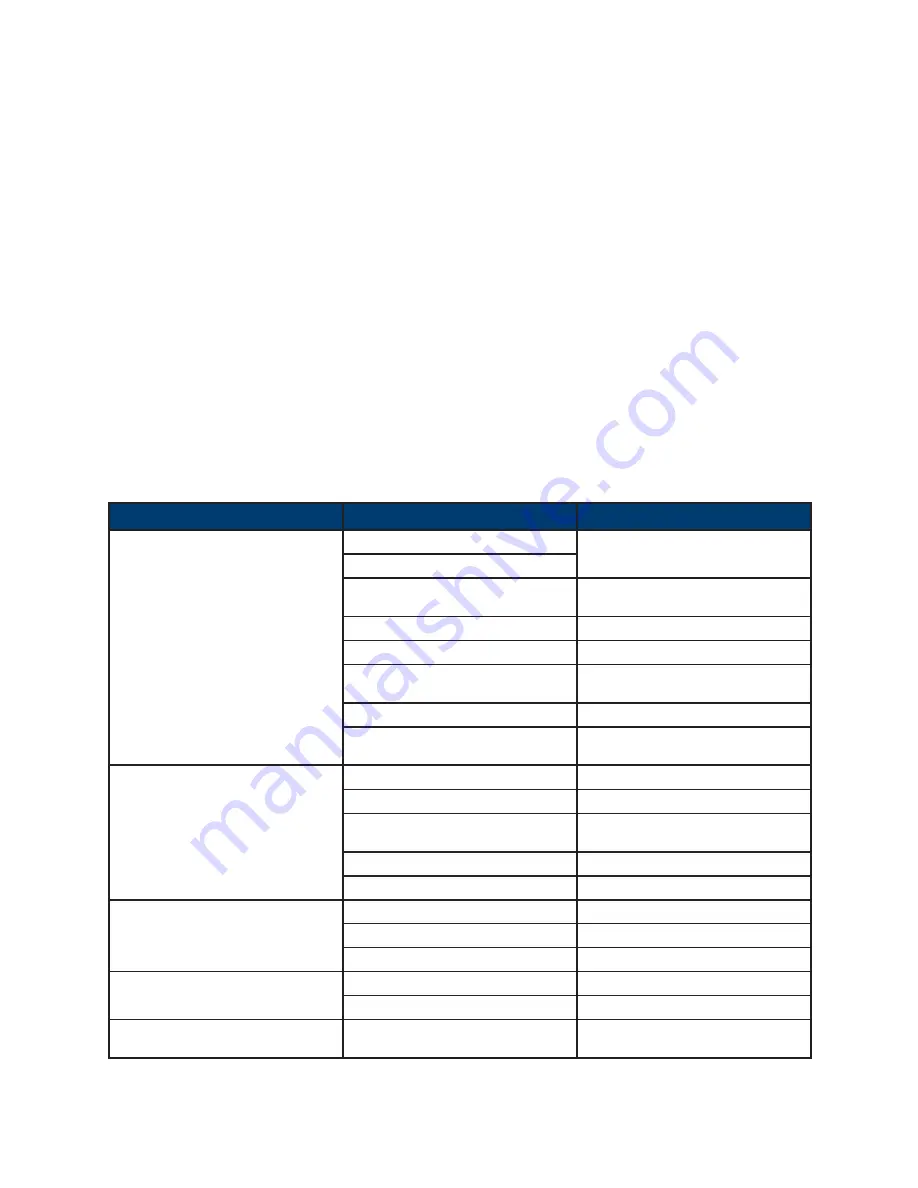
© Hydra-Flex, Inc. 2017
Page | 8
TROUBLESHOOTING
The AQUA-LAB is supplied with the following tools to assist in set up and troubleshooting:
• Vacuum gauge for checking the vacuum at the chemical injector hose barb,
• Back Pressure Gauge for measuring back pressure downstream of the injector.
PROBLEM
POTENTIAL CAUSED
SOLUTIONS
Pump Operates, but delivers little or no
water
Inlet Restriction
Check all in-line filters and inlet plumbing
for restrictions
Low line voltage
Inadequate water supply
Check pressure on inlet side of pump to
be sure positive pressure is maintained
Undersized piping
Replace with larger piping
Leak on the Inlet side
Make sure connections are tight
Worn or defective pump parts
Replace worn parts or entire pump,
Clean parts if required
Pump not primed
See priming instructions
Incorrect Motor rotation
Reverse motor rotation by interchanging
any two leads
Pump won’t start or run at full speed
Blown fuse or circuit breaker
Replaced fuses or close circuit breaker
Defective Motor Starter contactor
Replaced motor starter contactor
Incorrect Motor Voltage
Voltage must be within 10% of motor
rated voltage
Defective motor
Replace motor
Pump components damaged
Replace worn part or entire pump
Excessive Noise from Pump
Pump not secured firmly
Secure properly
Restricted Inlet
Clean or correct restriction
Cavitation (Sounds like marbles in pump)
Increase inlet size
Pump Leaks
Worn mechanical seal
Replace shaft seal
Worn o-ring seals
Replace
Injector is not drawing chemical -
Passes
Vacuum Pressure check test
Clogged chemical feed
Check chemical hose, foot valve, meter-
ing tip and hose barb for debris or clogs
INDIVIDUAL INJECTOR FLOW RATE MEASUREMENT
1.
Attach a short section of tubing (3-5 ft) to the outlet of the injector that you want to measure the flow
rate of.
2.
Turn on the Aqua-Lab pump and the solenoid valve for the Injector being tested. If possible have
someone assist by turning them on while you keep the water from the short section of hose pointed
in a safe direction.
3.
Using a 2 liter graduated cylinder (or other large graduated cylinder) and a stop watch (watch or cell
phone with a stop watch)
•
Make sure the graduated cylinder is empty and that the stop watch is cleared.
•
Direct the flow of water from the tube into the graduated cylinder and start the stop watch the
instant you start adding water to the cylinder.
•
Stop the timer when the cylinder is at least half full, preferably at a whole number level (ie. 1 liter,
2 liters)
•
Divide the number of liters by the time in seconds then multiply by 15.85 – this will result in how
many Gallons per minute (GPM)