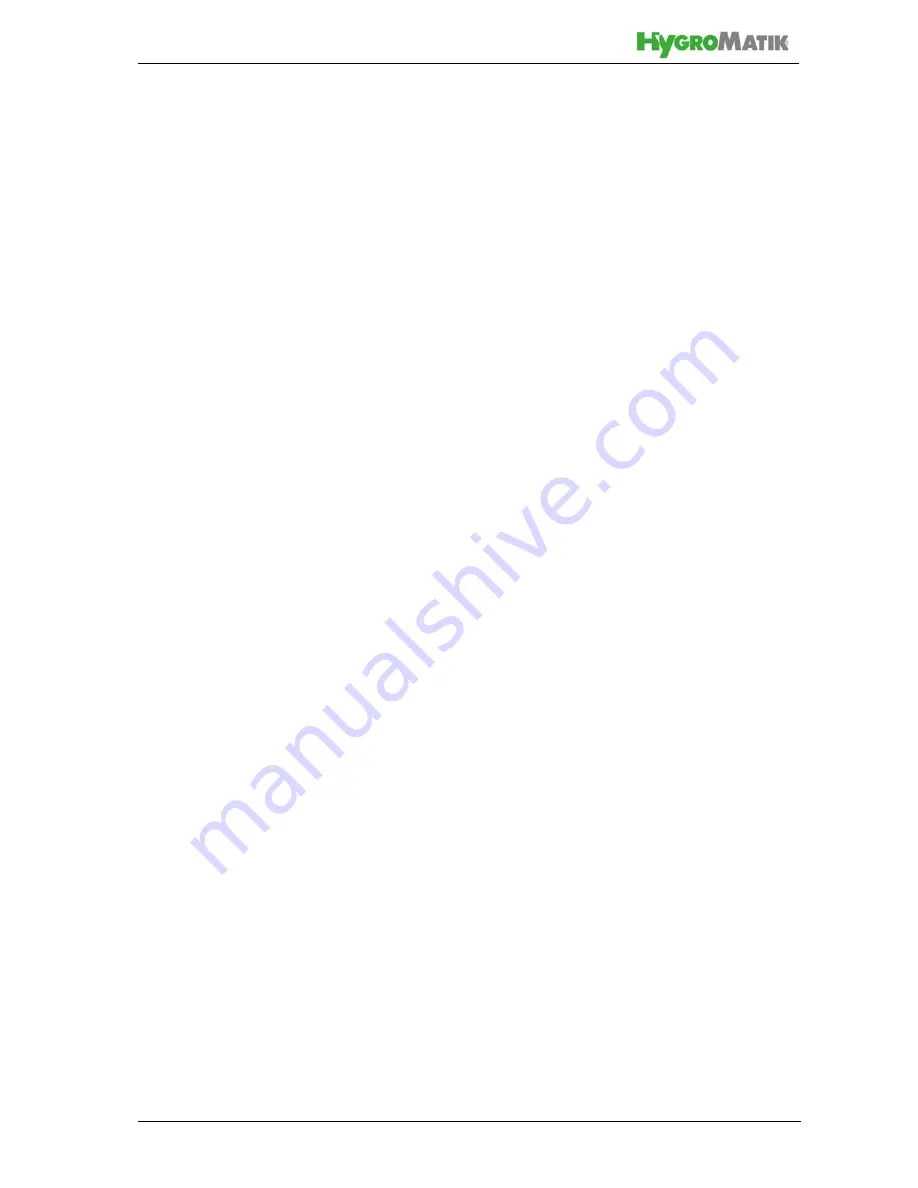
Page 59
Cleaning the steam hose adapter nozzle
From the top of the control cylinder a hose runs to the steam
hose adapter connecting piece. The nozzle integrated in the
connecting piece must be cleaned regularly otherwise blocking
by hardeners might occur.
8.6
Replacing Heater Elements
Removal
»
Remove and open the steam cylinder as described
above in section “Removing and Cleaning the Steam
Cylinder.”
»
Detach connecting cable for the heater element in
question. Mark these two terminals.
»
If necessary, remove the capillary tube of the thermo
sensor from the heater element by detaching the
retainer clips.
»
Detach the heater element from the cover by removing
the nut and adjusting washer.
»
If present detach cable lug for grounding.
»
Pull heater element downward out of the steam cylin-
der.
»
Clean the sealing surface on the underside of the cover
around the area where the new heater element will be
installed.
Installation
»
Install new heater element (with sealing), replacing the
parts in the correct sequence, and screw nut.
»
Insert the heater element’s connecting cable into the
two marked terminals and tighten. Polarity of (heater
element) connecting cable is not important.
»
If necessary: Install capillary tube of the thermo sensor
on the heater element using retainer clips.
»
To proceed further, follow the steps described above in
section “Removing and Cleaning the Steam Cylinder”.
Summary of Contents for HeaterCompact HC02
Page 69: ...Page 69 10 EC Declaration of Conformity...
Page 76: ...Page 76 13 Exploded View...