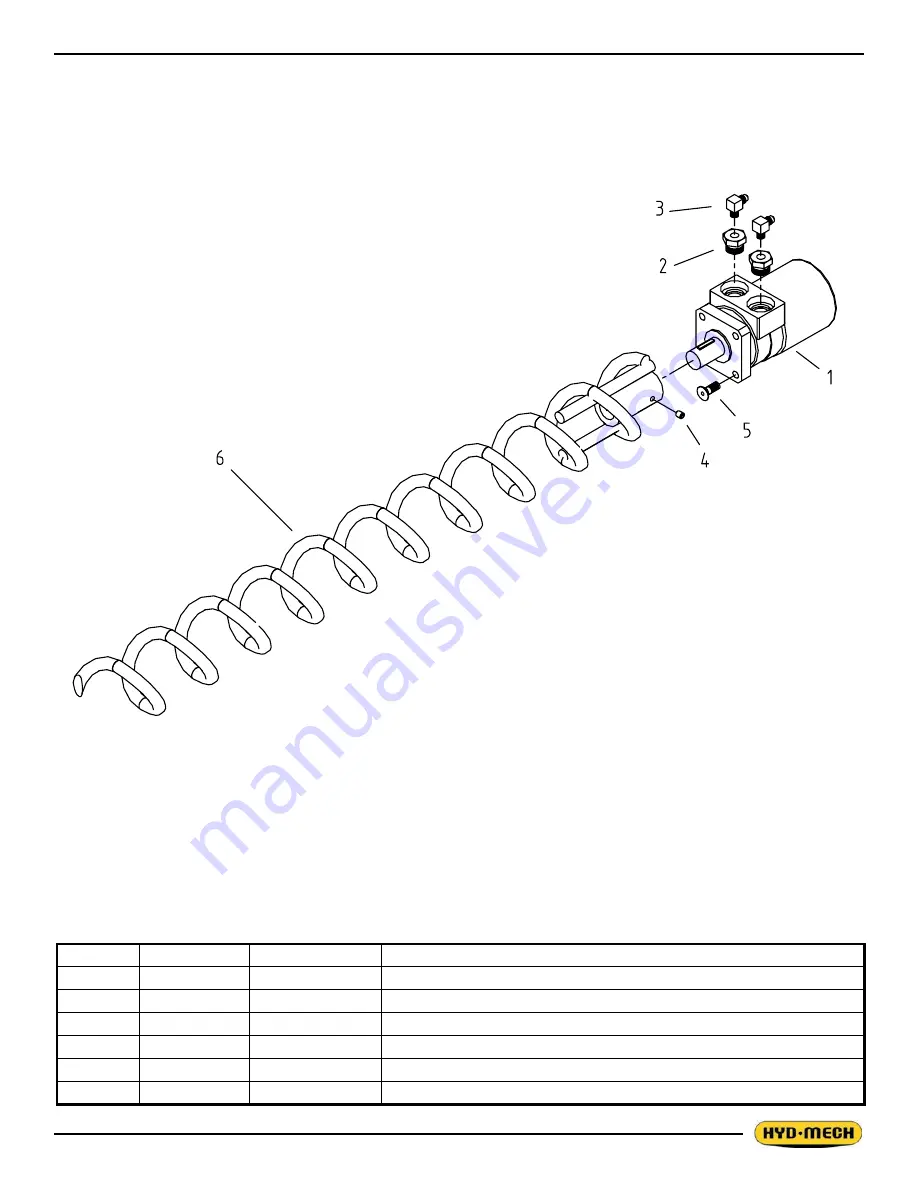
6.7
CHIP aUGER assEMblY
ITEM
QUanTITY
PaRT nUMbER
DEsCRIPTIon
362690
MOTOR, HYDRAULIC
2
2
360465
FITTING, HYDRAULIC, STEEL, 90, 2503-6-4
3
2
360535
FITTING, HYDRAULIC, STEEL, ELBOW ADAPTER, 203-4-4
4
393965
SCREW, SET, CUP POINT, 0.32 - 8 x 0.25
5
4
390630
BOLT, SOCKET HEAD, FLAT, 0.325 - 8 x .00
6
H4-2-00A
WELDMENT, AUGER
Summary of Contents for H-14P
Page 2: ......
Page 16: ......
Page 30: ......
Page 40: ......
Page 46: ...4 6 H 14P ELECTRICAL SCHEMATICS 208 240 VAC ...
Page 47: ...4 7 ...
Page 48: ...4 8 ...
Page 49: ...4 9 ...
Page 50: ...4 10 ...
Page 51: ...4 11 ...
Page 52: ...4 12 ...
Page 53: ...4 13 ...
Page 54: ...4 14 H 14P ELECTRICAL SCHEMATICS 480 575 VAC ...
Page 55: ...4 15 ...
Page 56: ...4 16 ...
Page 57: ...4 17 ...
Page 58: ...4 18 ...
Page 59: ...4 19 ...
Page 60: ...4 20 ...
Page 62: ...5 2 GLAND ASSEMBLIES PISTON ASSEMBLIES ...
Page 63: ...5 3 HYDRAULIC SCHEMATIC ...
Page 64: ...5 4 HYDRAULIC PLUMBING DIAGRAM ...
Page 65: ...5 5 ...
Page 66: ...5 6 ...
Page 67: ...5 7 ...
Page 68: ......
Page 76: ...6 8 FRONT VISE ASSEMBLY ...
Page 79: ...6 11 ...
Page 80: ...6 12 BONFIGLIOLI A412 GEARBOX ASSEMBLY ...
Page 81: ...6 13 ...
Page 86: ......
Page 88: ...8 2 H 14P LAYOUT DRAWING ...