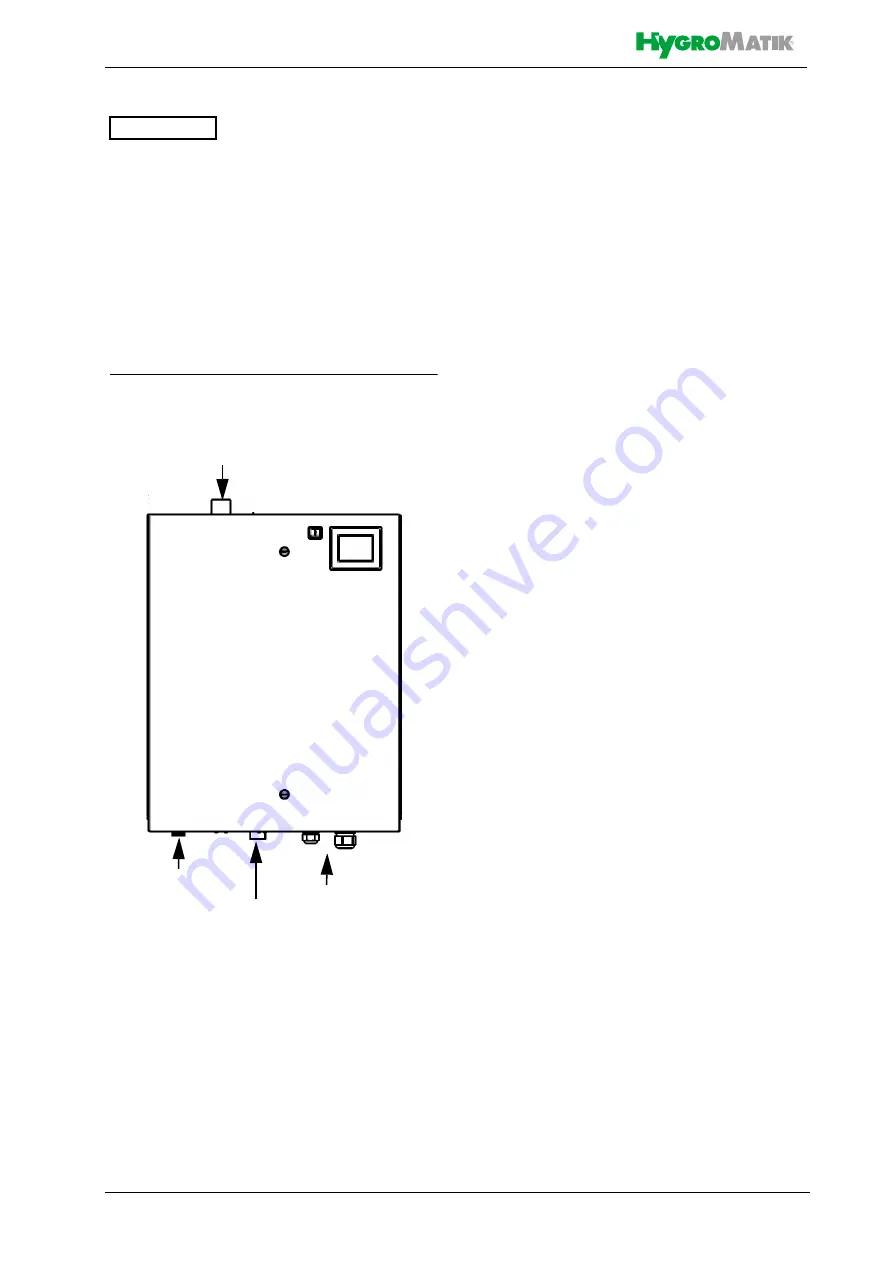
Page 16
•
To function properly, the steam humidi-
fier must hang level and plumb.
•
When choosing the installation loca-
tion, consider the necessary distance
between the unit and existing designa-
ted paths. This should be at least 60
cm.
•
The mounting wall must be made of a
temperature-resistant material, as the
enclosure can heat up to 70°C.
Device connections:
Please note
Cable entries
1¼“ Waste water connection
¾“ Water inlet
DN25, DN40 Steam outlet