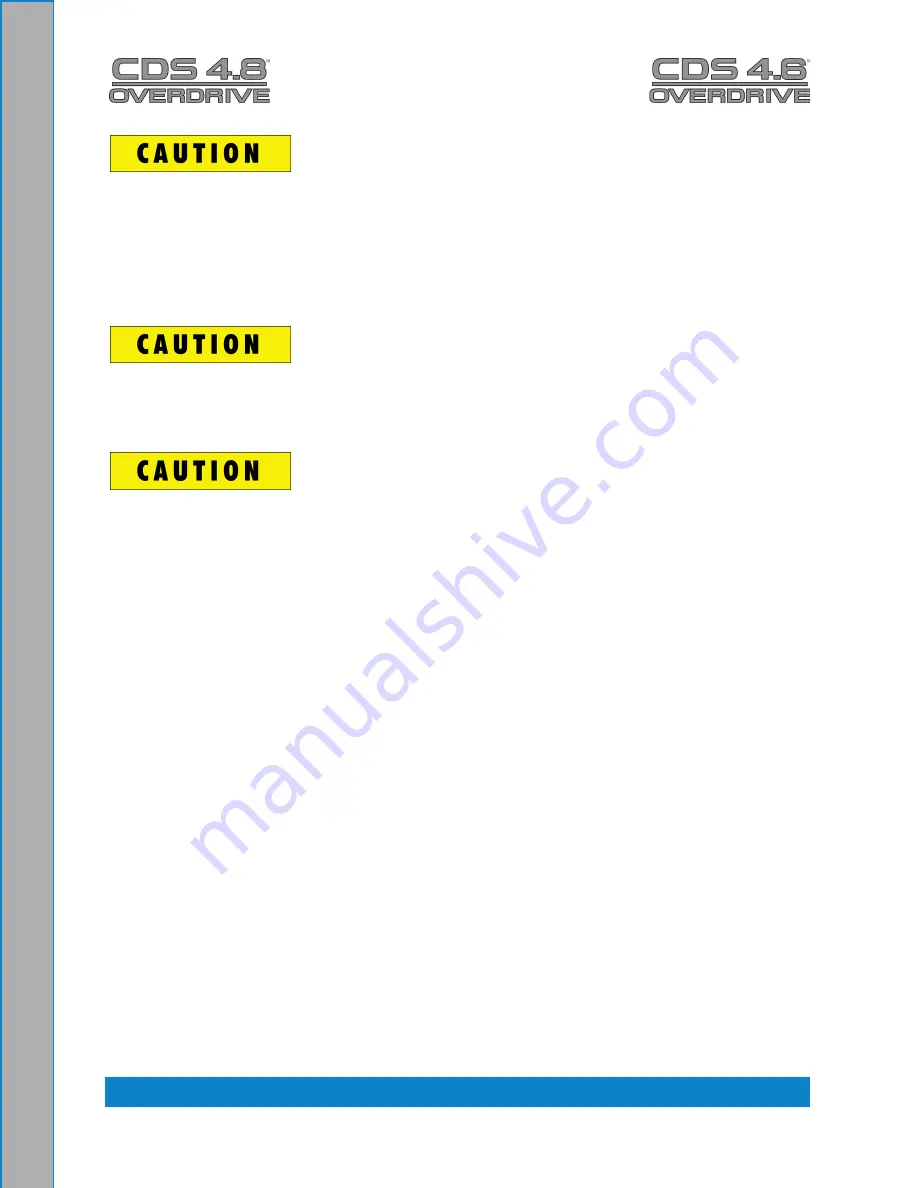
Vacuum Blower System: 8-2
To protect the vacuum blower from overloading and damaging itself, there is a vacuum
relief system installed on the vacuum recovery tank. When the vacuum tank inlet is
completely sealed off, a maximum of 14” Hg will be attained. At the end of each day,
spray an oil-based lubricant into the blower lubrication port before shutting down the
machine. If you fail to lubricate the vacuum blower on a daily basis, rust deposits and
moisture can form and decrease the life of the vacuum blower.
foam passing through the blower could lead to serious problems. Therefore, it is
important to keep the vacuum tank foam free. When cleaning surfaces with excessive
foaming residue, use HydraMaster’s Defoamer as directed.
The vacuum tank is protected from excessive water level overflowing by a vacuum tank
float kill switch. The switch is not activated by foam, only by liquid.
VACUUM TANK INLET FILTER
HydraMaster inlet filter screens are designed to trap lint, hair and large objects that would
normally collect at the bottom of your vacuum tank. Clean the screen at the end of each
job to eliminate build-up of debris in the tank.
VACUUM BLOWER LUBRICATION
Read the vacuum blower owner’s Manual, included with the CDS 4.8 / 4.6 owner’s
Manual, for proper oil changing instructions. Because the CDS is very demanding of
the vacuum blower, the vacuum blower should be maintained as recommended in the
vacuum blower owner’s Manual.
Remember to:
Remove vented oil fill plug on front or rear oil case.
1.
Fill with specified oil until it registers to the top of the sight glass.
2.
use lubricants as listed in the Table 8-1.
3.
Add fresh oil as required to maintain proper level.
4.
The oil should be drained, flushed and replaced every 300 hours. The oil drain hose is
connected under the head plate; at the end of the oil drain hose is a cap.
Summary of Contents for CDS 4.6
Page 44: ...Assemblies and Parts Lists 7 2 CDS Machine Assembly Rear View Figure 7 2 7145 Rev C ...
Page 46: ...Assemblies and Parts Lists 7 4 CDS Recovery Tank Assembly Front View Figure 7 2 6977 Rev B ...
Page 47: ...7 5 Assemblies and Parts Lists CDS Recovery Tank Assembly Rear View Figure 7 3 6977 Rev B ...
Page 50: ...Assemblies and Parts Lists 7 8 CDS Instrument Panel Assembly Front View Figure 7 5 6988 Rev C ...
Page 51: ...7 9 Assemblies and Parts Lists CDS Instrument Panel Assembly Rear View Figure 7 6 6988 Rev C ...
Page 61: ...7 19 Assemblies and Parts Lists CDS Pump Assembly Overview Figure 7 13 7429 Rev A ...
Page 65: ...7 23 Assemblies and Parts Lists CDS Dash Box Assembly Overall View Figure 7 16 7428 Rev A ...
Page 66: ...Assemblies and Parts Lists 7 24 CDS Dash Box Assembly Figure 7 17 Rear View 7428 Rev A ...
Page 68: ...Assemblies and Parts Lists 7 26 CDS Dash Panel Assembly Overall View Figure 7 18 7427 ...
Page 70: ...Assemblies and Parts Lists 7 28 CDS Water Box Assembly Overview Figure 7 20 6990 Rev C ...
Page 71: ...7 29 Assemblies and Parts Lists CDS Water Box Assembly Figure 7 21 Parts View 6990 Rev C ...
Page 101: ...7 59 Assemblies and Parts Lists Hydra Hoe Wand Assembly Figure 7 46 2660 ...
Page 110: ...Electrical System 9 2 Figure 9 1 CDS Electrical Schematic 7425 Rev B ...
Page 111: ...9 3 Electrical System Figure 9 2 CDS Wiring Diagram 7426 Sht 2 Rev C ...
Page 112: ...Electrical System 9 4 Figure 9 3 CDS Wiring Diagram 7426 Sht 3 Rev C ...