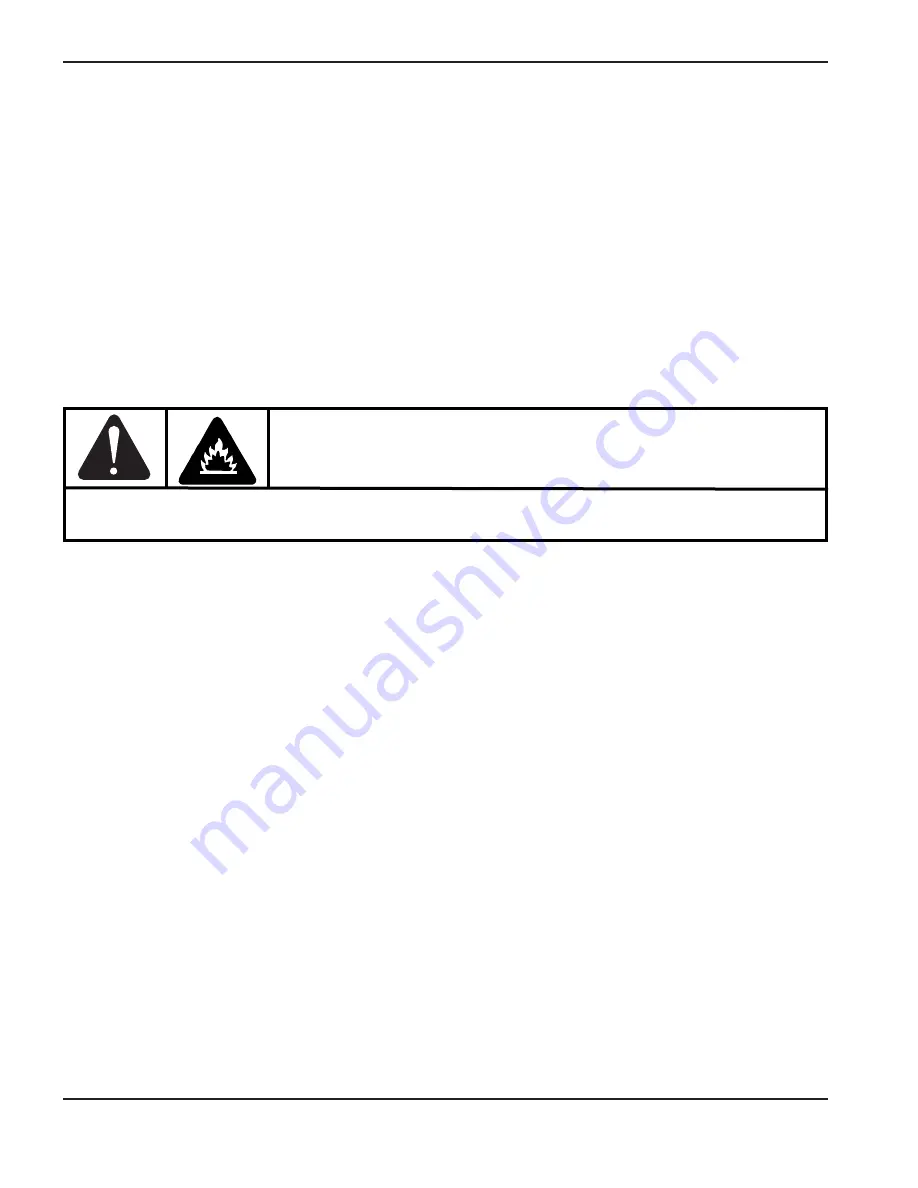
5-2
PAC500
Instruction Manual
4
MAINTENANCE
Routine Maintenance
Protecting Copper Surfaces
To protect copper surfaces in the injection water/torch coolant open loop, do the following twice a year:
1. Mix a 16 ounce container of corrosion inhibitor benzotriazole (128020) in the water chiller's 45 gallon water
reservoir.
2. Turn on the water chiller and run the pump for 2 hours. Do not start the power supply or attempt to cut with the
torch while recirculating the solution.
3. Turn water chiller off and leave power supply off for 8 hours.
4. Resume normal operating procedures.
Normal wear and tear on the nozzle, electrode and swirl ring limit the life of these parts, making replacement
necessary. Replace the nozzle when the water spray cone becomes irregular and cleaning of its water flow
passages does not correct the problem.
Nozzle
1. Place the 3Ø power ON/OFF switch on the cutting machine operator's panel to OFF.
2. Unscrew the retaining cap and remove the nozzle by hand.
3. Before replacing the nozzle, apply a light coat of silicone grease to the O-ring that is on the O.D. of the copper
portion of the nozzle.
4. Insert the nozzle into the torch and push into place.
5. When replacing the retaining cap, tighten snugly by hand to insure good electrical contact between the nozzle
and the torch. If the cap does not go on easily, clean threads and apply a small amount of silicone grease to the
O-ring located just below the threads of the torch body.
Note:
Failure to tighten the retaining cap snugly will result in pitting of the stainless steel nozzle seat (current ring)
of the torch and subsequent gas and water leaks around the upper nozzle O-ring which will impair cut
quality. However, tighten the retaining cap by hand only. Pitting will never occur if proper care is taken
as outlined above. See Torch on next page.
WARNING
Always disconnect the power supply from the main power source before inspecting or changing the
torch parts.
Summary of Contents for PAC500
Page 1: ...Water Injection Plasma Cutting System Instruction Manual 800370 Revision 4 PAC500 ...
Page 53: ...5 12 PAC500 Instruction Manual 4 MAINTENANCE Figure 1 PAC500 Schematic Layout ...
Page 56: ...PAC500 Instruction Manual 5 15 4 MAINTENANCE Figure 4 Direction of Cut Figure 5 Cut Angle ...
Page 60: ...PAC500 Instruction Manual 5 19 4 MAINTENANCE Figure 9 Plasma Console Electrical Schematic ...
Page 63: ...6 2 PAC500 Instruction Manual 4 PARTS LIST Model 500 Torch 1 2 3 4 3 6 7 5 3 ...
Page 65: ...6 4 PAC500 Instruction Manual 4 PARTS LIST Torch Leads ...
Page 69: ...6 8 PAC500 Instruction Manual 4 PARTS LIST Remote Stop Start 6 3 2 1 4 5 ...
Page 71: ...6 10 PAC500 Instruction Manual 4 PARTS LIST Argon Hydrogen Manifold 14 ...
Page 73: ...6 12 PAC500 Instruction Manual 4 PARTS LIST 1 Torch Operator s Panel ...
Page 75: ...6 14 PAC500 Instruction Manual 4 PARTS LIST 2 Torch Operator s Panel ...
Page 81: ...6 20 PAC500 Instruction Manual 4 PARTS LIST Plumbing Compartment PAC500 Console ...
Page 82: ...PAC500 Instruction Manual 6 21 4 PARTS LIST Plumbing Compartment with Kobold Flow Switches ...
Page 88: ...a 2 PAC500 Instruction Manual 4 ...
Page 89: ...PAC500 Instruction Manual a 3 4 ...
Page 90: ...a 4 PAC500 Instruction Manual 4 ...
Page 91: ...PAC500 Instruction Manual a 5 4 ...
Page 93: ...PAC500 Instruction Manual a 7 4 ...
Page 94: ...a 8 PAC500 Instruction Manual 4 ...