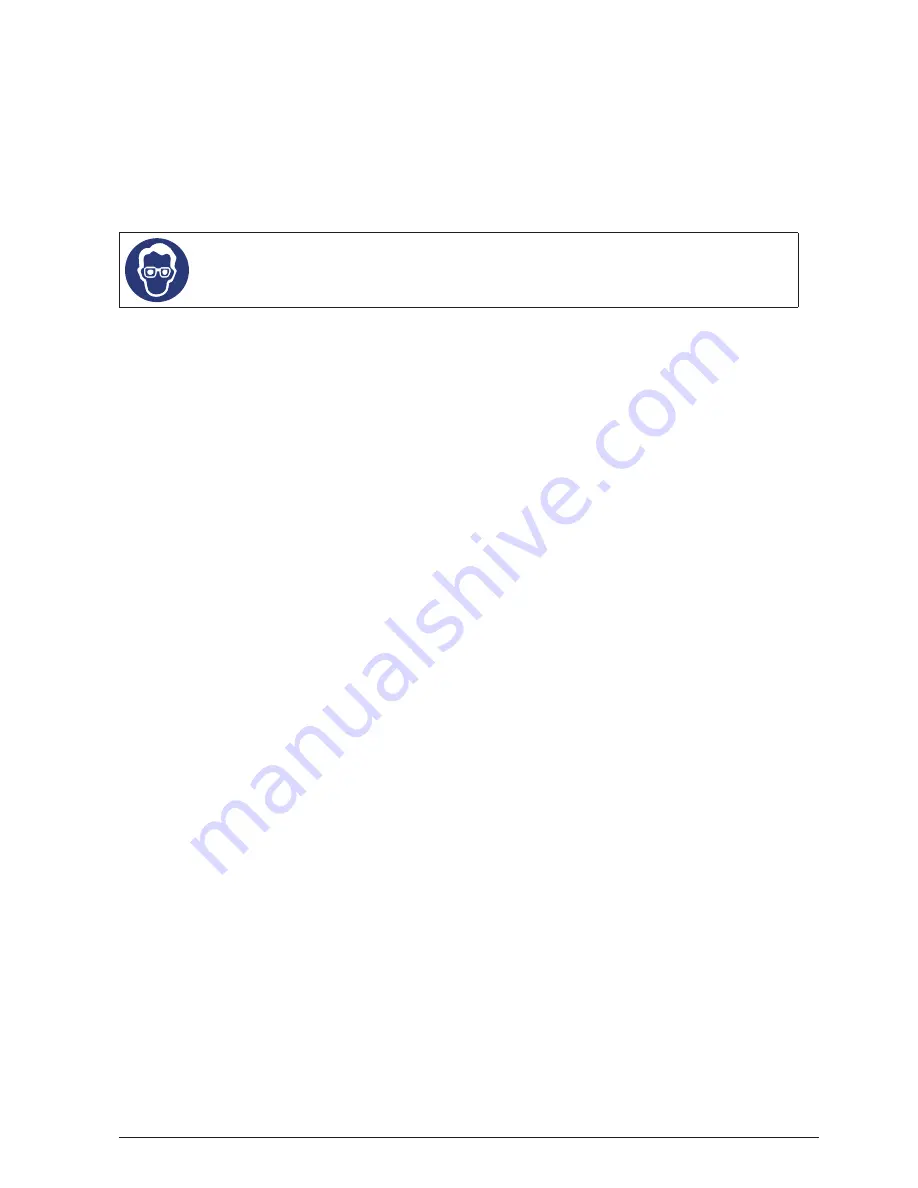
12
CHANGES AND T YPING ERRORS RESERVED
CHANGES AND T YPING ERRORS RESERVED
Additional safety rules
Always keep in mind that:
•
the machine must be switched off and disconnected from the power supply during maintenance and repairs,
•
clamped workpieces may only be measured when the machine is switched off.
Never lean over the machine, mind loose clothing, ties, jewellery etc. and wear a cap.
Do not remove safety devices or guards. Never use the machine while a guard is open.
Always use safety glasses for machining rough materials.
Burrs and chips should only be removed using a sweeper or other aid, never with your bare hands!
Never leave the machine running unattended.
Always wear safety glasses!
2. a
TTenTion
2.1. s
afeTy
Please read the operation manual carefully before the installation and adjustment of the machine. When the
installation is finished, check all components and perform an idle trial run before putting the machine into
operation. In case of problems, please contact your Huvema dealer.
2.2. c
auTion
Make sure you read all the safety instructions and follow them carefully.
3. m
achine
appearance
,
applicaTions
and
work
environmenT
3.1. m
achine
appearance
The machine design encompasses the gear box, spindle box, column, work table, bracket, base and electrical
cabinet. The gear box is atop the spindle box. The spindle box is mounted on top of the column. The work table
is supported by the bracket, which is assembled in the middle of the column. The column sits on the base. The
electrical cabinet is situated at the back of the spindle box.
Picture A – Outline drawing
A1
Electrical cabinet
A5
Work table
A2 Gear
box
A6 Bracket
A3 Spindle
box
A7 Base
A4 Column
3.2. a
pplicaTions
This machine is designed for drilling, broaching, reaming, tapping, boring and similar operations. The large
drilling capacity allows for drilling of workpieces within a large size range. The machine is suitable for production
and maintenance shops. The worktable bracket can move up and down along the column at 180°, or 45° parallel
to the bracket. This design is very flexible and easy to operate.
3.3. w
ork
environmenT
•
The elevation of the workshop must be 2000 m or less.
•
The environmental temperature should be 20° C to 40 ° C.
•
With a medium temperature of 20 5° C, the relative humidity should not exceed 85 %.
•
No conductive dust allowed.
•
Installation in an environment with explosion danger is forbidden.
•
No corrosive gas or steam which may corrode metal or damage the insulation.
•
Keep away from the source of shocks or vibration.
Summary of Contents for HU 40 TI
Page 1: ...HU 40 TI HU 40 TI D R I L L I N G M M A C H I N E S...
Page 2: ...2 A B C A1 A2 A3 A4 A5 A6 A7 CHANGES AND TYPING ERRORS RESERVED...
Page 3: ...3 D E CHANGES AND TYPING ERRORS RESERVED...
Page 4: ...4 F G H CHANGES AND TYPING ERRORS RESERVED...
Page 5: ...5 I J3 J2 J1 J4 CHANGES AND TYPING ERRORS RESERVED...
Page 6: ...6 K L CHANGES AND TYPING ERRORS RESERVED...
Page 7: ...7 M CHANGES AND TYPING ERRORS RESERVED...
Page 8: ...8 N CHANGES AND TYPING ERRORS RESERVED...
Page 9: ...9 O CHANGES AND TYPING ERRORS RESERVED...
Page 23: ...23 CHANGES AND TYPING ERRORS RESERVED...
Page 26: ...26 CHANGES AND TYPING ERRORS RESERVED...
Page 27: ...27 CHANGES AND TYPING ERRORS RESERVED...
Page 28: ...2014 V1...