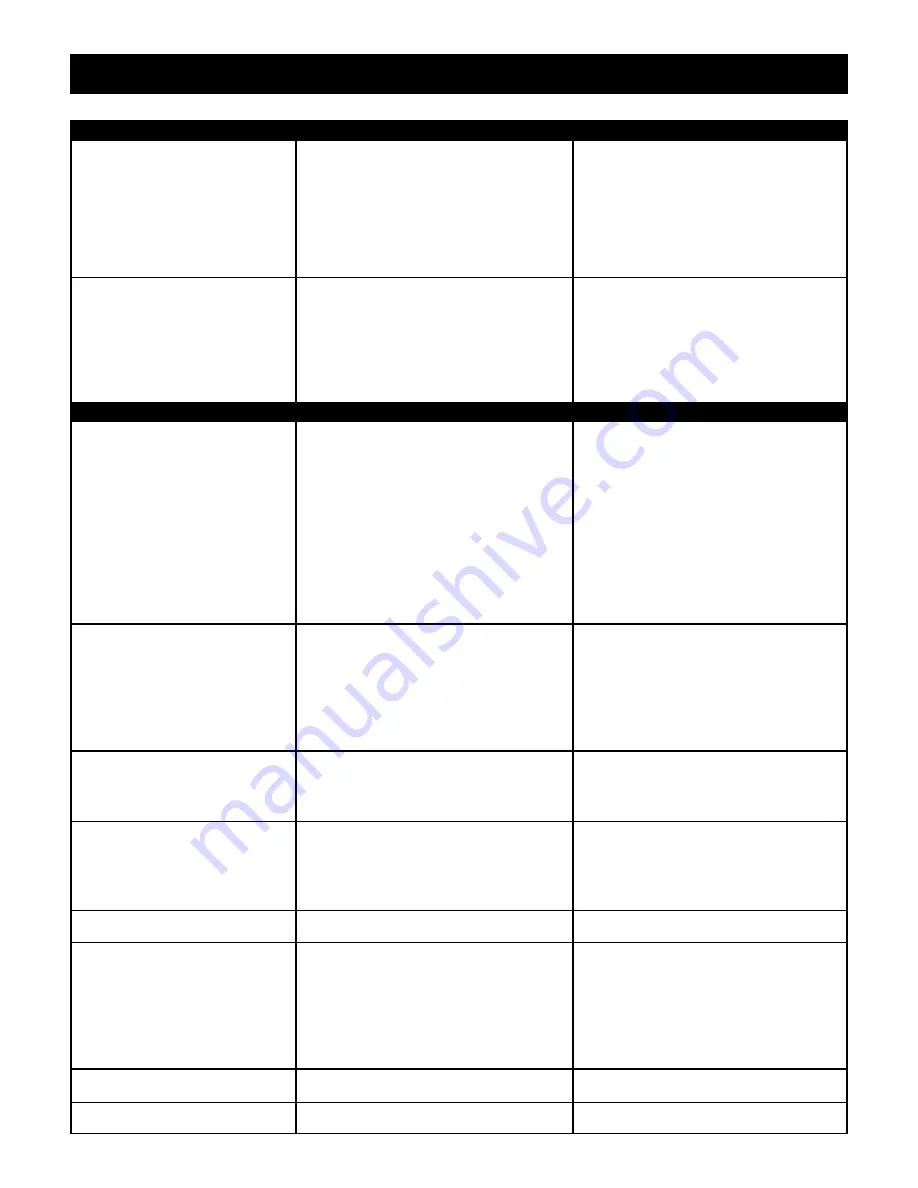
TROUBLE SHOOTING GUIDE
13
PROBLEM
PROBABLE CAUSE*
REMEDY
Check cord, plug, socket, and breaker. Check
Voltage
Reset manual overload by depressing the thermal
switch on the outside of the motor or starter after
the motor has cooled. CAUTION! Automatic overload
will restart the motor automatically when it has
cooled.
Check power switch.
Replace or repair motor and/or wiring.
25 PSI minimum.
Descale coil for better water flow.
Remove spray nozzle and pull trigger to check
auto-start function.
Check mechanical function & electrical signal to
relay.
Clean obstruction or scale deposits from coil
with coil cleaner.
Install Nozzle.
Dual wand valve must be closed and high
pressure nozzle installed.
Replace hose, quick coupler, or o-ring in the
quick coupler.
Close Valve
Clean and check more frequently.
Replace nozzle of proper size.
Tighten or replace with correct belt.
Install pressure gauge on pump head to adjust
pressure. Check valve seat on Unloader.
Reseal fittings and inspect inlet hoses for air leaks.
Increase water supply flow.
Clean out or replace worn valves.
Check fittings and hose for air tight seal, clean
inlet strainer screen.
Replace seals.
Pressure feed the pump and replace L.P. seals
if water leaks from the pump head.
Replace pump or bearing.
Locate point of oil leakage and replace damaged
O-ring or seal.
No electric power.
Thermal overload in the motor/or starter has
been tripped.
Power switch inoperative.
Electric motor or wiring failure.
Must have adequate water supply.
Coil scale build up.
Check filter screen & inlet pressure.
Inlet Flowswitch damaged or jammed with debris
Nozzle not installed.
Dual wand valve is open.
Leaky discharge hose or quick coupler.
Chemical Valve open
Inlet strainer clogged.
Worn, plugged or wrong size nozzle.
Belt slippage.
Unloader valve worn or improperly adjusted.
Air leak in inlet plumbing.
Inadequate incoming water supply.
Stuck inlet or discharge valves.
Restricted inlet or air entering the inlet plumbing
on the pump.
Leaking H.P. seals.
Leaking L.P. seals.
Broken or worn bearing or connecting rod in
crankcase.
Loose drain plug or damaged seal.
* The most recurring probable cause is listed first. Repairs should be made only by a qualified technician.
Electric motor does not start.
Machine will not Auto-Start (if equipped)
Pump runs but has low spray pressure.
Pump runs but there is erratic,
fluctuating pressure.
Excessive crankshaft play or loud,
knocking noise in pump.
Oil leaking from pump.
Pumping System
Power System: Electric Motor Driven
Inlet injection will not siphon chemical.
Water is emitted from the chemical
pickup tube.
Downstream injector will not siphon
chemical.
Pressure relief relieving water.
Check valve in the strainer clogged.
Chemical valve not open or clogged.
Strainer not submerged in solution.
Detergent hose cut or Kinked.
Check Valve malfunctioning.
Brass knob on injector is closed.
Unit not in low pressure mode.
Soap solution too thick.
Detergent hose cut or Kinked.
Strainer plugged or not submerged.
Internal injector parts corroded or stuck.
Outlet water temperature too high.
Unloader failure/ Coil overheating/ excessive
pressure
Clean or replace. Rinse after each use.
Open Chemical valve or clean.
Submerge strainer and replenish chemical.
Inspect hose, replace as necessary.
Repair or replace check valve.
Open by turning counter clockwise.
Open dual wand or install low pressure tip.
Dilute or use different soap.
Inspect hose, replace as required.
Check screen on strainer pickup tube.
Disassemble, clean or replace.
Use with cold water (150 Degrees F. Max.) If
installed on discharge side of coil.
Turn machine off, wait a few minutes and
restart. If problem continues take in for repair.
Burst Disk Relieving water
Excessive overpressurization and
system spikes
Take it in for system check