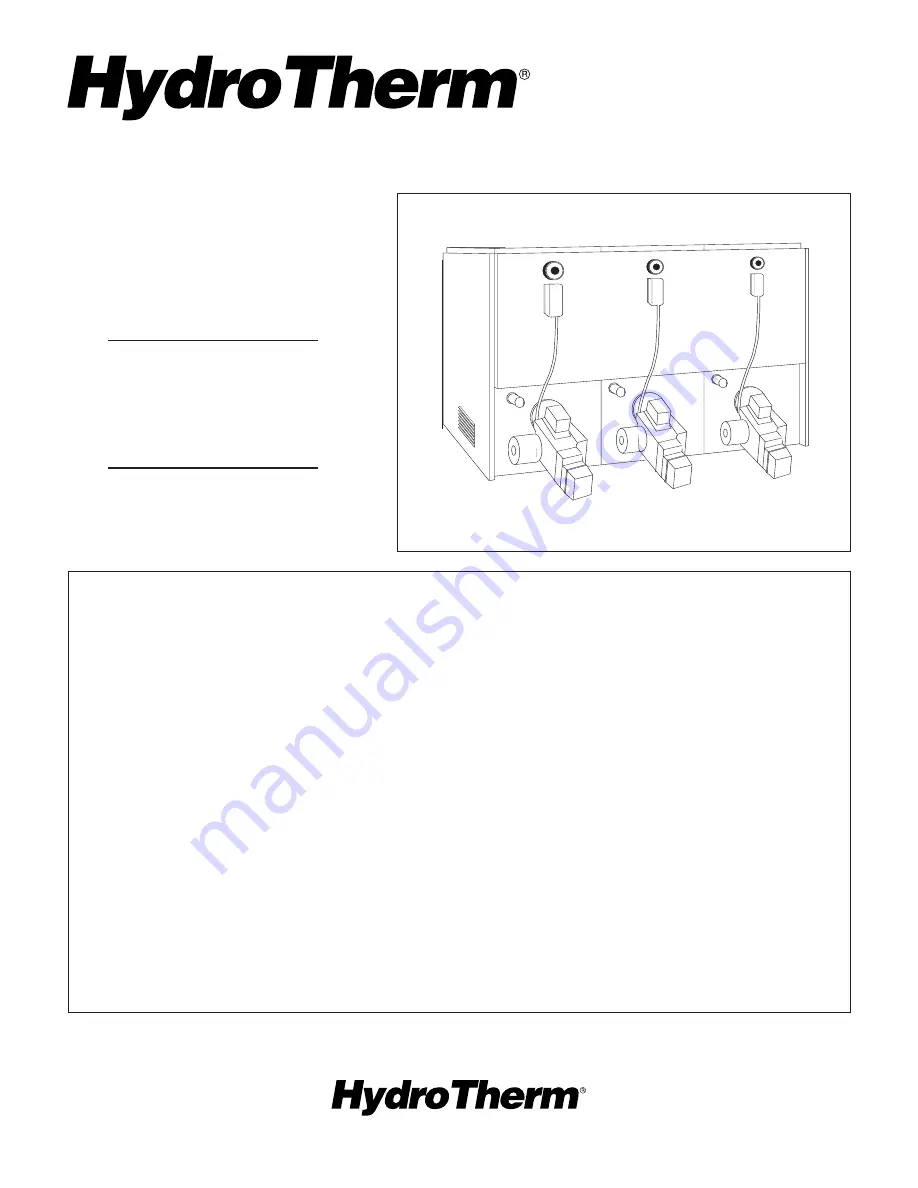
MG2-605
42-9158
AAA
AAA
AAA
AAA
AAA
AA
AA
AA
AA
AA
AA
AA
AA
AA
AA
IN UNITED STATES: 260 NORTH ELM ST., WESTFIELD, MA 01085 • (413) 568-9571/FAX (413) 568-9613
IN CANADA: 5211 CREEKBANK ROAD, MISSISSAUGA, ONT L4W 1R3 • (905) 625-2991/FAX (905) 625-6610
MG SERIES
INSTALLATION MANUAL
AND REPLACEMENT
PARTS LIST
Modular Power Gas Cast
Iron Water Heating Plants
770,000 to 2,310,000
Btuh Input
SECTION 1: INTRODUCTION
Heating Plant Design............................................
2
Code Compliance.................................................
2
Heating Plant Shipment........................................
2
Heating Plant Dimensions.....................................
3
SECTION 2: INSTALLING MODULES
Step 1: Planning Ahead.........................................
4
Step 2: Arranging Heating Plant............................
5
Step 3: Setting & Aligning Modules.......................
5
SECTION 3: INSTALLING WATER PIPING
Step 1: Planning Ahead.........................................
6
Step 2: MC Heat Exchangers................................
6
Step 3: Supply & Return Headers..........................
6
Step 4: Hydronic Components...............................
7
Step 5: Hydrotesting The System..........................
8
SECTION 4: VENTING THE HEATING PLANT
Step 1: Planning Ahead........................................ 11
Step 2: Draft Regulators, Vent Connectors
& Slip Joints............................................. 12
Step 3: Breeching Runs.......................................
13
SECTION 5: INSTALLING JACKETS
Jacket Assembly...................................................
14
SECTION 6: INSTALLING BURNER
Burner Requirements...........................................
15
SECTION 7: INSTALLING GAS PIPING
Step 1: Gas Main & Gas Headers........................ 15
Step 2: Test Gas Piping........................................
16
SECTION 8: WIRING THE HEATING PLANT
Wiring Requirements............................................ 16
SECTION 9: HEATING PLANT START-UP
Step 1: Planning Ahead........................................ 17
Step 2: Start-Up & Adjustments............................ 17
APPENDICES
A: Breeching/Chimney Sizing...............................
18
B: Gas Pipe Sizing................................................ 20
C: Control Guidelines............................................ 22
REPLACEMENT PARTS
27
NOTE: If shop drawings have not been provided, refer to the Appendices at the rear of this manual for sizing
(breeching, chimney & gas piping) and control system data.
Applicable For Larger Heating
Plants Using Boiler Banks
Of 6-Modules Or Less