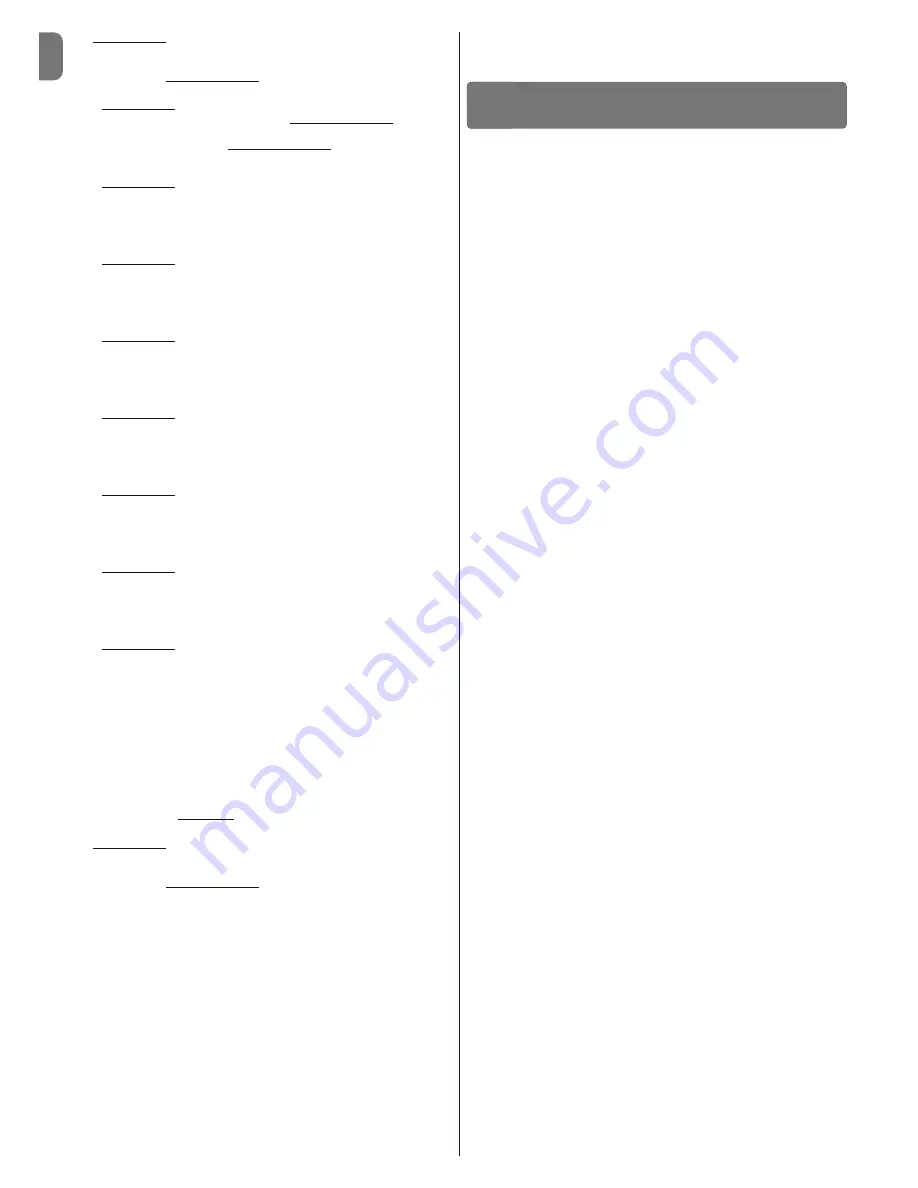
EN
6
– English
01.
Press and hold keys “
Set
” and “
” at the same time.
02.
Release the keys when led “
L1
” starts flashing (after approx. 1 second);
Note
– After 3 seconds have elapsed, if the keys
“
Set
” and “
”
are not
released, the “automatic learning” procedure is started up, and not the
manual procedure.
03.
• LED
L1
flashes:
position 0 of M1
To bring motor 1 to
position 0
(
fig. C
): press and hold down the
or
keys. On reaching the position, release the key to stop the manoeuvre.
To memorise the position, press and hold down the “
Set
” key for at least
3 seconds and then release it (after 2 seconds LED L1 remains on and on
releasing the “Set” key LED L2 begins flashing).
• LED
L2
flashes:
position 0 of M2
To bring motor 2 to
position 0
(
fig. C
): press and hold down the
or
keys. On reaching the position, release the key to stop the manoeuvre.
To memorise the position, press and hold down the “
Set
” key for at least
3 seconds and then release it (after 2 seconds LED L2 remains on and on
releasing the “Set” key LED L3 begins flashing).
• LED
L3
flashes:
position SA of M2
To bring motor 2 to
position SA
(
fig. C
): press and hold down the
or
keys. On reaching the position, release the key to stop the manoeuvre.
To memorise the position, press and hold down the “
Set
” key for at least
3 seconds and then release it (after 2 seconds LED L3 remains on and on
releasing the “Set” key LED L4 begins flashing).
• LED
L4
flashes:
position A of M1
To bring motor 1 to
position A
(
fig. C
): press and hold down the
or
keys. On reaching the position, release the key to stop the manoeuvre.
To memorise the position, press and hold down the “
Set
” key for at least
3 seconds and then release it (after 2 seconds LED L4 remains on and on
releasing the “Set” key LED L5 begins flashing).
• LED
L5
flashes:
position A of M2
To bring motor 2 to
position A
(
fig. C
): press and hold down the
or
keys. On reaching the position, release the key to stop the manoeuvre.
To memorise the position, press and hold down the “
Set
” key for at least
3 seconds and then release it (after 2 seconds LED L5 remains on and on
releasing the “Set” key LED L6 begins flashing).
• LED
L6
flashes:
position SC of M1
To bring motor 1 to
position SA
(
fig. C
): press and hold down the
or
keys. On reaching the position, release the key to stop the manoeuvre.
To memorise the position, press and hold down the “
Set
” key for at least
3 seconds and then release it (after 2 seconds LED L6 remains on and on
releasing the “Set” key LED L7 begins flashing).
• LED
L7
flashes:
position 1 of M1
To bring motor 1 to
position 1
(
fig. C
): press and hold down the
or
keys. On reaching the position, release the key to stop the manoeuvre.
To memorise the position, press and hold down the “
Set
” key for at least
3 seconds and then release it (after 2 seconds LED L7 remains on and on
releasing the “Set” key LED L8 begins flashing).
• LED
L8
flashes:
position 1 of M2
To bring motor 2 to
position 1
(
fig. C
): press and hold down the
or
keys. On reaching the position, release the key to stop the manoeuvre.
To memorise the position, press and hold down the “
Set
” key for at least
3 seconds and then release it to exit programming (after 2 seconds LED
L8 remains on until the “Set” key is released).
Note –
To perform manual programming in a system with a single gear-
motor
, proceed as described in paragraph 4.7.2 and at
step 03
program posi-
tions “
0
” and then “
1
” of M1, ignoring the part related to keys “
” and “
”, and
using the “
Set
” key only, as described.
Important!
– In the manual proce-
dure, positions “SA” of M2; “A” of M1; “SC” of M1 must not be pro-
grammed.
4.7.3 - Learning in combined mode
Perform this procedure after completing the automatic learning cycle:
01.
Press and hold keys “
Set
” and “
” at the same time.
02.
Release the keys when led “
L1
” starts flashing (after approx. 1 second);
Note
– After 3 seconds have elapsed, if the keys
“
Set
” and “
”
are not
released, the “automatic learning” procedure is started up, and not the
manual procedure.
03.
Briefly press key “
” or “
” to move the flashing led (L1-L8) to the position
to be programmed and proceed for each position, as described in step 03
of the manual learning procedure (paragraph 4.7.2).
Repeat this operation for all other positions to be modified.
To complete the manual learning process, press key “
” repeatedly to move
the led that flashing beyond position L8.
4.8 - Checking movement of gate leafs
At the end of the learning procedure, it is advisable to make the control unit per-
form a few opening and closing manoeuvres to ensure that the gate moves cor-
rectly and to check for installation or setting defects.
01.
Press the “
Open
” key. Check for the correct leaf opening offset and check
that the opening manoeuvre includes the acceleration, constant speed
and deceleration phases and that the leaf limit switch is set a few centime-
tres from the opening mechanical stops.
02.
Press the “
Close
” key and check that the closure manoeuvre includes the
acceleration, constant speed and deceleration phases. Check that the leaf
closure offset is correct. At the end of the manoeuvre, the leafs must be
perfectly closed on the mechanical closure stop.
These are the most important phases in the installation of the automation sys-
tem, in order to guarantee maximum system safety. Testing can also be used to
check the devices in the automation system regularly. The automation system
testing and commissioning phases must be carried out by qualified experts
who must be responsible for determining the tests necessary to check the
solutions adopted vis-à-vis the risks involved, and to check the observance of
all legal and regulatory obligations: in particular all the requirements of the EN
12445 standard which sets forth the test methods for checking automated
gates.
Additional devices must undergo specific testing, both in terms of functionality
as well as their correct interaction with HYKE; please refer to the relevant indi-
vidual instruction manuals.
5.1 - Testing
The sequence of steps to take to carry out testing refers to a typical system (
fig. 3
):
1
Ensure that everything stated in the “Installation warnings” chapter has
been observed.
2
Release the gearmotors manually and check that when you operate the
leaf, at the point designed especially for the manual manoeuvre, the leaves
can either be opened or closed with a force of less than 390 N.
3
Secure the gearmotors (see chapter 3.6).
4
Using the control devices (transmitter, command button, key selector, etc.),
perform some Gate Opening, Closing and Stop tests, making sure the
movement of the leaves corresponds with each test. It is a good idea to car-
ry out several tests in order to evaluate the movement of the leaves and pin-
point any assembly or adjustment defects as well as to check for any par-
ticular points of friction.
5
Check one by one that all the safety devices in the system work properly
(photocells, sensitive edges, etc.). When a device is activated, the “BLUE-
BUS” LED on the control unit emits two quicker flashes to confirm that
recognition has taken place.
6
If the hazardous situations caused by the movement of the leaves have
been safeguarded by limiting the force of impact, the force must be meas-
ured in accordance with the EN 12445 standard and, if necessary, if the
control of the “gearmotor force” is used as an aid to the system to reduce
the force of impact, try and then find the adjustment that achieves the best
results.
5.2 - Commissioning
Commissioning can only take place once all the testing phases have been
carried out successfully.
1
Put together the automation system’s technical file, which should include
the following documents: an overall diagram of the automation system, the
diagram of the electrical connections made, the current risk analysis and
the related solutions adopted, the manufacturer’s declaration of conformity
for all the devices used and the declaration of conformity filled in by the in -
staller.
2
Affix a data plate onto the gate which specifies the following information, at
least: the type of automation system, the name and address of the manu-
facturer (responsible for the commissioning), the serial number, the year of
manufacture and the EC mark.
3
Fill in the declaration of conformity of the automation system and hand it
over to its owner.
4
Fill in and hand over to the owner of the automation system the “
User’s
guide
” of the automation system.
5
Fill in and hand over to the owner of the automation system the “
Mainte-
nance schedule
” which contains instructions on the maintenance of all the
devices in the automation system.
6
Before commissioning the automation system, inform the owner of all the
hazards and residual risks entailed.
For all the documentation mentioned, the Nice technical support service
provides the following: instruction manuals, guides and precompiled forms.
Also visit: www.nice-service.com
TESTING AND COMMISSIONING
5
03.
Make sure that the flashing light flashes at intervals of 0.5 sec on, 0.5 sec
off during manoeuvres.
Summary of Contents for HK7024
Page 2: ......
Page 25: ...IX 1 2 3 4 320 mm 210 mm 290 mm ...
Page 27: ...XI 1 2 a b 3 9 5 OK OK b a 9 b a a b x 4 c a 4 1 2 3 4 90 90 10 7 6 8 ...
Page 28: ...XII 9 1 2 a b 3 10 5 b x 4 c a 4 8 b a 10 1 2 3 13 11 6 OK OK 7 ...
Page 29: ...XIII 1 2 90 3 90 12 A 90 2 1 3 12 B 4 OK 3 NO 2 NO 11 1 3 2 5 4 ...
Page 31: ...6 1 2 8 7 15 1 3 5 1 2 2 4 XV ...
Page 32: ...XVI 16 1 2 7 6 17 L1 OPEN STOP CLOSE L2 L3 L4 L5 L6 L7 L8 ...
Page 33: ...XVII 1 2 1 2 18 1 3 5 1 2 2 2 1 4 19 1 2 ...
Page 34: ...XVIII 1 2 20 1 4 1 2 3 2 ...