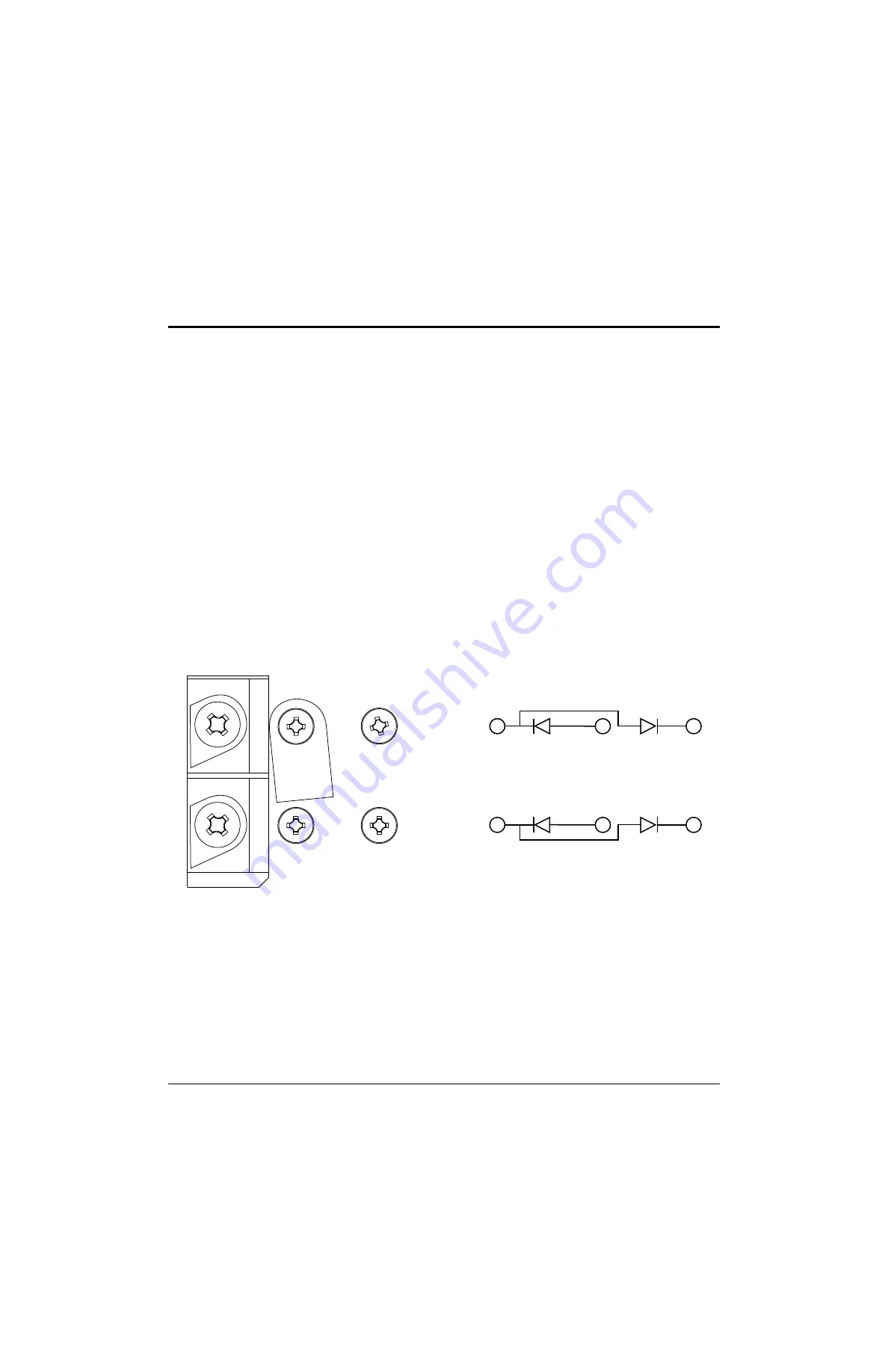
Do System Tests to Identify Defective Components
5
90
810430
Troubleshooting Guide
Powermax65/85/105 SYNC
Test 3 – Output diodes
Do this test if you get the
3-51-1
or
3-52-0
fault code.
1.
Set the power switch on the plasma power supply to OFF (
O
), and disconnect the power cord.
2.
Remove the plasma power supply cover and the component barrier.
3.
Put a multimeter in ohmmeter (resistance) mode or diode test mode, and measure the
resistance on all 4 diodes in the bridge. For each diode, put the black (common) lead on 3.
Refer to
. A diode that is operating correctly gives the following values:
The value is open (very high resistance) with the meter leads in one direction.
The value is within the range of 0.1 V – 1.0 V with the meter leads in the opposite direction.
4.
If a diode has one of the following conditions, replace both output diode bridges. Always
replace output diodes as a pair.
The diode has a value less than 0.1 V. In this condition, the diode is short-circuited.
The diode has a value greater than 1.0 V in both directions. In this condition, the diode has
an open circuit.
Figure 16
– Output diode connections on the power PCB
3
2
1
3
2
1
3
2
1
3
2
1
Summary of Contents for Powermax105
Page 1: ...Powermax65 85 105 SYNC Troubleshooting Guide 810430 REVISION 0 ENGLISH ...
Page 12: ...Before You Begin 1 12 810430 Troubleshooting Guide Powermax65 85 105 SYNC ...
Page 174: ...System Diagrams 8 174 810430 Troubleshooting Guide Powermax65 85 105 SYNC ...
Page 180: ...System Diagrams 8 180 810430 Troubleshooting Guide Powermax65 85 105 SYNC ...