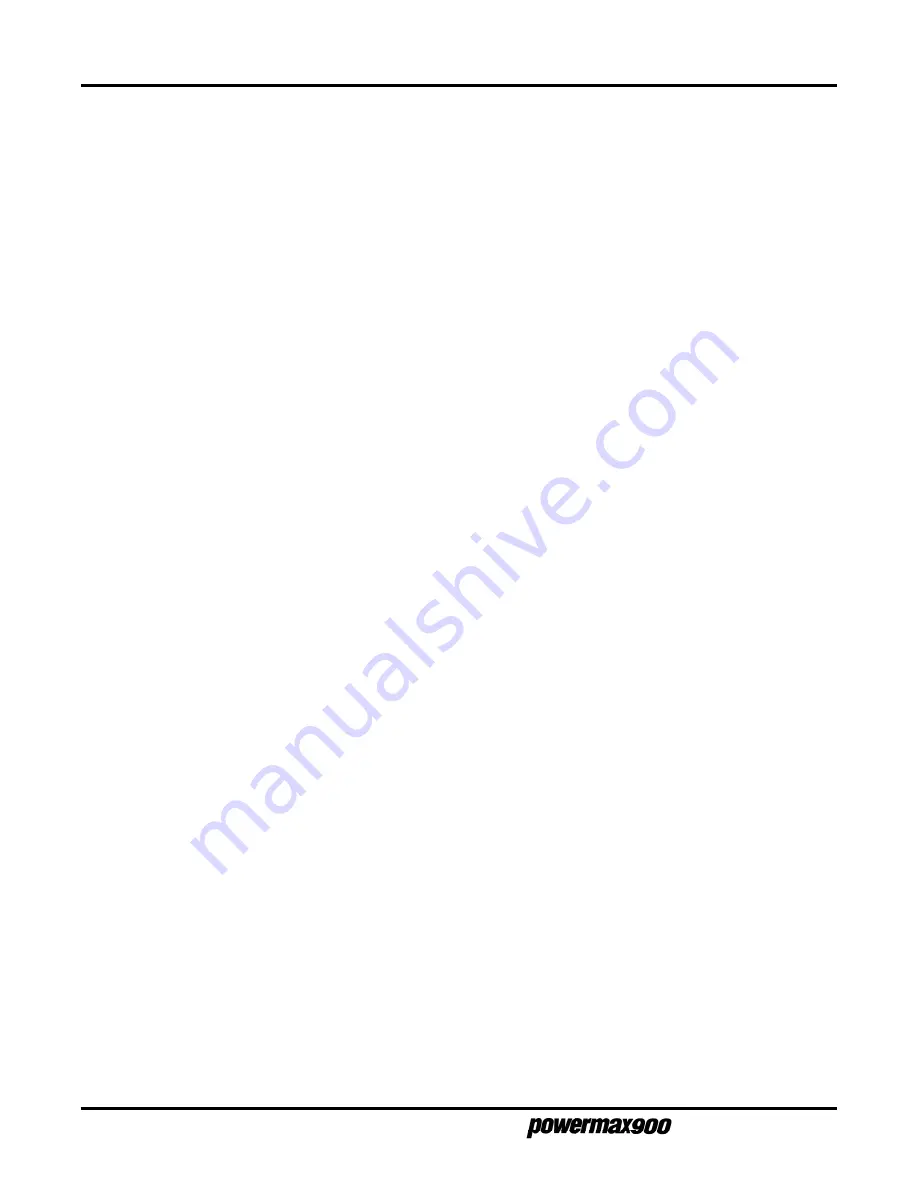
4-14
O
PERATION
Operator Manual
Cut Chart Notes (continued):
•
Maximum recommended mechanized cutting capacity: 1/2" (13 mm).
•
See page 4-7 or
Section 5
for additional consumable parts.
•
Compressed air or nitrogen must be available to the power supply filter/pressure regulator at a
flow rate of 360 scfh/6 scfm (170 l/min) at a pressure of 90 psi (6.2 bar). The dynamic (flowing)
pressure when operating is 70 psi (4.8 bar). If torch leads are 50 ft (15.2 m), the dynamic
pressure when operating is 75 psi (5 bar). If the pressure to the power supply falls below 40 psi
(2.8 bar), the torch will go out.
•
After several minutes of running, the torch retaining cap may become hot to touch. To cool it,
push in and hold the GAS TEST switch until the cap cools down.
•
The duty cycle, or the amount of time the pilot or plasma arc can remain “on” in minutes within a
10-minute period, is affected by many factors. When the current is set at 55 amps, the
Powermax900 has a 50% duty cycle at a temperature of 40
°
C (104
°
F). At these conditions,
the plasma arc can remain on 5 minutes out of every 10 minutes without causing the tempera-
ture sensors to disable the unit. The duty cycle increases to 100% at a temperature of 40
°
C
(104
°
F) when the current is set below 39 amps.
•
To avoid performance deterioration of the Powermax900, input voltage should be within 10% of
the specified system line voltage setting.
COMMON CUTTING FAULTS
•
The workpiece is not totally penetrated. Causes can be:
-
The current is too low.
-
The cut speed is too high.
-
The torch parts are worn.
-
The metal being cut is too thick.
-
The work clamp is not properly attached to the workpiece.
•
Dross forms on the bottom of the cut. Causes can be:
-
The cutting speed is too slow.
-
The torch parts are worn.
-
The metal being cut is too thick.
-
The current is too low.
Summary of Contents for powermax900
Page 1: ......
Page 15: ...SAFETY 1 6 Hypertherm Plasma Systems 8 99 ...
Page 21: ...SÉCURITÉ 1a 6 08 99 HYPERTHERM Systèmes plasma ...
Page 50: ...OPERATION 4 9 Operator Manual Figure 4 8 Dragging the Torch Figure 4 7 Cutting a Circle ...
Page 69: ...Operator Manual 5 14 MAINTENANCE PARTS ...
Page 73: ...APPENDIX B Operator Manual ...